Metal Separator Locations in a Plastics Plant
By Paul Fears | 14 October 2019
Determining the best location to remove metal in a Plastics Processing plant can be difficult. To assist plastics engineers, Bunting has released a Typical Plant Flowsheet showing optimum locations for metal separators. This blog focuses on the locations, designs and types of Magnetic Separator and Metal Detector commonly used in plastics plants.
A Typical Flowsheet
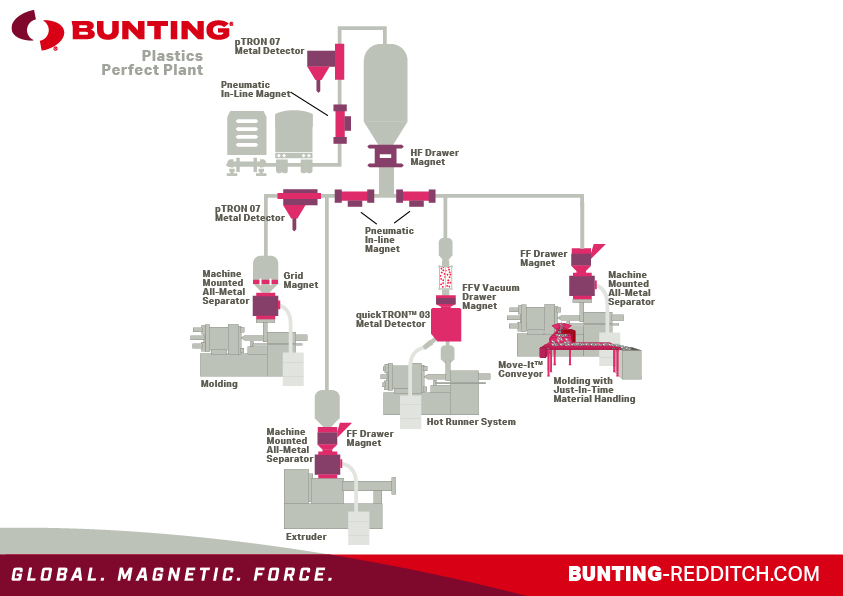
On the flowsheet, the Plastics plant is divided into different areas and identifies optimum locations to remove metal. In many cases, a combination of Magnetic Separator and Metal Detector is recommended as the Magnet captures and holds ferrous metal (the vast majority of metal contamination in any plant). This leaves the Metal Detector to focus on removing the more difficult non-ferrous metals whilst minimising product loss and production downtime.
The Equipment
The type and suggested location of Metal Separation equipment is as follows:
Stage 1 – Primary Feed to Storage
Tramp metal commonly enters the process with the raw material feed. Subsequently, it is good practice to position metal detectors and magnetic separators on the pneumatic line feeding the primary storage silo. This reduces the level of tramp metal introduced to the process from external sources.
- Pneumatic Inline Magnet (PIM) for ferrous metal removal;
- pTRON 07 Metal Detectors for all metal removal
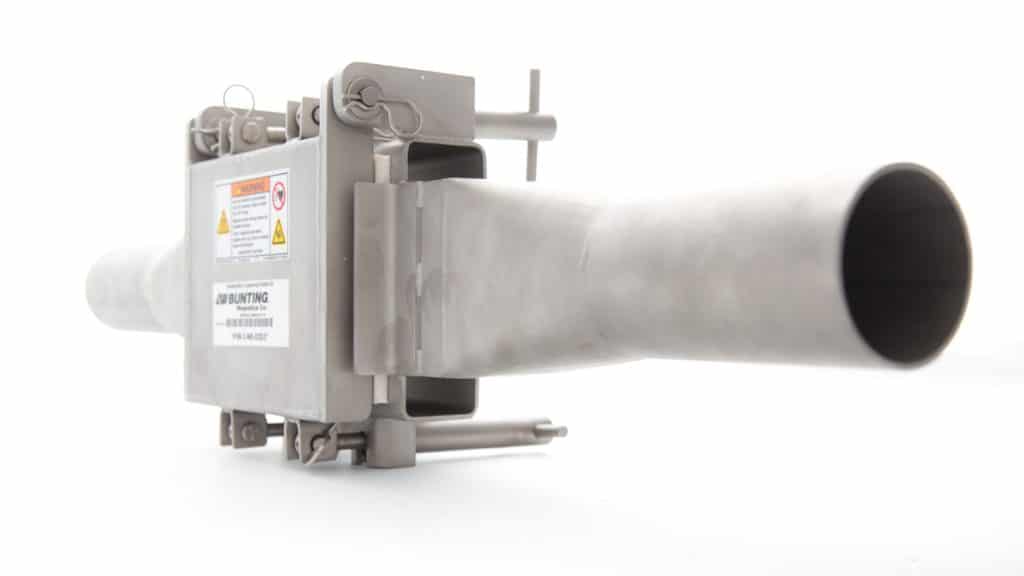
Stage 2 – Exiting Bulk Storage Silo
The key in preventing equipment damage or causing defects in the end plastic product is to continually identify and trap any metal contamination. Metal contamination arises within a plant from fatigued equipment (e.g. screens, pumps), general wear and tear (e.g. of silos, pipes, etc), and accidental introduction from personnel when conducting maintenance and other work. Subsequently, several stages of metal removal are required.
When the raw material leaves the storage silo, the feed passes through a gravity fed HF Drawer Filter or Pneumatic Inline Magnets.
- Drawer Filter Magnet for ferrous metal removal;
- Pneumatic Inline Magnet (PIM) for ferrous metal removal;
Stage 3 & 4 – Moulding Line and Moulding (with just-in-time material handling)
Metal contamination entering the moulding lines causes costly damage to machinery affecting productivity, as well as increasing the percentage of finished product rejects. A combination of metal detectors and magnetic separators prevents such issues, with the final combination determined by the installation. The options include:
- pTRON 07 Metal Detector for detection and removal of a range of metal contaminants from pneumatic lines;
- A simple Grate Magnet mounted in the hopper of the moulding machine to remove ferrous metal;
- A FF Drawer Filter Magnet for ferrous metal removal;
- Machine Mounted All-Metal Separator to remove all metals;
Stage 4 – Extruder
Metal contamination also damages the extruder. Once again, a combination of a magnetic separator and metal detector provide important protection.
- FF Drawer Filter Magnet to remove ferrous metal;
- Machine Mounted All-Metal Separator to remove all metals;
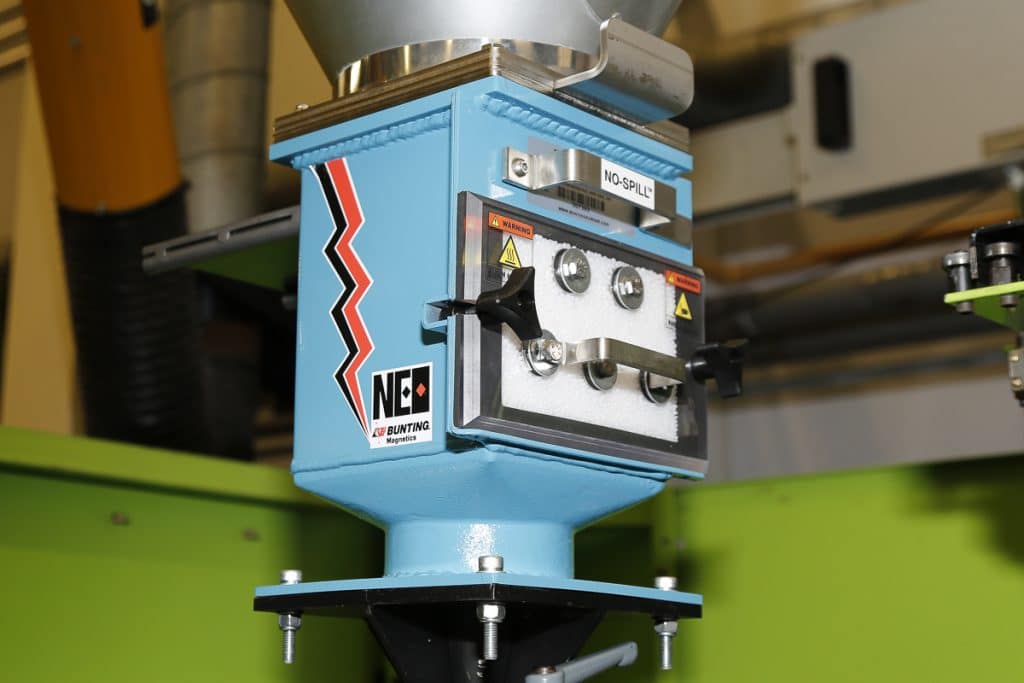
Stage 5 – Hot Runner System
Metal contamination entering the hot runner system, which is an assembly of heated components used in plastic injection molds that inject molten plastic into the cavities of the mold, can cause catastrophic and costly damage. If the system is fed pneumatically, the optimum metal separation equipment includes:
- FV Vacuum Drawer Magnet to remove ferrous metal;
- quickTRON 03 Metal Detector to remove all metal;
Stage 6 – Reworking and Recycling Rejects & Offcuts
Within any plastic manufacturing process, a proportion of the production will be rejected (i.e. by metal detectors) and there will be off-cuts and pre-production runs that produce recoverable waste. Metal contamination in this ‘waste’ is more likely, due to the collection process and also as some materials will have already been rejected with such contamination.
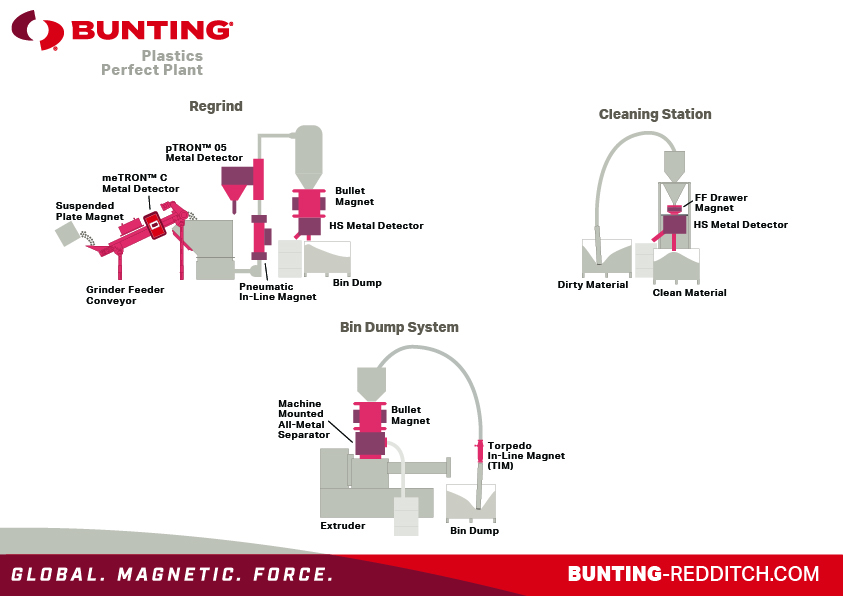
The three recycling processes include:
Regrind
The process stands for Post Industrial Regrind, or PIR and essentially describes the process of recapturing scrap plastics and resins from any manufacturing process. These processes happen, for example, when lids are being made for bottles and plastic containers. There is a wide range of metal detectors and magnetic separators used including:;
- Suspended Plate Magnet – positioned over the feed conveyor to lift and remove larger ferrous metal;
- meTRON 05C Metal Detector mounted on the conveyor to identify any non-ferrous metal;
- Pneumatic Inline Magnet – positioned on the pneumatic line feeding the storage silo to remove smaller ferrous metal fragments;
- pTRON 05 Metal Detector – follows the Inline Magnet detecting smaller non-ferrous metals;
- Plate Housing Magnet – this design of magnetic separator has two Plate Magnets facing each other across an open gap and is ideal for handling materials that tend to bridge when there are flow restrictions;
- HS Metal Detector – final check to remove any remaining rogue metal;
Cleaning Stations
Previously rejected material is reprocessed to recover any entrapped good material, initially passing through a magnetic separator followed by a metal detector.
- FF Drawer Filter Magnet
- HS Metal Detector;
Bin Dump System
In some operations, the waste plastic is immediately extruded for future use in the plant or on-sale. Metal separation equipment is vital to protect the extruder and can include:
- Torpedo Inline Magnet;
- Plate Housing Magnet;
- Machine mounted All-Metal Separator;
Cost Saving Protection
The type and design of Magnetic Separator and Metal Detector and the recommended locations has been determined following several decades of working with plastics producers and processors all over the world. There are always variations to plant designs and layouts that mean different types of Metal Separation equipment is needed and an onsite review by a Bunting engineer will help ascertain the best solution.
Other relevant plastic industry articles
For further information on removing metal from a plastics processing plant using Magnetic Separators and Metal Detectors, please contact the Bunting technical sales team on:
For additional information on removing metal from plastic please contact us on:
Email Gordon: gkerr@buntingmagnetics.com
Telephone: +44 (0) 1527 65858
All product photographs by Paul Fears Photography
Follow us on social media