Metal Recovery from Finnish Household Waste
By Paul Fears | 07 March 2017
In January 2016, Bunting secured the contract for the supply of metal separation equipment for a waste treatment facility processing municipal solid waste (MSW) and solid recovered fuel (SRF) in Lahti, 105km northeast of Helsinki. This new plant, designed and built by Vimelco, would be handling an input in excess of 66,000 TPA of this mixed waste and Bunting was to provide a solution for the recovery of an estimated 2700 TPA of ferrous and non-ferrous metals in the material.
Metal Recovery from 20-200mm Fraction
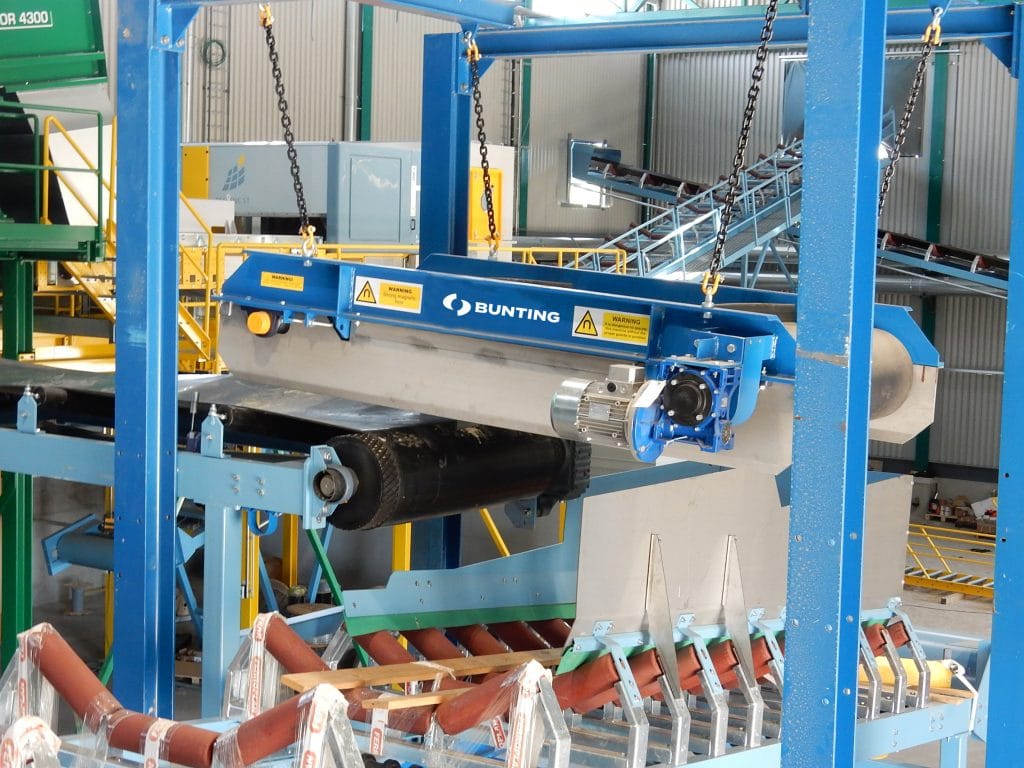
The incoming material was sized into two different fractions; a 3D and 2D fraction with a size range from 20mm to 200mm. Vimelco required an Overband Magnet installed inline over the head of the conveyors for the recovery of ferrous metals. A Permanent In Line Overband Magnet (12PIL7) was selected for the 3D fraction, working at a 300mm suspension height across the 1000mm wide feed belt.
- Technical Product Details: Overband Magnets
After recovery of ferrous metals, the material fed onto a 1000mm wide Eddy Current Separator for recovery of non-ferrous metals (e.g. aluminium cans).
Metal Recovery from <20mm Fraction
The finer 2D fraction required another Overband Magnet, which was suspended at 250mm above the conveyor, for the recovery of smaller ferrous metals. To maximise small and fine ferrous metal removal, a Rare Earth Magnetic Head Pulley (400mm dia x 1000mm wide) replaced the conveyor head pulley.
Technical Product Details: Magnetic Head Pulleys
The <20mm ferrous metal-free waste passed over a 1250mm wide Eddy Current Separator (ECS) to recover smaller non-ferrous metallics.
Both Eddy Current Separators include controls to vary the belt and magnetic rotor speeds to fine tune the metals separation.
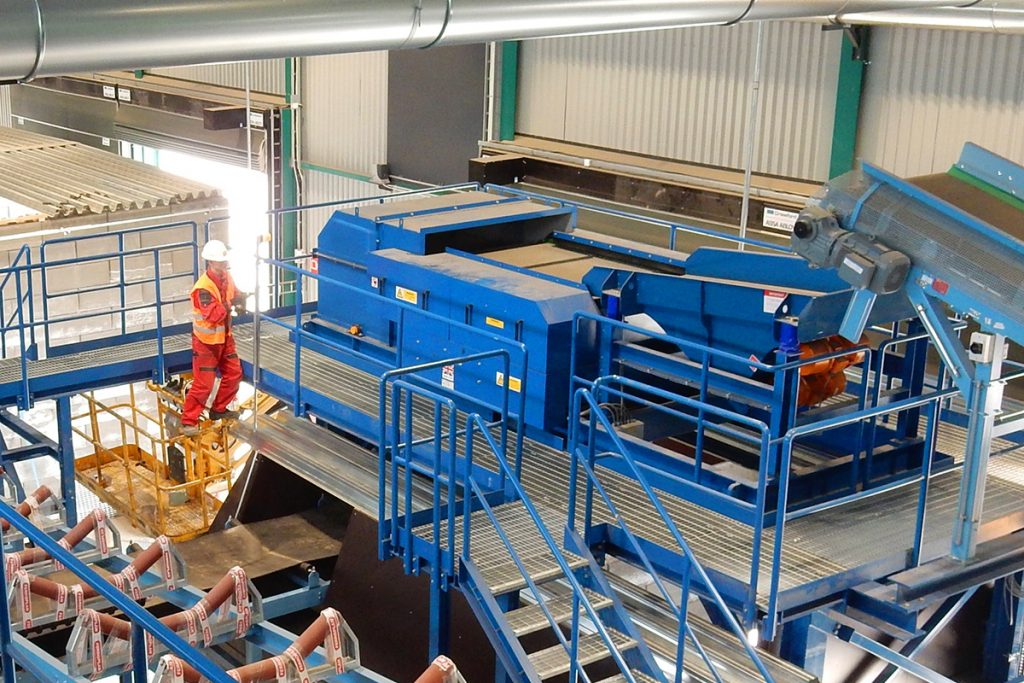
The metal-free waste feeds onto windshifters and optical sorters for further segragation.
- Technical Product Details: Eddy Current Separators
Manufacturing Expertise
The design and manufacture of the Overband Magnets, Eddy Current Separators and Pulley Magnets took three months, with delivery occurring in April 2016. Vimelco oversaw the installation of the metal separators, resulting in cold and hot commissioning throughout July and August. Although Vimelco engineers were fully versed in the setting up and operation of the machinery, Bunting personnel provided specialist technical assistance and information.
Related Recycling Articles
For further information on Magnetic Separators, Eddy Current Separators, and ElectroStatic Separators for metal recovery in recycling applications or to discuss a specific project including undertaking tests in our Customer Experience Centre, please contact our technical sales team on:
Email: Gordon Kerr at GKerr@buntingmagnetics.com
Telephone: +44 (0) 1527 65858
Follow us on social media