Rare Earth Roll or Induced Magnetic Roll
By Paul Fears | 07 May 2019
Comparing Two High Intensity Magnetic Separators
High intensity magnetic separators remove ferro and para magnetic particles from dry non-metallic minerals. However, the design of the separation system dictates the final product purity and product losses. The two most common designs of dry high intensity magnetic separator are the Induced Roll (IMR) and the Rare Earth (RE) Roll. These magnetic separators are used widely in the mineral processing industry to purify non-metallic minerals such as silica sand, feldspar, and in the ceramics sector to cleanse spray dried powders and raw materials.
Selecting the optimum separation system is often determined through controlled laboratory tests. Representative samples are tested on laboratory scale versions of the IMR and RE Roll and confirm capacities and separation performance.
Induced Roll Magnetic Separator (IMR)
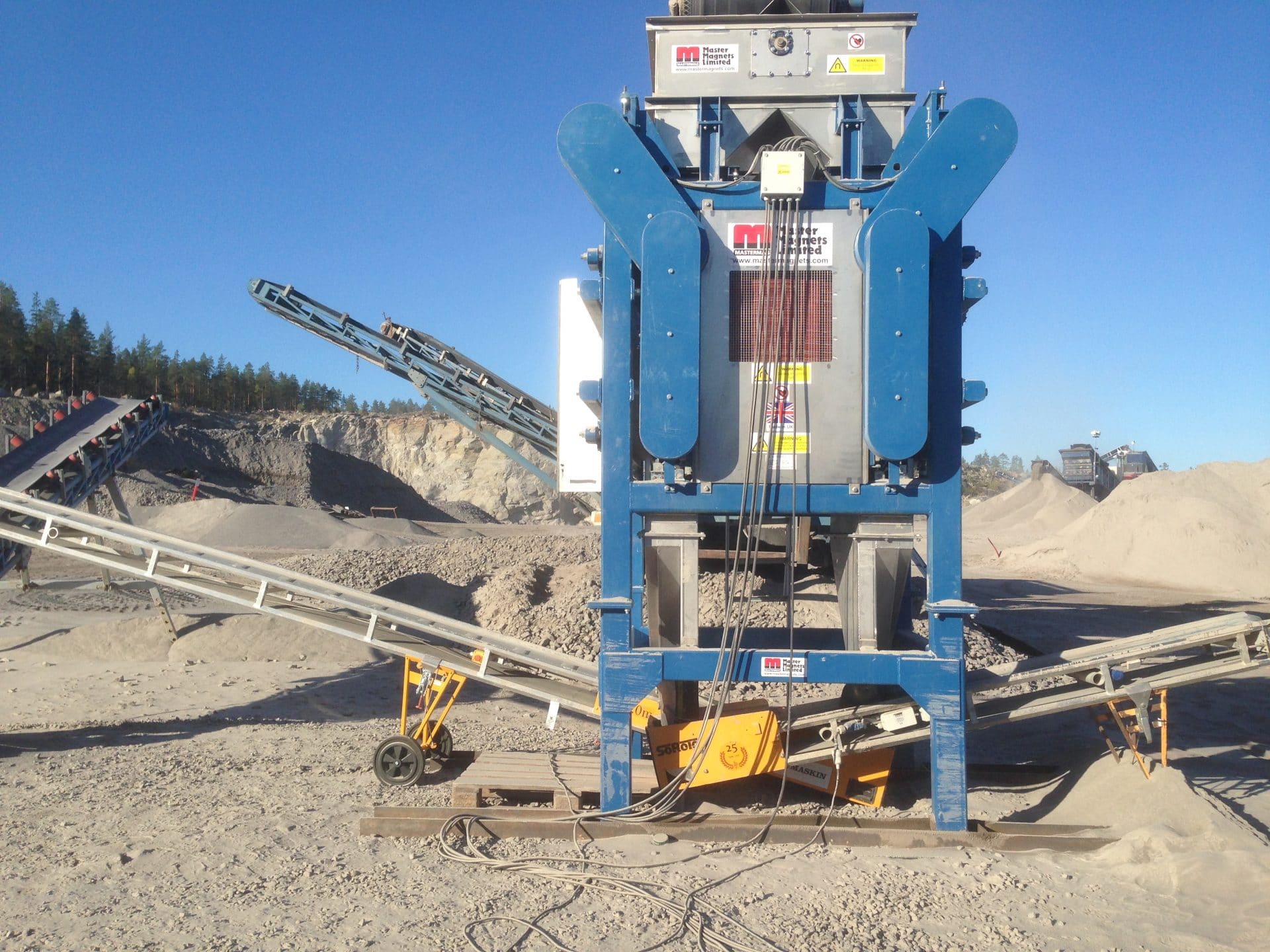
The Induced Roll Magnetic Separator (IMR) uses electromagnetically-generated high intensity magnetic fields to continuously separate small paramagnetic particles from materials with a particle size range between -2mm to 45 microns. The IMR comprises of an electro-magnetically induced steel roll positioned between a bridge bar and pole piece. The peak magnetic field generated on the induced roll is 2.2 Tesla (22,000 Gauss).
In operation, a controlled rate of material is fed from a hopper or vibratory feeder onto the rotating induced magnetic roll (roll speeds vary between 80 to 120 RPM). Weakly magnetic material is attracted and either deflected or held to the roll surface. The trajectory of the non-magnetic material is unhindered, discharging away from the separated material. Captured magnetic material discharges from the roll at a point of lower magnetic intensity, often aided by a brush. A splitter plate is interposed between the two product streams to enable a clean separation. The IMR is often setup to produce a ‘middlings’ stream (i.e. very weak magnetic material mixed with non-magnetics) by the addition of a second splitter plate. It is common practice to have two induced rolls mounted in series on the same unit to enable a double pass for improved separation efficiency and process performance.
The flexibility of the IMR is popular with many mineral processing engineers. The magnetic field strength is variable due to the adjustable electro-magnetic coil and the roll speed is adjustable. In addition, the gap between the induced roll and pole is adjustable to accommodate different feed size ranges.
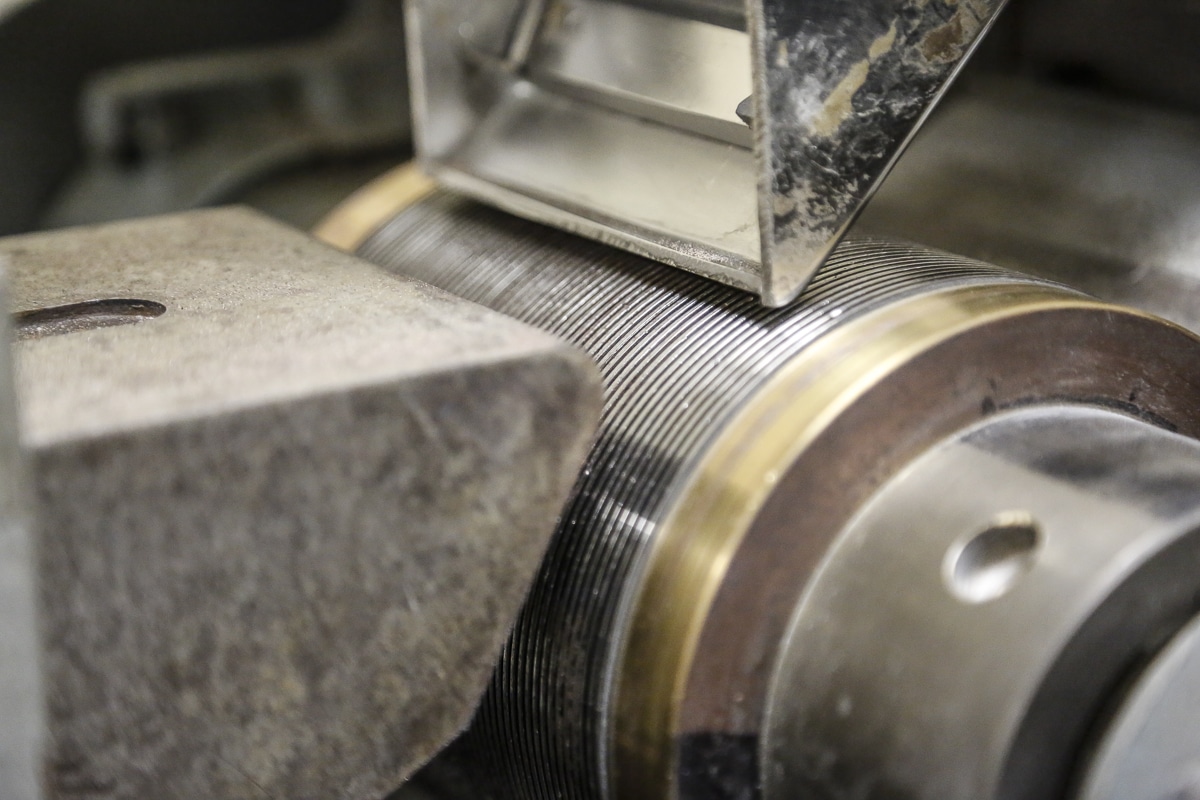
One key advantage of the IMR is the ability to process hot mineral feeds (up to 80-100 C) without compromising the separation efficiency. This is unlike the Rare Earth Roll Separator, which uses permanent magnets. The IMR also tends to generate very little static charge on the surface, resulting in minimal carryover of fine particles into the magnetics fraction. This aids higher grades and improved recoveries.
Typical capacities for a metre-wide unit vary based on mineral type, density and particle size distribution and are ideally determined by laboratory test trials. Typical capacities per meter width are:
- Concentration of ilmenite sands: 4tph
- Chromite concentration: 3-5tph
- Silica sand upgrading: 2-3tph
Rare Earth (RE) Roll Magnetic Separator
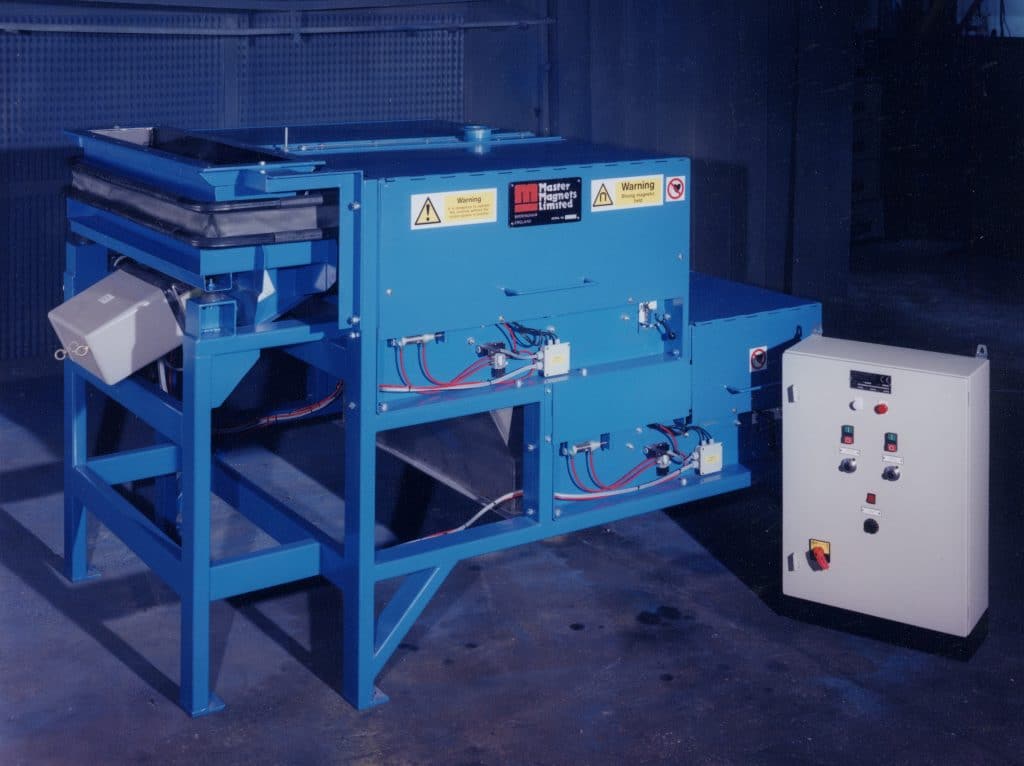
A Rare Earth Roll Magnetic Separator features a high intensity permanent neodymium iron boron magnet head pulley on a short conveyor. The magnets and interspacing steel poles are aligned to produce intense magnetic forces at points across the whole width of the pulley. The system is suited to handle materials with a particle size range between 15mm and 75 microns, although optimum separation is achieved by having a material with a narrow particle size distribution.
In operation, a thin and evenly spread layer of material is fed from a vibratory feeder onto the short centred thin conveyor belt. As the material moves towards and onto the magnetic head roll, magnetically susceptible material is attached to the high intensity magnetic poles. The attracted material is either deflected or held by the magnetic field and falls into a collection chute underneath the head roll. Non-magnetic material is discharged forward of the roll in a normal trajectory. An adjustable splitter divides both fractions.
The magnetic strength of the permanent Rare Earth Roll is adjusted by using different thicknesses of belt. Material trajectories are set by altering the conveyor speed using an inverter control and adjusting the splitter chutes. The spacing between the poles on the magnetic roll are set to suit different particle size ranges.
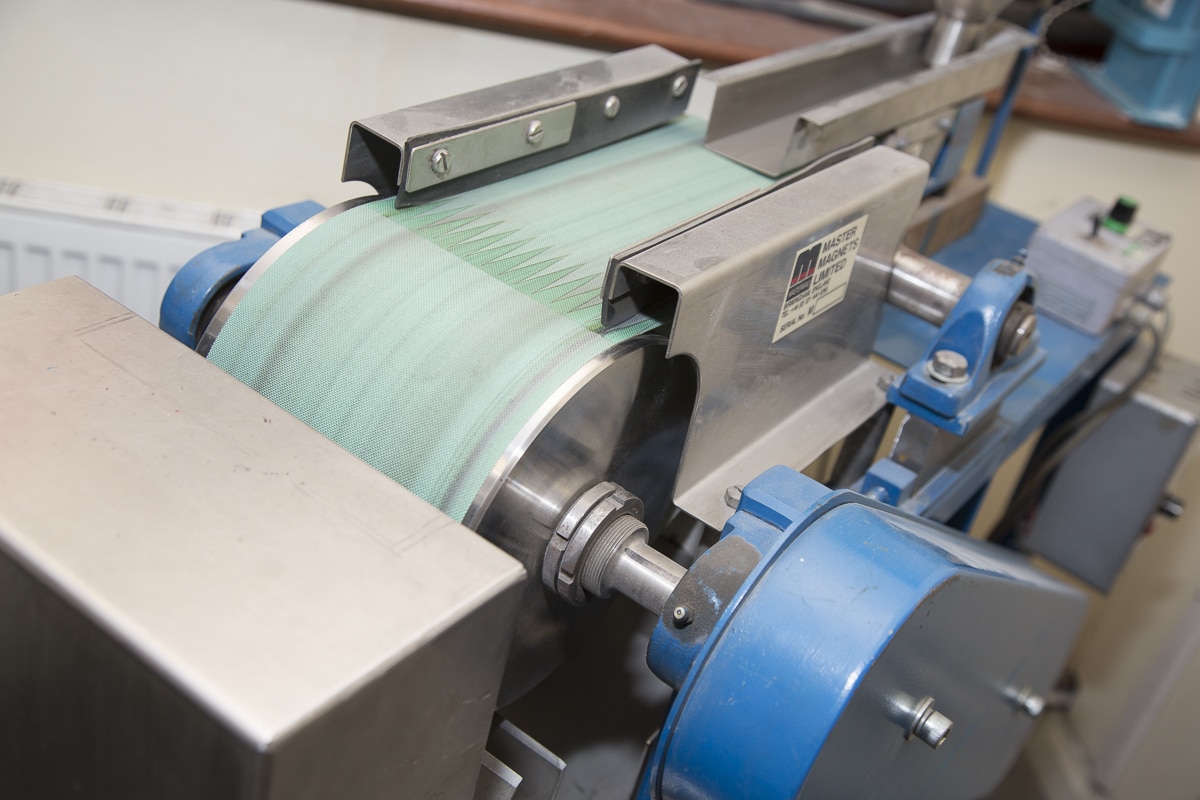
Rare Earth Roll Separators have roll diameters of 75mm, 150mm and 200mm and widths up to 1.5m. Multiple configurations of rolls enable enhanced separation.
Typical Applications include the removal of iron mineral contamination from silica sands, feldspar and other industrial minerals. Processing of granulated slag, ilmenite upgrading, beach sand processing, and recycling applications such as crushed glass. Typical capacities range from 2 and 4 tph depending on the specific application.
Magnetic Separator Selection
Both the Induced Roll Magnetic Separator and Rare Earth Roll Separator produce high intensity magnetic fields to separate ferro and para magnetic minerals. The electromagnetic IMR offers greater magnetic field flexibility and is able to handle high temperature materials. The Rare Earth Roll Separator has a permanent magnetic roll and therefore has a low power consumption. The design is also more compact, reducing the amount of space used in a processing plant.
Ultimately, the separation performance will dictate which magnetic separator is selected for a specific application.
Related Mineral Processing Technical Articles
Magnetic Separators – Mineral Processing Laboratory
Bunting-Redditch has one of the most comprehensive magnetic separation mineral processing testing laboratories in the world. Their Laboratory Technicians have decades of experience in mineral processing. Controlled tests ensure that the most suitable and cost-effective machinery is recommended for each application. The laboratory is equipment with a wide range of equipment including:
- Smaller scaled versions of industrial Magnetic Separators. This equipment is used to accurately scale up to industrial capacities and calculate performance guarantees;
- X-Ray Fluorescence and X-Ray Diffraction analysis are available for chemical assay and mineralogical identification to aid the development of a viable process route for each application;
For further information on our range of magnetic separation equipment designed for purifying ceramics and non-metallic minerals, or to arrange sample tests in our laboratory, please contact us on:
Email: Gordon Kerr at GKerr@buntingmagnetics.com
Telephone: +44 (0) 1527 65858
To keep up to date with our news and technical reports, please follow us on social media