Separating Metal When Recycling Wood
By Paul Fears | 24 January 2022
Wood is one of the most recyclable materials of all waste. Waste wood originating from well-used wooden products such as pallets and furniture is reused in furniture, in creating building materials, animal bedding, and fuel. However, both ferrous and non-ferrous metal contaminates wood from secondary sources.
Separating Metal Contamination
Problematic metal contamination occurs in many forms such as nails, screws, and fixings. Removal of the majority of metal occurs after at least one stage of shredding, where the contamination is liberated and free for separation.
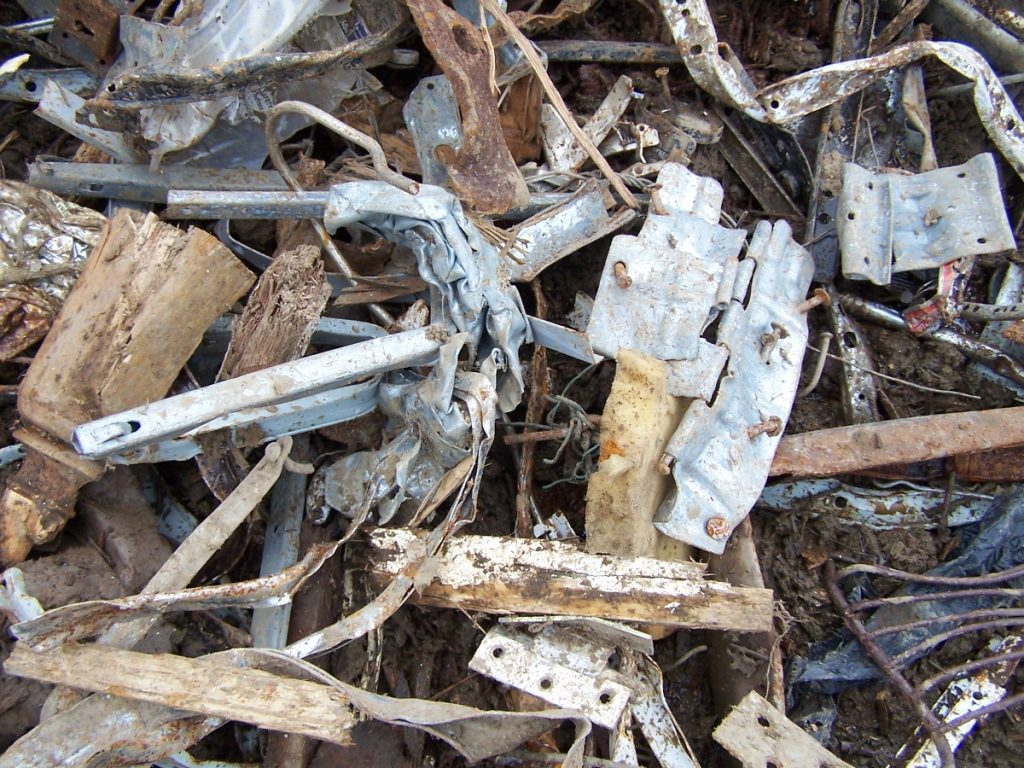
As with most separation processes, several separate stages of metal separation are required to achieve optimum removal.
Metal Separation After Primary Shredding
Most metal separation occurs after the primary shredder, with the first stage taking place on the conveyor transporting the shredded wood.
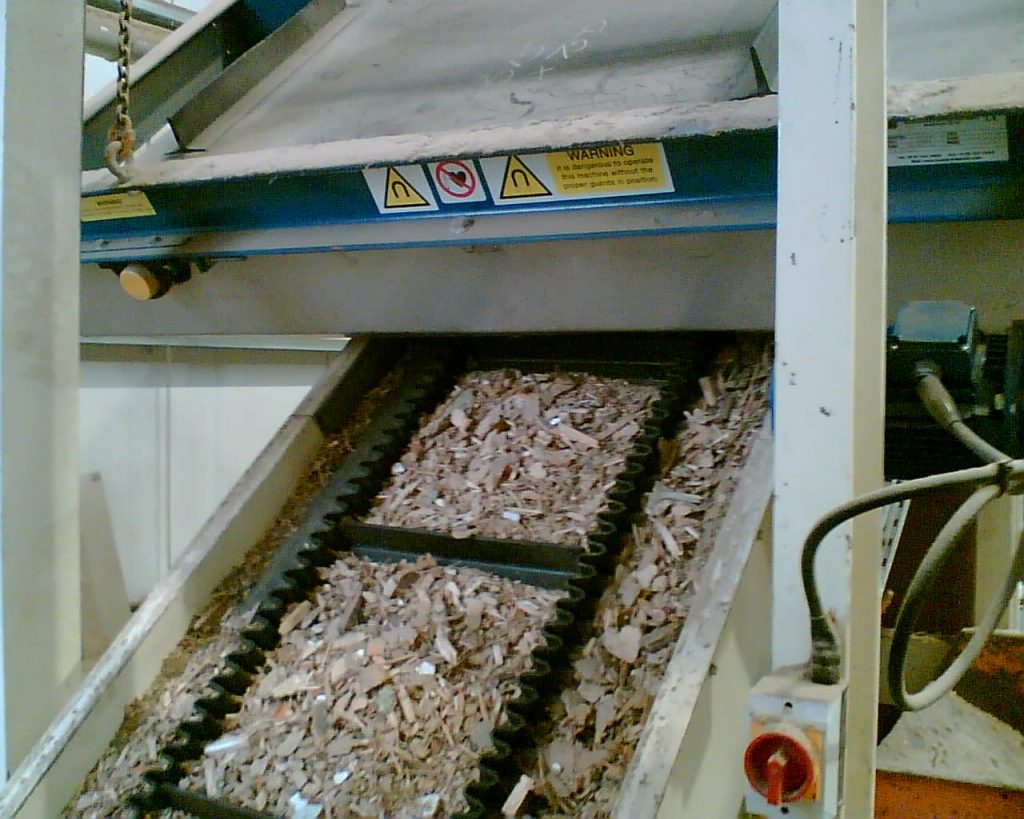
A Permanent or Electro Overband Magnet, suspended over the conveyed wood, lifts and automatically removes liberated ferrous metals such as nails and screws. The Overband Magnet features either a permanent or electro magnetic block mounted between two pulleys, over which runs a slated rubber belt. In operation, the magnetic block attracts ferrous metal up and and onto the rotating rubber belt, which automatically transfers the metal into a separate collection area.
If the nail or screw strikes the belt point first, then there is a risk of the metal piercing the belt and becoming embedded. As the belt revolves, the tips of the nails or screws scrape across the surface of the magnet block, which can cause catastrophic wear.
To prevent such issues, Bunting recommends the use of a tri-polar design of Permanent Overband Magnet. This lifts nails and screws up onto the belt in a flat orientation, preventing belt piercing. Also, all Electro Overband Magnets have 8mm thick ABRO M manganese steel base plates to prevent wear.
Another benefit is the shape of the magnetic field. The tri-polar design focuses the magnetic flux directly below the magnet box, without any of the leakage found in a standard single pole model. This prevents the magnetic holding of captured ferrous metal on the steel frame.
The efficiency of the primary shredder will determine the level of liberation, with wood containing embedded metal separated with the ferrous metal. After hand-sorting, such wood is returned to the primary shredder feed.
In many operations, after the first stage of magnetic separation, reclaimed wood is screened into two different size fractions, with oversized material returning to the primary shredder feed. Tightening the particle size distribution enables fine-tuning of the separation equipment and enhances further metal separation.
- Technical product information: Overband Magnets
Focus On Non-Ferrous Metal Separation
After the Overband Magnet and possible screening, the focus turns to the removal of smaller ferrous metals and non-ferrous metals with a Metal Separation Module, consisting of a high-strength Rare Earth Drum Magnet and Eddy Current Separator. The shredded wood feeds onto a heavy-duty Vibratory Feeder, driven by out-of-balance motors. This spreads and regulates the flow of wood onto the surface of the Drum Magnet.
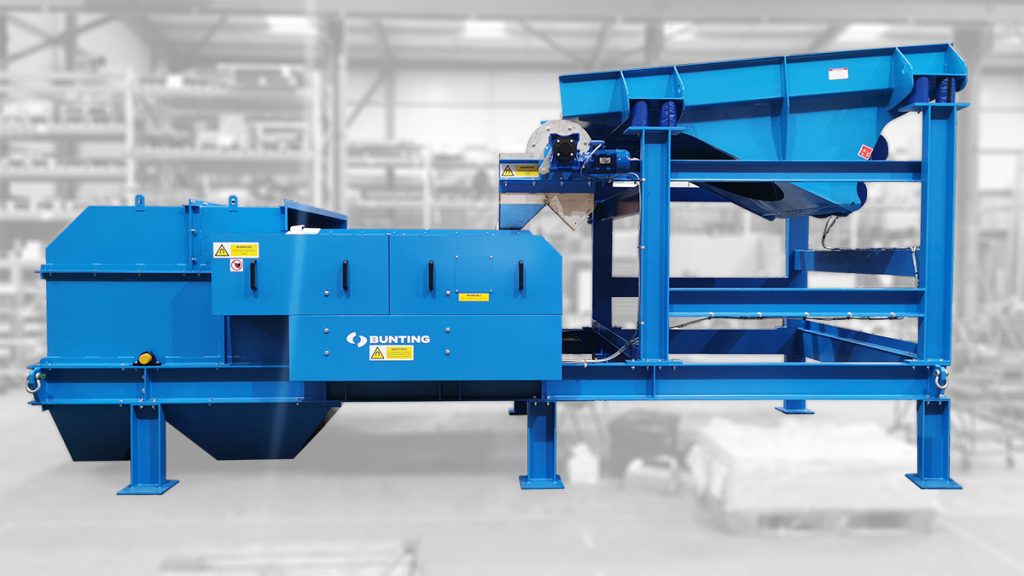
The high-powered magnetic field of the stationary element arc inside the Rare Earth Drum Magnet attracts and separates smaller and entrapped ferrous metal, with the rotating outer shell moving and depositing the captured metal underneath the module in a designated collection area.
As nails, screws and other ferrous metal held onto the outer shell surface of the strong Drum Magnet cause excessive wear, there is a single stainless-steel replaceable skin (up to 8mm thick). This prevents wear to the main Drum shell, which could result in exposure of and damage to the magnet element.
- Technical product information: Permanent Drum Magnets
The remaining wood flows down onto the feed belt of an Eddy Current Separator, which separates non-ferrous metals such as aluminium fixings and handles. The Eddy Current Separator has a high-strength magnetic rotor spinning at high speeds within a non-metallic shell. Non-ferrous metal transported into the alternating magnetic field of the rotor experiences an induced current that produces its own magnetic field. The conflicting north to north and south to south field in the non-ferrous metal particle and the rotor causes the metal to repel. A strategically placed splitter separates the repelled metal from the cleansed wood.
- Technical product information: Eddy Current Separator
In operation, a 2-metre wide Eddy Current Separator achieves excellent levels of non-ferrous metal separation from 50 tonnes per hour of shredded wood (5-20 mm particle size range).
Prior to Secondary Shredding
The second stage of shredding, which further reduces and tightens the particle size range, is susceptible to costly damage from tramp metal. An industrial Metal Detector on the shredder feed conveyor checks the wood for any remaining metal contamination. This could be buried deep inside a piece of wood, which negated separation on previous equipment.
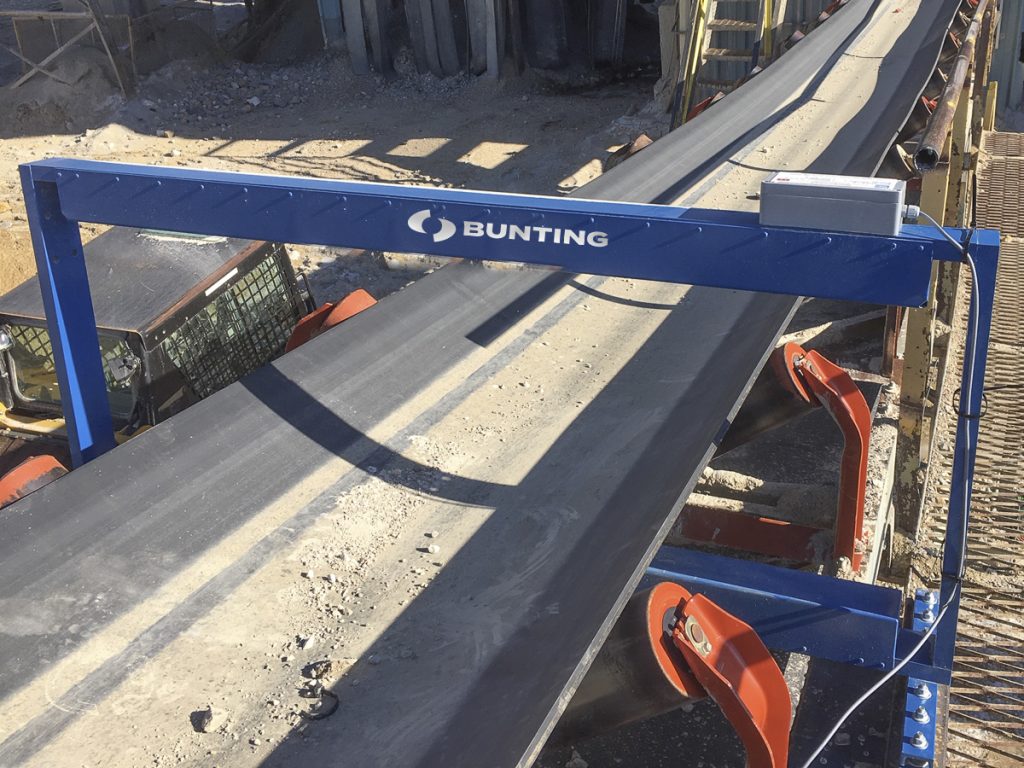
The Metal Detector is mounted around the feed conveyor. Shredded wood passes through the Metal Detector, where any metal contamination alters the magnetic field of the coil. This sends a signal to a control, which either stops the conveyor or initiates a reject flap to remove a section of conveyed wood.
Technical product information: Industrial Metal Detector
Four Stages of Separation & Detection
These four stages of separation and detection ensure that the final shredded wood product is free from both ferrous and non-ferrous metals. As many plants are unique, Bunting’s application engineers commonly visit site to discuss each project and determine the optimum metal separation solution.
Related Articles
For further information on Magnetic Separators, Eddy Current Separators, and ElectroStatic Separators or to discuss a specific project, including arranging a site visit, please contact our technical sales team on:
Email: Gordon Kerr at GKerr@buntingmagnetics.com
Telephone: +44 (0) 1527 65858
Follow us on social media