Maximising Non-Ferrous Metal Separation
By Paul Fears | 03 December 2019
There is an ever-growing demand to maximise the recovery or removal of metal from waste, especially non-ferrous. The economic viability of many recycling plants is based upon their ability to successfully recover valuable metals such as aluminium. In operations processing waste plastics, successful recycling is not possible without removing the ferrous and non-ferrous metal contamination. This demand is driving the evolution of the Eddy Current Separator.
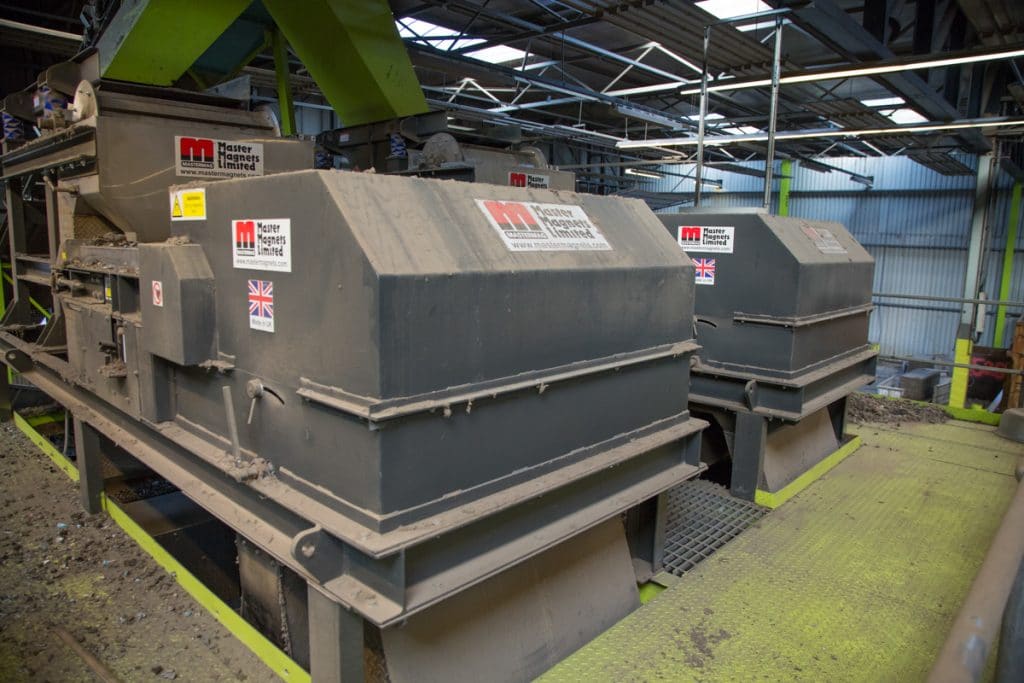
An Eddy Current Separator is a two-pulley conveyor system with a high-speed, multi-pole magnetic rotor positioned inside a non-metallic head pulley. In accordance with Fleming’s left-hand rule, an electric current is induced into any non-ferrous metal particle entering the alternating magnetic field. This current generates its own magnetic field within the non-ferrous particle that reacts with the magnetic rotor, causing it to be repelled and enabling separation.
First Bunting Eddy Current Separator
The first Bunting Eddy Current Separator dates back to the early 1990s. Over thirty years, Bunting’s Eddy Current technology has evolved, with both concentric and eccentric rotor designs featuring differing numbers of magnetic poles.
The optimum separation is achieved by balancing a number of factors including, but not limited to:
- the particle size of the non-ferrous particle;
- the magnetic field depth of the magnetic rotor;
- the number of magnetic poles on the magnetic rotor;
- the rotation speed of the magnetic rotor.;
Generally, for the separation of larger particles (e.g. aluminium cans) a deeper magnetic field with fewer magnetic poles is required, whereas separating smaller particles requires a shallower field, with more poles operating at a higher rotation speed.
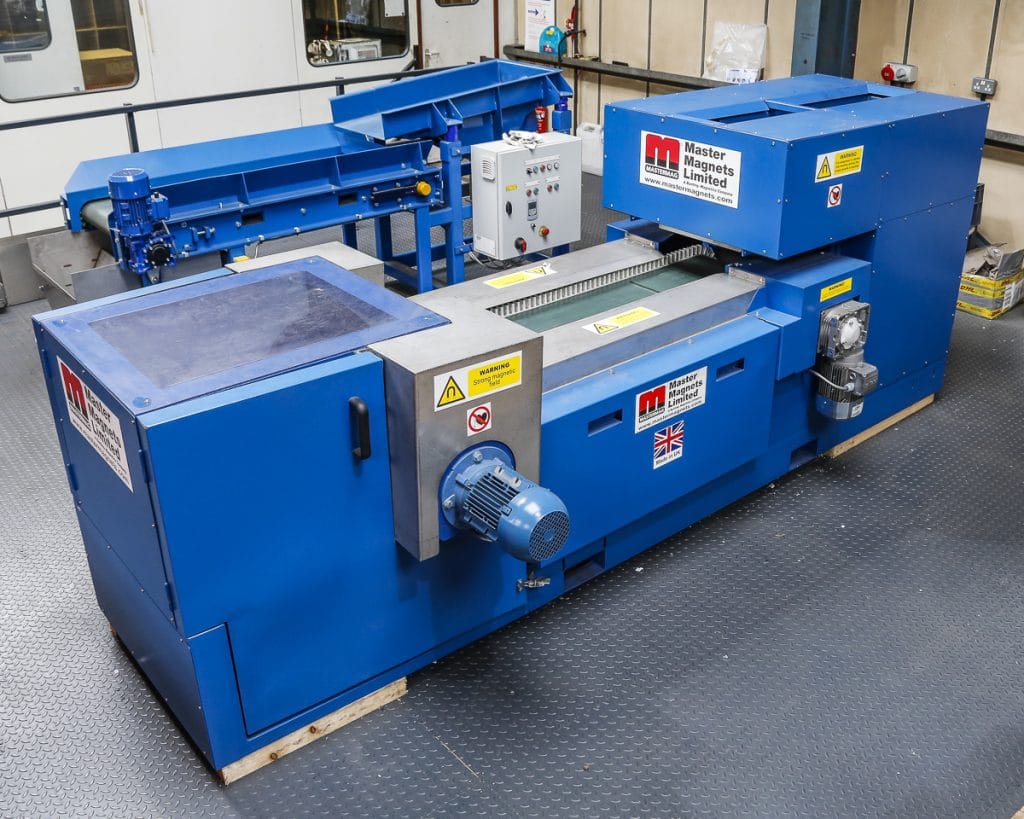
However, waste and secondary materials are commonly not uniform in shape or size. Subsequently, it is important to take a more holistic view of the separation objective before proposing a specific design of Eddy Current Separator. This includes appreciating the operation of a recycling plant and ultimate objectives such as end-product purity, metal content and recovery. Controlled tests at one of Bunting’s test facilities confirm what level of separation is possible and the projected operating parameters once installed.
The Eddy Current Separator is a key technology in the global war against waste, which Bunting’s engineers continue to develop and enhance.
For additional information on equipment used to separate and recover metals, please contact us on:
Email: press@buntingeurope.com
Telephone: +44 (0) 1527 65858
Photographs taken by Paul Fears Photography
Follow us on social media