Metal Separation from Plastic Flake
By Paul Fears | 26 July 2023
A UK plastic recycler has installed a Bunting Metal Separation Module to separate ferrous and non-ferrous metal from plastic flake. The Metal Separation Module features Vibratory Feeders, a Drum Magnet, and an Eddy Current Separator.
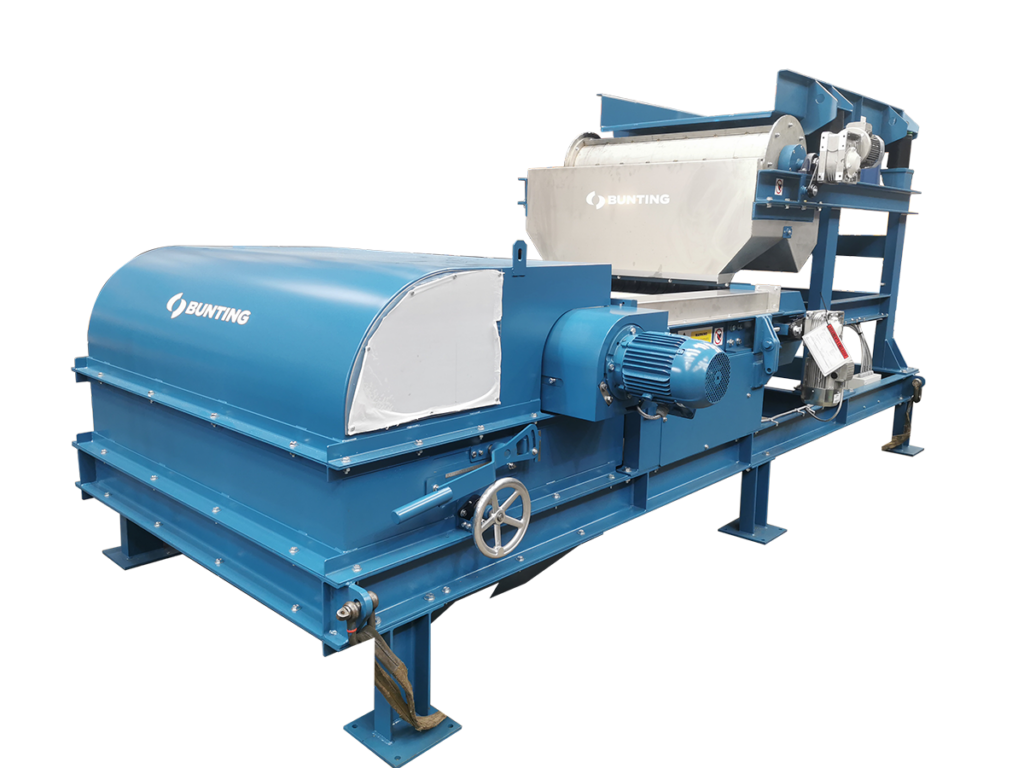
The successful recycling of plastic waste is often hindered by the presence of contamination, including ferrous and non-ferrous metals. In this project, the UK plastic recyclers approached Bunting to address the issue of metal contamination in <20mm plastic flake.
Material Tests
Initially, the recycler undertook extensive material tests at Bunting’s Customer Experience Centre in Redditch, UK. These tests identified the best model of Eddy Current Separator for the project and confirmed the operating parameters, including the throughput per metre width.
The Metal Separation Module acquired for the project included a high-strength Rare Earth Drum Magnet followed by an eccentric-rotor Eddy Current Separator.
In operation, a Vibratory Feeder presents a controlled and regulated flow of plastic flake feeds onto the Drum Magnet. The Drum Magnet has a stationary, permanent Rare Earth magnet element mounted inside a rotating stainless-steel shell. Plastic flake flows onto the rotating shell, with ferrous metal and magnetic materials being held to the surface and deposited underneath out of the material flow. The high-strength magnetic element enables the separation of both large and small magnetic particles.
Removing Non-Ferrous Metals
The plastic flake then flows onto the belt of an Eddy Current Separator and is conveyed into the head-pulley separation zone. The Eddy Current Separator (ECS) utilises magnetic forces to repel non-ferrous metals physically and enables separation from non-conductive materials. The Eddy Current Separator is a dual pulley conveyor system where the non-metallic rotor cover houses an independently rotating high-speed magnetic rotor. Separation occurs when a non-ferrous metal particle (e.g. aluminium, copper or zinc) is conveyed into the magnetic zone. The non-ferrous metal particle is exposed to rapidly changing magnetic polarity. This induces ‘eddy currents’ into the particle generating an electrical current (Fleming’s left-hand rule) that subsequently creates its own magnetic field. The two magnetic fields oppose each other (i.e. North vs North pole repulsion), causing the repulsion of the non-ferrous metal particle and a change in trajectory. The measured positioning of a splitter enables the separation of non-ferrous metals from non-metallic material due to the altered and unaltered material trajectories.
The material tests at Bunting’s Customer Experience Centre had determined that the eccentric-rotor design gave the best non-ferrous metal separation. In the eccentric rotor, Eddy Current Separator, the smaller-diameter rotor is mounted off-centre inside a non-metallic shell.
To meet the two tph capacity demands of the recycler, the feed widths of both the Drum Magnet and Eddy Current Separator are 1250mm. All the equipment is mounted on one common frame with a single control panel.
Related Recycling Articles
- HML Recycling Operate Bunting Magnetic Separators
- Parry & Evans Recover Metal with Bunting Magnetic Separators
For further information on Magnetic Separators, Eddy Current Separators, and ElectroStatic Separators for metal separation in recycling applications or to discuss a specific project, including undertaking tests in our Customer Experience Centre, please contact our technical sales team on:
Email: Michael Allen (mallen@buntingmagnetics.com)
Telephone: +44 (0) 1527 65858
Follow us on social media