Keeping Ceramic Sanitaryware Iron Free
By Paul Fears | 09 July 2019
Sanitaryware is a commonly used term in the ceramics industry referring to sanitary appliances found in toilets and bathrooms. Traditionally, bathroom bowls, cisterns, bidets, urinals and washbasins are made from porcelain (a ceramic material made from clay that might be described as ‘vitreous china’ when coated with enamel). This might be referred to as ceramic, porcelain or china sanitaryware, and is commonly white.
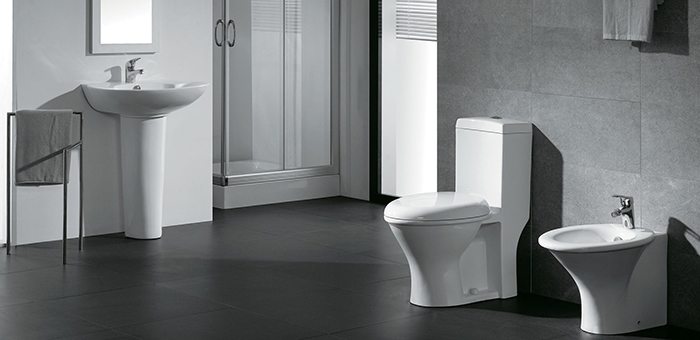
In the modern day, many sanitaryware products are white or have a very pale colouring. This results in any defects being easily visible, with the affected product being rejected prior to release from the manufacturing plant. This is costly and time-consuming, with rejected materials being re-crushed and fed back into the process or discarded to waste.
One of the most common causes of a defect is iron, either as free iron or as an iron-bearing mineral. After firing, iron contamination occurs as ugly and very visible black spots on the surface of the sanitaryware, or creates a weakness within the ceramic structure. Such contamination can also affect the colour of the glaze, reducing the whiteness.
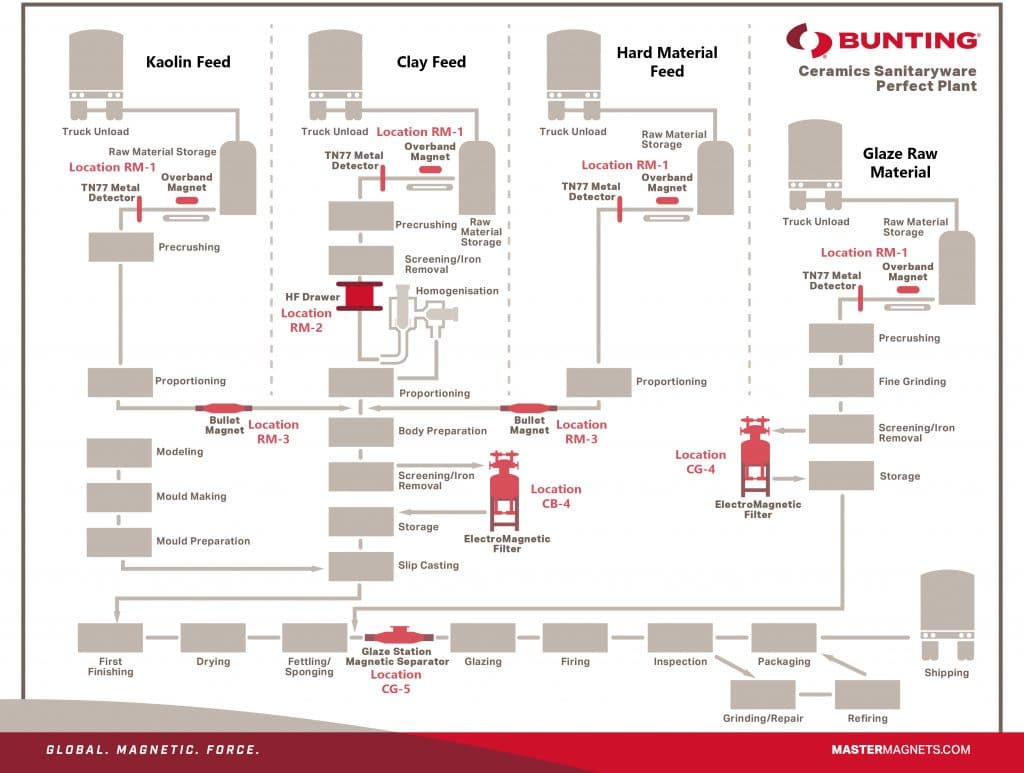
Iron and Mineral-Iron Removal
There are several key stages within a sanitaryware manufacturing process including:
- Body preparation;
- Glaze preparation;
- Moulding and Mould preparation;
- Casting;
- Drying;
- Control and Spraying;
- Firing;
- Sorting;
- Refire/Rework;
Within this process, there are key areas to locate and position magnetic separators for the optimum separation of iron, mineral iron, and magnetic minerals.
Ceramic Body Preparation
The ‘Ceramic Body’ is the material mix used to form the core structure of the sanitaryware item. Ceramic Body is produced by mixing raw materials including Ball Clay, Kaolin, Silica, and Feldspar. Iron and mineral iron contamination in ceramic body ultimately causes weaknesses within the finished fired sanitaryware, often lead to cracking and fracture.
Removing Tramp Iron from the Raw Materials – RM-1
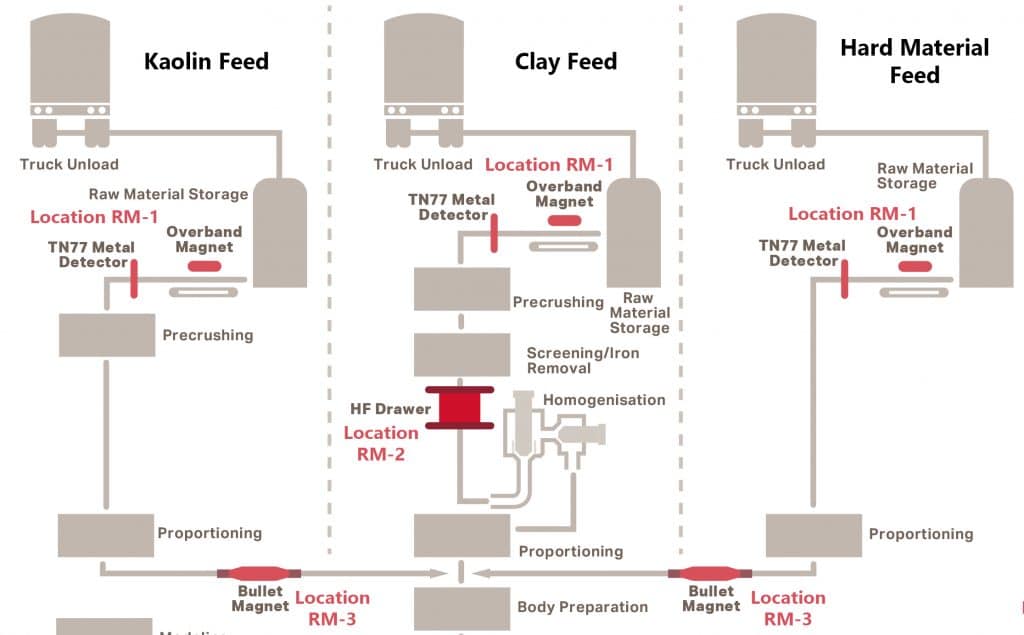
In most cases, raw material suppliers have already removed a large proportion, if not most of, the larger free iron and stronger iron bearing minerals. However, tramp metal is often accidently introduced during transportation and handling. If tramp metal enters the pre-crushing stage or Ball Mill it can cause significant and costly damage to processing equipment. Also, such tramp iron would be significantly reduced in size causing it to spread extensively through the body mix and becoming increasingly difficult to extract.
The raw material is delivered and stored before being batch fed into the process. A combination of a Magnetic Separator and Metal Detector (RM-1) on the conveyor feeding the raw material to the pre-crushing stage ensures the removal and detection of larger tramp metal, both iron and non-magnetic. A permanent Overband Magnet (or Suspended Plate Magnet), positioned over the feed conveyor initially lifts and separates tramp iron. This is followed by a TN77 Metal Detector that identifies and enables the removal of non-magnetic metals such as manganese steel.
- Technical Product Information: Overband Magnets
- Technical Product Information: TN77 Metal Detector
Prior to the kaolin, clay and hard materials being mixed together as the Ceramic Body, it is important to ensure the removal of the vast majority of free fine iron and strongly magnetic minerals, many of which have been liberated during the pre-crushing stage.
On the Clay feed line, post pre-crushing and screening, fine iron and magnetic minerals released during crushing are separated using a Drawer Filter Magnet (with high-strength Neodymium Tube Magnets) (RM-2).
- Technical Product Information: HF Drawer Filter Magnet
After pre-crushing and proportioning of the kaolin and the hard materials, locating a Bullet Magnet prior to mixing ensures the capture of any liberated fine iron and strongly magnetic minerals.
- Technical Product Information: Bullet Magnets
Separating Fine Magnetic Particles from Ceramic Body
The mixed and milled raw materials then form the ‘Ceramic Body’. After mixing, the ceramic body is screened and then passes through a final stage of magnetic separation. This is the last opportunity to capture problematic magnetic particles; a task ideally suited for a high-intensity Electro Magnetic Filter (CB-4).
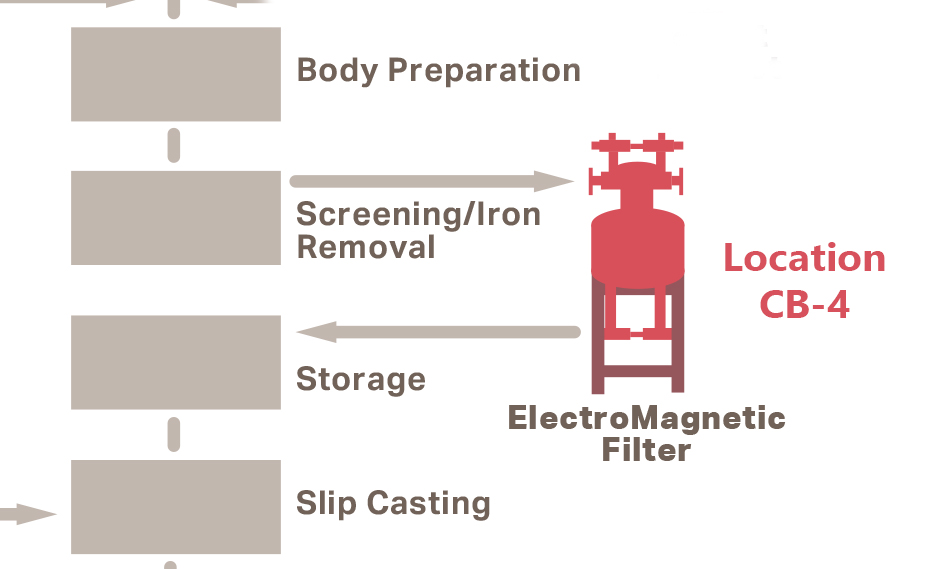
An Electro Magnetic Filter has a magnetic stainless steel matrix positioned in the centre of an electromagnetic coil. The magnetic field is intensified on the points of the matrix to approximately 10-12,000 gauss. The ceramic body is pumped up through the Electro Magnetic Filter, where very fine iron and weakly magnetic minerals are captured on the points of the matrix.
On a timed cycle (dependent on the level of contamination), the Electro Magnetic Filter goes through an automatic cleaning sequence to remove the capture magnetic particles.
- Technical Product Information: Electro Magnetic Filter
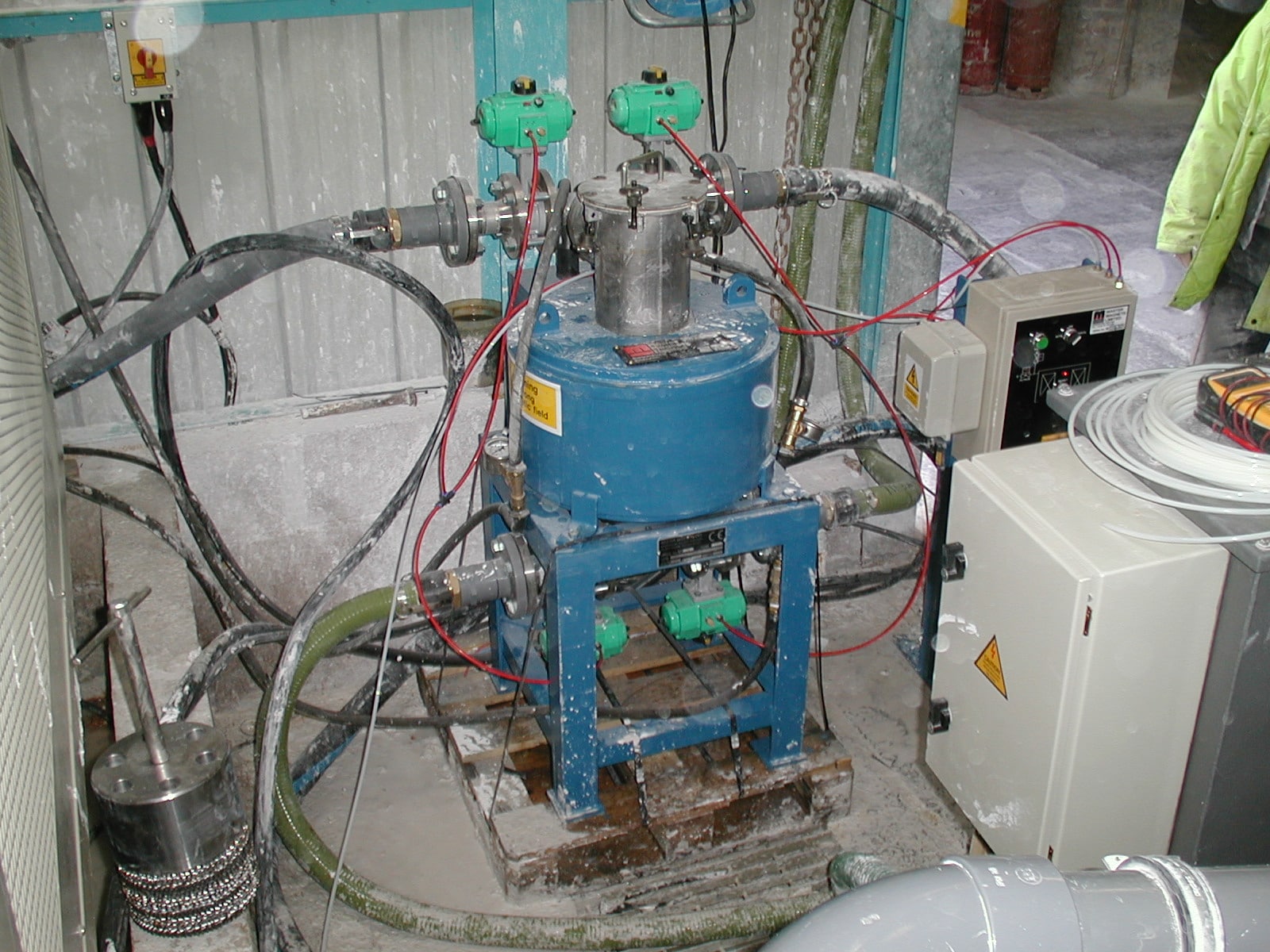
The cleaned Ceramic Body is then stored prior to slip casting.
Ceramic Glaze Preparation and Application
Ceramic glaze is an impervious layer or coating of a vitreous substance, which has been fused to a ceramic body through firing. Through history, it has been used to cover and disguise iron-induced and other defects.
Glaze is produced by mixing zircon, feldspar, quartz, calcite, china clay and zinc oxide. The raw material mix is ground in a ball mill.
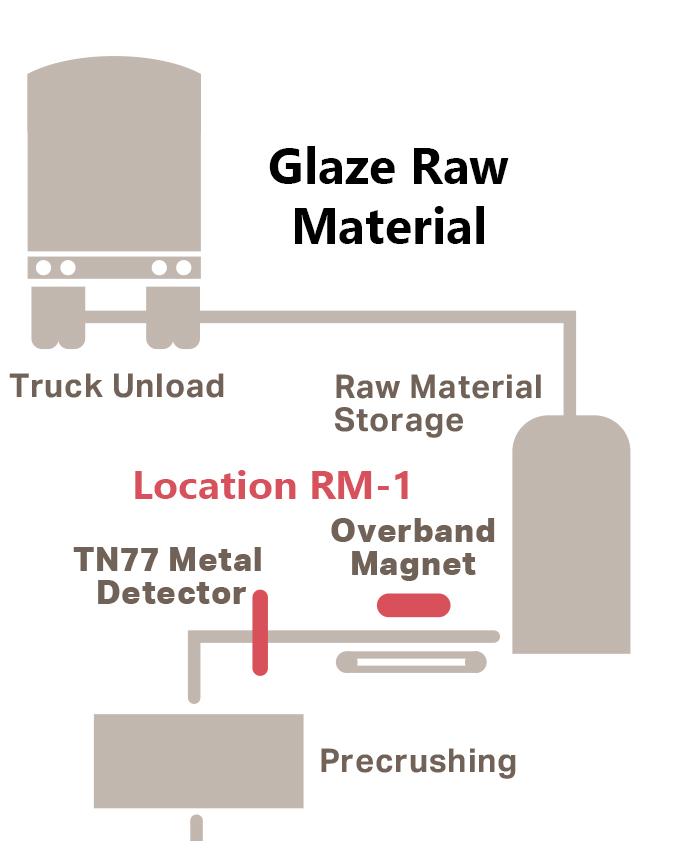
Ensuring the Glaze is iron-free is more critical than with the Body. Any iron present in the Glaze will be visible on the surface of the sanitaryware product. As with Ceramic Body, the first stage of separation focuses on the raw material feed. Ensuring the raw materials entering the process are free of tramp metal reduces the risk of heavy contamination.
Once again, the combination of a permanent Overband Magnet and TN77 Metal Detector (RM-1) provides optimum protection and separation prior to pre-crushing.
The Ceramic Glaze raw material mix is first pre-crushed and then finely ground before being screening. After screening, the Glaze is fed through a high-intensity Electro Magnetic Filter. Arguably, this is the most important magnetic separation stage in the whole sanitaryware plant, removing both fine iron and weakly magnetic minerals from the Glaze.
The cleansed Ceramic Glaze is then stored and transported to the glazing stations when needed. Immediately prior to the glaze spraying, the material passes through a final Neodymium Magnetic Separator such as a Liquid Pipeline Magnet or Magnetic Trap (CG-5). This captures any magnetic particles that have entered the Glaze during storage or transportation to the glazing line.
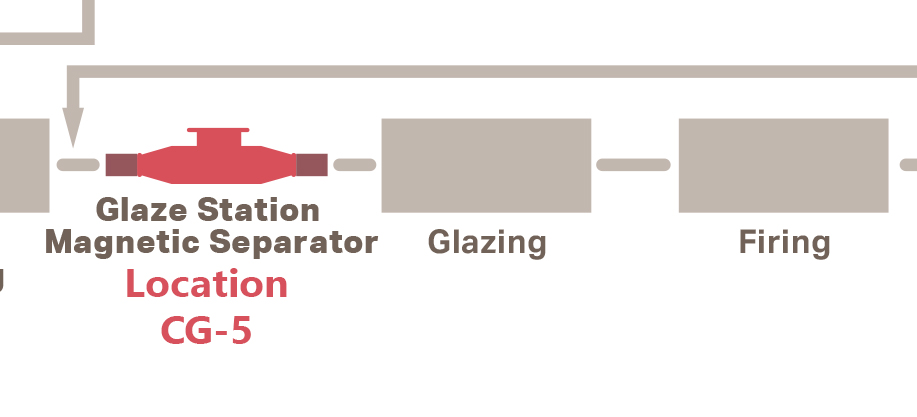
- Technical Product Information: Liquid Pipeline Magnets
The glazed sanitaryware is then fed into a kiln for firing, before passing through inspection to search for defects such as cracks or spots (from iron or other materials). Rejected products will either go for reworking or be crushed and blended back into the raw material feed.
Crushed rejects are passed over a high-intensity permanent Drum Magnet or Rare Earth Roll Magnetic Separator to remove iron and ensure that contaminated product is not reintroduced to the process.
Related Technical Articles
Optimum Magnetic Separation Reduces Rejects
Understanding the ceramic manufacturing process is important when making recommendations for the optimum magnetic separation equipment. The magnetic separators mentioned in this review are used successfully in ceramic production operations. However, each manufacturing process is unique and a visit by a local Bunting Sales Engineer will help understand a specific process and iron contamination issue and propose a specific solution.
For additional information on eradicating iron contamination blemishes in ceramic tableware, tiles, or sanitaryware, please contact us on:
Email: Gordon Kerr at GKerr@buntingmagnetics.com
Telephone: +44 (0) 1527 65858
Follow us on social media