Metal Recovery from WEEE and Cable
By Paul Fears | 25 January 2021
There is a wealth of valuable metals present in WEEE (Waste of Electrical and Electronic Equipment) and cables. However, the recovery is often difficult due to the small particle size range and variable nature of the metals.
With the development and launch of the ElectroStatic Separator [in 2020], Bunting now provides a complete multi-stage metal separation solution incorporating several different separation techniques to maximise metal recovery from complex waste streams. This blog reviews a typical WEEE flowsheet and the optimum location and design of the associated separation equipment.
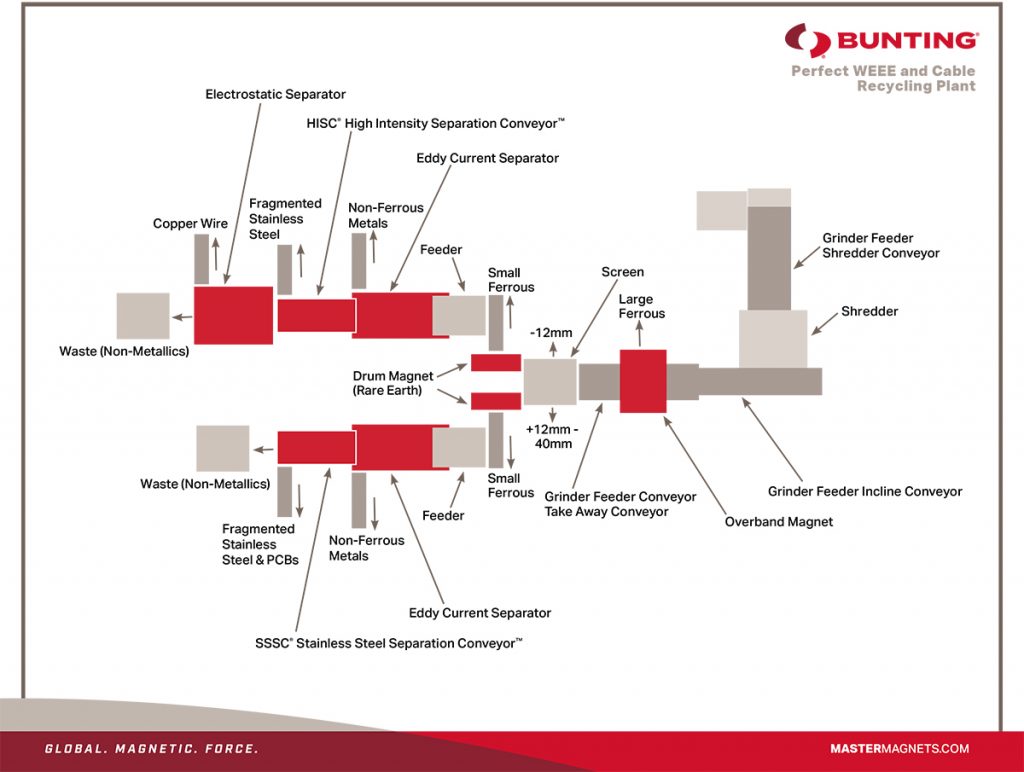
Metal Liberation
Successful metal liberation is critical to maximise recovery. This flowsheet shows one primary stage of shredding, although a secondary stage is common prior to screening.
Even with two-stages of shredding, a self-cleaning Overband Magnet is commonly located on the exit conveyor from the primary shredder to recover larger ferrous metals. Removal at this stage also reduces the load and wear on the secondary shredder.
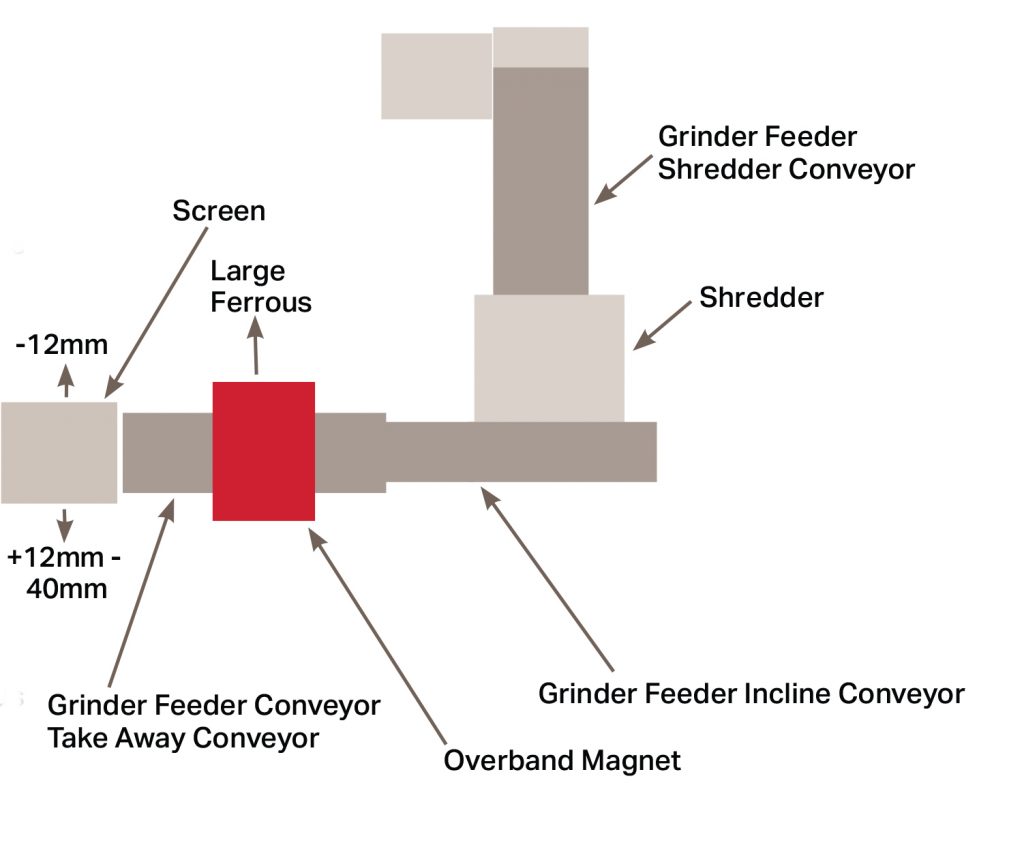
The self-cleaning Overband Magnet has a slated rubber discharge belt revolving around two outer pulleys, and an internal permanent or electro magnetic block. The magnetic block attracts and lifts ferrous metal from the conveyor, which is then automatically transferred into a collection area by the discharge belt. Both permanent and electro Overband Magnets successfully recover ferrous metal, with models such as the ElectroMax providing an enhanced separation at higher suspension heights.
- Technical Product Information: Overband Magnet
Controlling Particle Size
Optimum metal separation requires careful particle size control. Such tight control enables both higher metal recoveries and purities. Following successful metal liberation, the material on this flowsheet is screened into three fractions:
- < 12mm
- 12mm – 40mm
- >40mm (returned to the primary or secondary shredder)
<12mm Fraction
Efficiently recovering metals from the <12mm fraction is challenging and requires a multi-stage separation process.
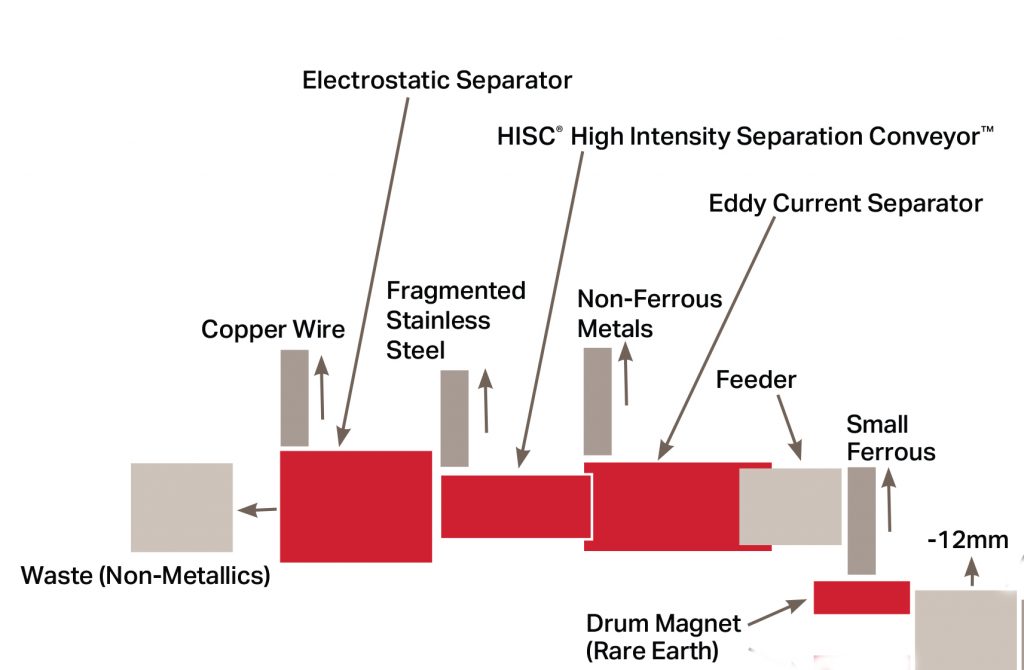
Ferrous Metal Separation
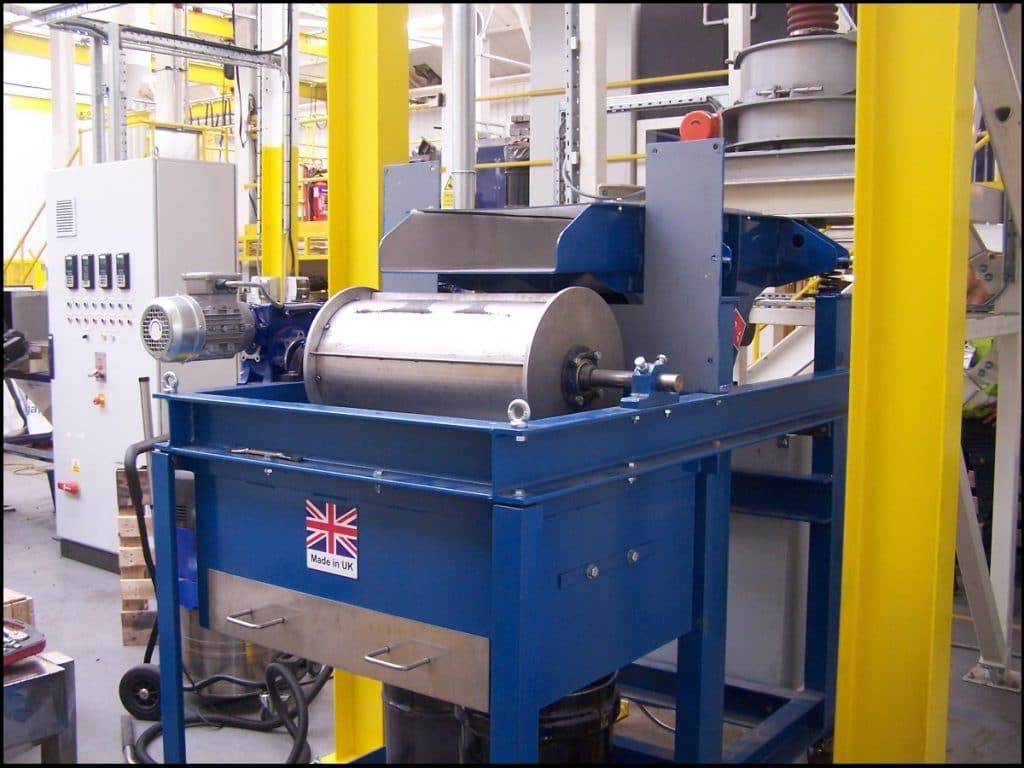
After screening, the <12mm fraction is fed, via a vibratory feeder, over a high-strength Rare Earth Neodymium Permanent Drum Magnet, usually featuring a radial field for maximum ferrous metal separation. The vibratory feeder enables close-control of the feed onto to the surface of the Drum Magnet, with a mono-layer gently falling from a short distance (avoiding bounce) onto the Drum’s rotating stainless-steel shell. Magnetic particles attract to the radial magnetic poles before being transferred underneath and out of the magnetic field where they fall into a separate collection area or conveyor. Non-magnetic and very weak magnetic particles flow under a normal trajectory onto the next separation stage.
- Technical Product Information: Permanent Drum Magnet
Non-Ferrous Metal Recovery
The metal and non-metallic mix, free of strongly magnetic materials, then feeds via another vibratory feeder onto the belt of an Eddy Current Separator.
An Eddy Current Separator features a high-speed rotating magnetic rotor, mounted inside a slower moving non-metallic head pulley of a short conveyor. The rotating alternating polarity magnetic rotor generates currents and opposing magnetic fields in non-ferrous metal particles causing them to repel. This results in the non-ferrous conducting metals, such as aluminum and copper, moving in a different trajectory to the unaffected non-metallic materials; enabling segregation using a carefully placed splitter. In operation, a mix of non-magnetic material is fed, via a vibratory feeder, onto a belt. The belt transfers the material into the separation zone of the head pulley with the magnetic rotor.
There are two designs of Eddy Current Separator based on mounting of the high-speed magnetic rotor inside the non-metallic head pulley.:
- Concentric, where the magnetic rotor is concentrically located within the outer non-metallic shell;
- Eccentric, where the magnetic rotor is mounted eccentrically in one quadrant of the outer non-metallic shell;
Optimum separation and recovery of non-ferrous metals below 12mm is achieved using the model High-Intensity Eccentric (HIE).
- Technical Product Information: Eddy Current Separators
Stainless-Steel Separation
The volume of <12mm material decreases significantly after the removal of strong magnetics and larger sized non-ferrous metals. This mix is ideal for recovering fragmented stainless-steel, which becomes weakly magnetic when processed through a shredder.
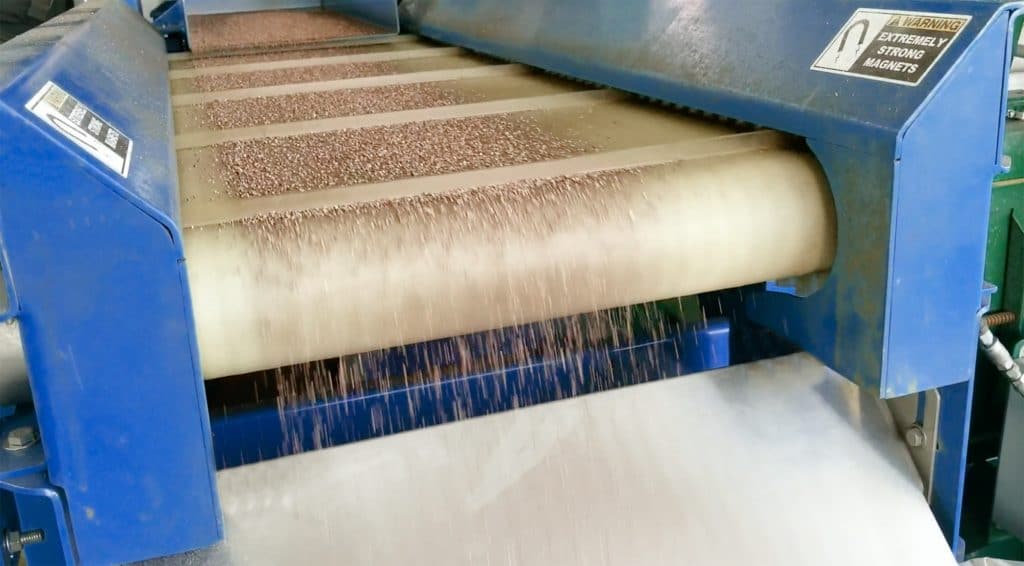
The High-Intensity Separation Conveyor (HISC) recovers stainless-steel from smaller sized materials such as this <12mm fraction. In operation, the ultra high-intensity neodymium head roll attracts and separates the fragmented stainless-steel and any other small magnetic materials remaining in the fraction, leaving behind a mix of fine non-ferrous metal and non-metallic waste.
- Technical Product Information: Stainless Steel Separators (HISC and SSSC)
Recovering Fine Copper Wire
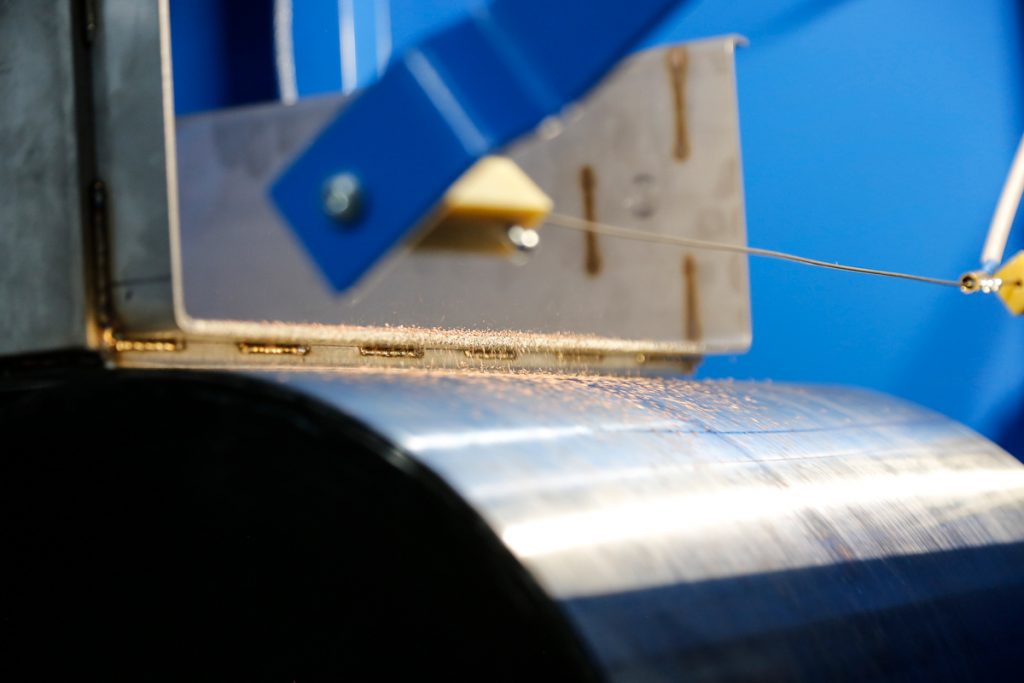
The final separation stage on the <12mm fraction focuses on recovering fine copper wire; metals that are below the operational range of the Eddy Current Separators (nominally <2mm). For optimum separation, the remaining material mix could be screened at around 3mm to concentrate the fine copper.
The revolutionary electrostatic separator provides the only known method of separating and recovering metals from certain recycled materials. Separation occurs by inducing an electrostatic charge into a conductive dry-liberated particle.
In operation, an electrostatic separator exploits the difference in electrical conductivity between various materials in a feed material to produce a separation. The ability to produce a separation depends on a number of key material characteristics including:
- Conductivity;
- Moisture content;
- Particle size range;
When processing <12mm shredded WEEE or cable, the electrostatic separator may be the only technology able to execute the separation of fine copper wire and other small non-ferrous metals. The copper wire fraction could be over 98% pure copper, depending on the composition of the feed.
- Technical Product Information: ElectroStatic Separator
12-40mm Fraction
Metal recovery from the larger fraction is not as demanding as for <12mm and requires three (3) instead of four (4) stages of separation.
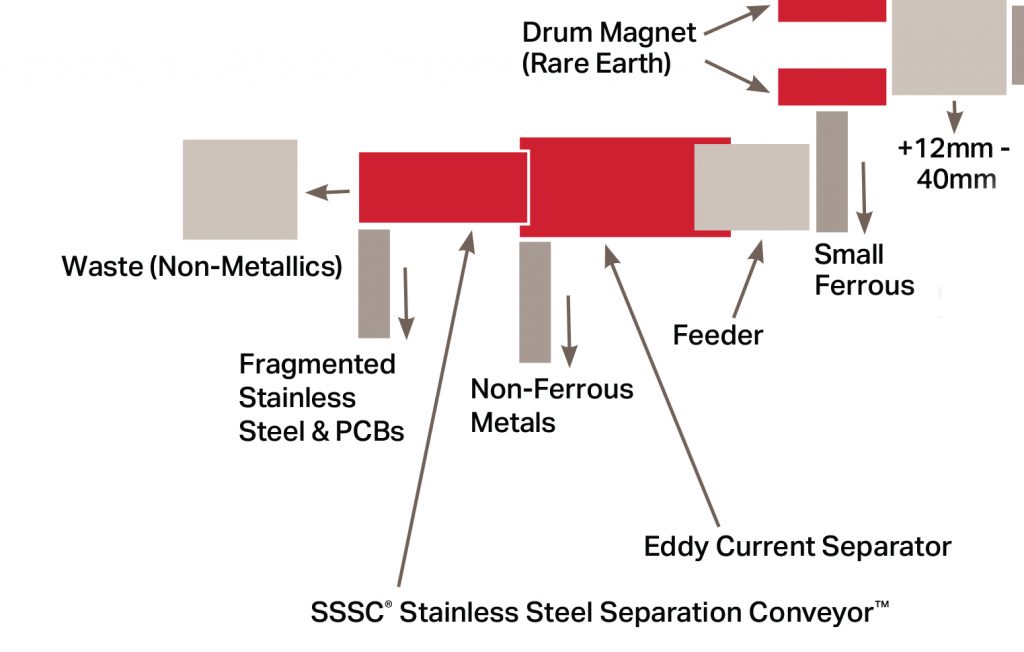
Recovering Ferrous Metals
As on the <12mm line, the first stage is recovering smaller ferrous metals with a high-intensity Rare Earth Neodymium Permanent Drum Magnet fed by a vibratory feeder. Once again, a radial magnetic field produces the highest degree of metal recovery.
- Technical Product Information: Permanent Drum Magnet
Separating Non-Ferrous Metals
For the 12-40mm fraction, the High-Intensity Concentric (HIC) Eddy Current Separator model provides optimum non-ferrous metal separation and recovery. Once again, a vibratory feeder provides a regulated, controlled and mono-layer flow of material onto the feed belt. Non-ferrous metals are propelled away from the high-speed magnetic rotor and into a separate collection area.
- Technical Product Information: Eddy Current Separators
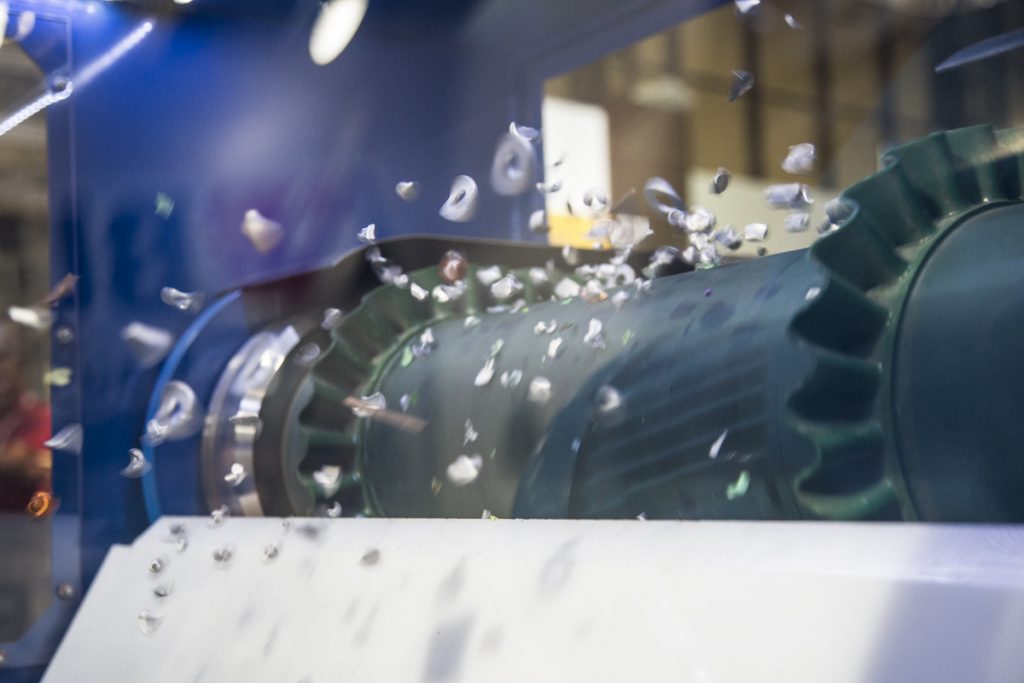
Weakly Magnetic Stainless-Steel and PCB Separation
The final stage of separation for the 12-40mm fraction takes place on the Stainless-Steel Separation Conveyor (SSSC). In contrast to the HISC, the SSSC has a large diameter ultra high-intensity neodymium magnetic roll for the recovery of larger-sized weakly magnetic particles. Experience on working installations shows that the SSSC also recovers shredded green PCB boards, which are then either manually picked or separated by reprocessing over the SSSC.
- Technical Product Information: Stainless Steel Separators
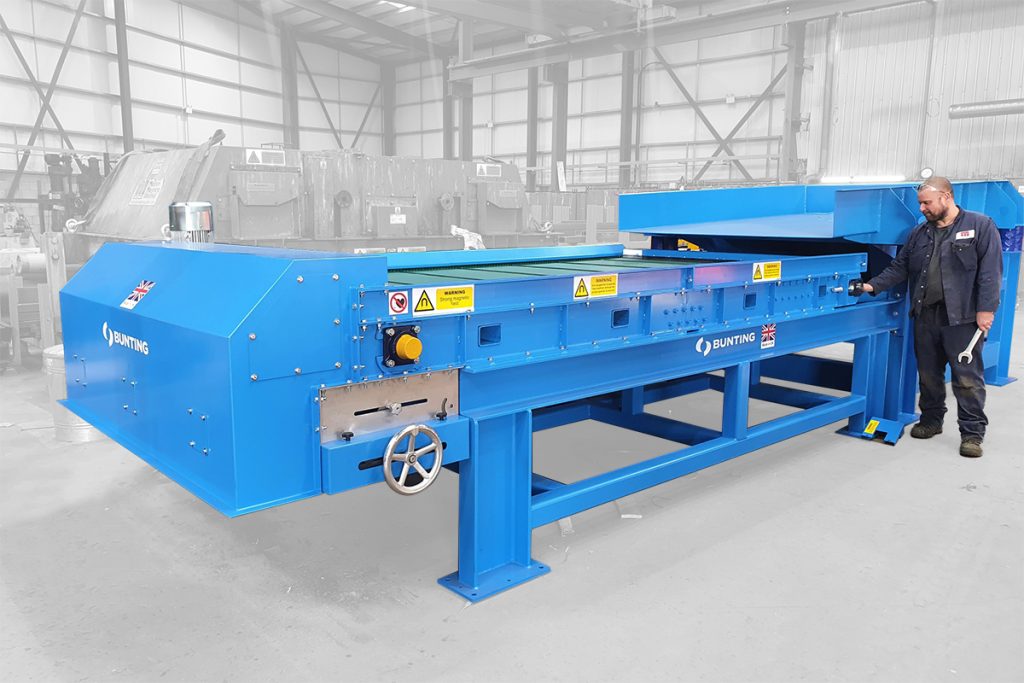
Optimising Metal Recovery
Understanding the material and the unique processes of each WEEE and cable processor ultimately determines the optimum metal recovery equipment. Nevertheless, this ‘typical’ process highlights proven methods for producing seven (7) different saleable fractions:
- Strong magnetics
- <12mm
- 12-40mm
- Non-ferrous metals
- <12mm
- 12-40mm
- Stainless-steel and weak magnetics
- <12mm
- 12-40mm
- Fine non-ferrous metals such as copper wire (nominally <2mm)
At the Bunting-Redditch Customer Experience Centre just outside Birmingham (UK), our applications engineers undertake controlled tests on laboratory-scale metal separators. Such tests determine recovery rates and purity levels, whilst identifying whether further changes are needed in the process to maximise metal recovery (e.g. additional size reduction, improved screening, etc).
Related Recycling Articles
For further information on Magnetic Separators, Eddy Current Separators, and ElectroStatic Separators for metal recovery in recycling applications or to discuss a specific project including undertaking tests in our Customer Experience Centre, please contact our technical sales team on:
Email: Gordon Kerr at GKerr@buntingmagnetics.com
Telephone: +44 (0) 1527 65858
Follow us on social media