Tramp Metal Removed from Reclaimed Kaolin
By Paul Fears | 16 March 2020
A major UK mineral processing company has installed two large Bullet Magnets to remove tramp ferrous metal from dry reclaimed kaolin.
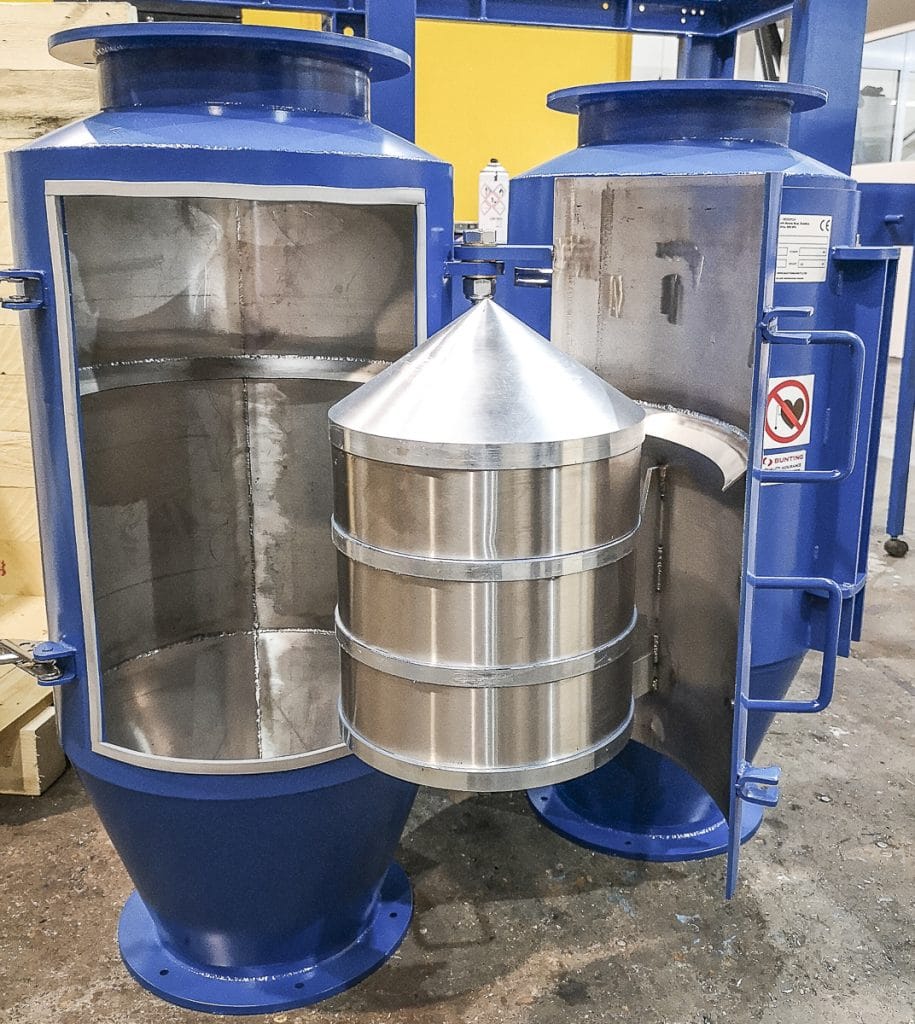
After initial discussions, Bunting conducted controlled tests in the Redditch Centre-of-Excellence. The reclaimed kaolin had a broad particle size range, with 95% below 250 microns. Iron contamination was approximately 1000ppm (although it could peak at 2000ppm) and the client was aiming to reduce this to below 120ppm.
Controlled Laboratory Tests
The laboratory tests concluded that the flow characteristics of the material did not suit dry-process Magnetic Separators such as Drum Magnets and Rare Earth Roll Magnetic Separators. Previous project experience indicated that material with such a particle size distribution would normally be processed in a wet slurry state. However, due to the customer’s process and end market requirements, the material needed to be handled in a dry state.
The tests also identified that the contamination was ferromagnetic iron, which probably originated in the ball mills.
Recommending Bullet Magnets
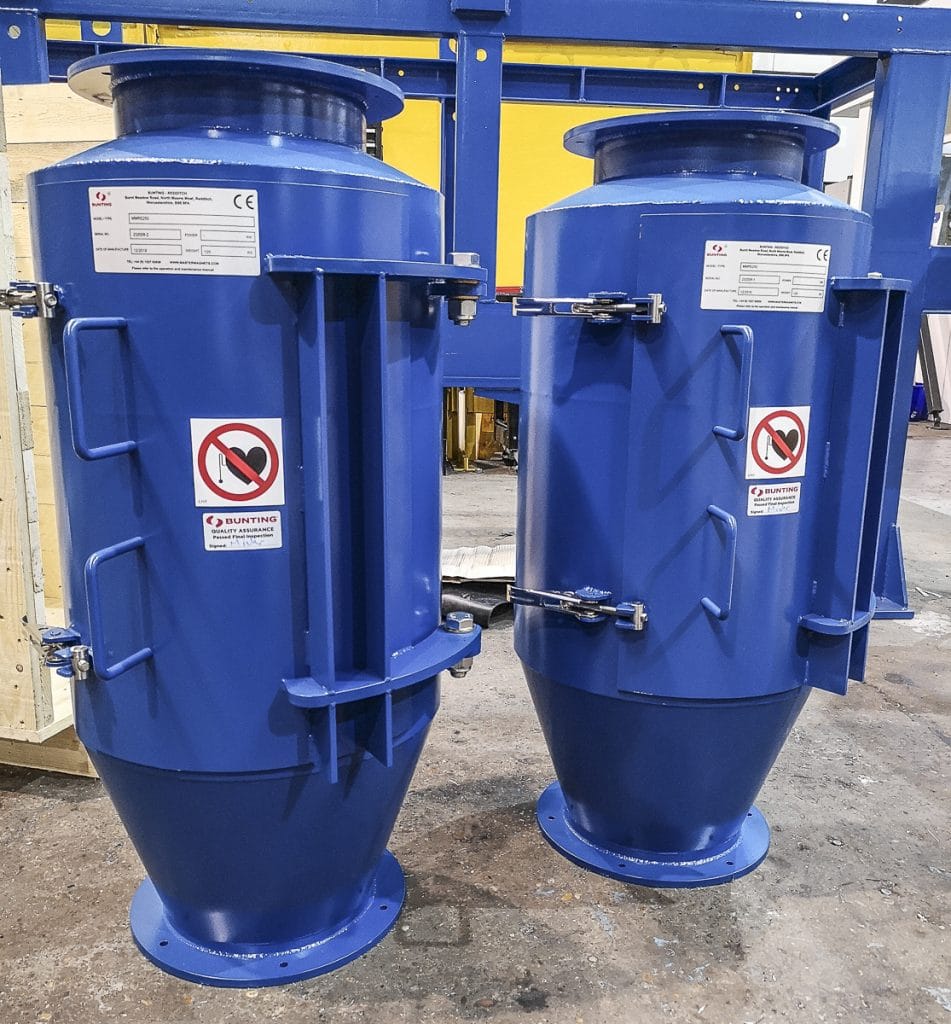
Subsequently, Bunting’s application engineers thought laterally and proposed magnetic separation technology successfully used successfully in the flour industry.
Bullet Magnets feature a magnetic cone centralised in a housing that fits into pneumatic and gravity fed pipelines. High strength designs, using Rare Earth Magnets, produce magnetic fields strong enough to capture fine iron. Once captured, the iron is held on the surface of the magnetic cone until manually cleaned during scheduled maintenance.
For this kaolin application and to maximise iron separation, the two Bullet Magnets were positioned in series. Approximately 4tph of kaolin would be gravity fed via a screw conveyor through the two Bullet Magnets.
To suit the capacity, Bunting recommended two Model MM250RE Bullet Magnets, both fitted with PN16 flanges. Each one is 950mm long and weighs 145kg. The magnetic cone is centrally housed inside a non-magnetic stainless-steel body and mounted to a hinged door for easy access and cleaning.
In operation, kaolin flows under gravity down from the screw conveyor through the Bullet Magnet, with all the material travelling through the strong magnetic field. The ferromagnetic iron particles are attracted to the surface of the cone magnet and separated from the non-magnetic kaolin.
Related Mineral Processing Technical Articles
Magnetic Separators – Mineral Processing Laboratory
Bunting-Redditch has one of the most comprehensive magnetic separation mineral processing testing laboratories in the world. Their Laboratory Technicians have decades of experience in mineral processing. Controlled tests ensure that the most suitable and cost-effective machinery is recommended for each application. The laboratory is equipment with a wide range of equipment including:
- Smaller scaled versions of industrial Magnetic Separators. This equipment is used to accurately scale up to industrial capacities and calculate performance guarantees;
- X-Ray Fluorescence and X-Ray Diffraction analysis are available for chemical assay and mineralogical identification to aid the development of a viable process route for each application;
For further information on our range of magnetic separation equipment designed for purifying ceramics and non-metallic minerals, or to arrange sample tests in our laboratory, please contact us on:
Email: Gordon Kerr at GKerr@buntingmagnetics.com
Telephone: +44 (0) 1527 65858
To keep up to date with our news and technical reports, please follow us on social media