Magnetic Separation in Mining and Mineral Processing
By Paul Fears | 17 February 2025
Magnetic separators are commonplace in most mining and mineral processing operations. However, the term ‘magnetic separator’ encompasses a diverse range of specialist separation equipment with the ability to separate widely different materials such as large tramp metal and paramagnetic minerals.
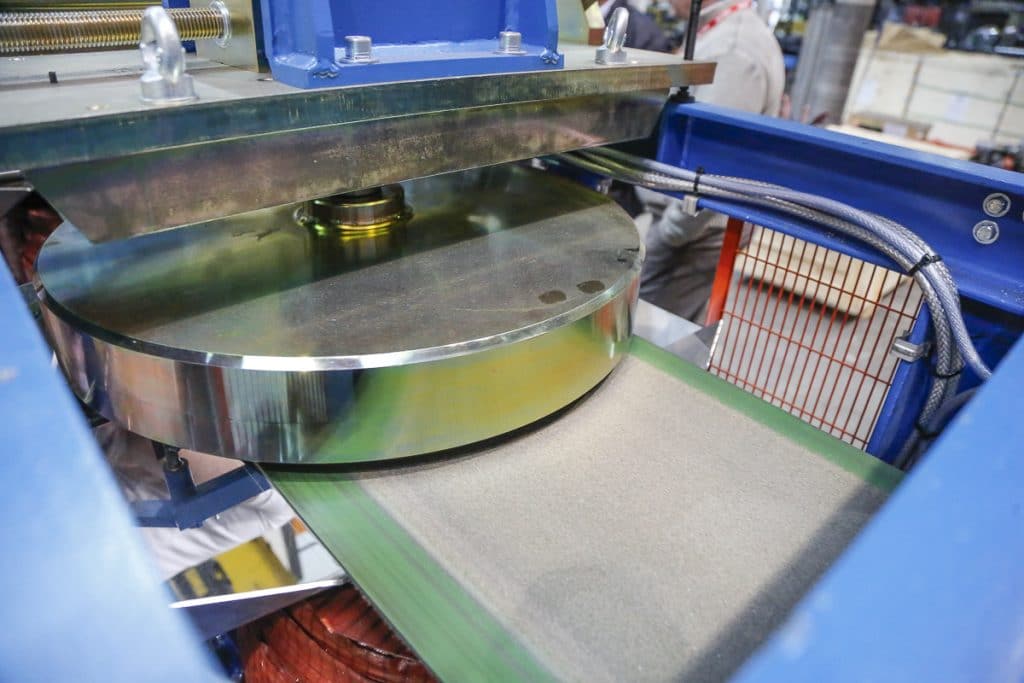
Magnetic separators for the mining and mineral processing sectors are broadly differentiated into two ranges. Commonly early in the process, magnetic separators with a deep magnetic field, such as Overband Magnets, remove tramp ferrous metal to prevent damage to crushers, screens, and conveyors. For mineral beneficiation, also known as ore dressing, high-intensity magnetic separators with a shallow and powerful magnetic field separate strong to weakly magnetic minerals from mined ores and quarried rocks for purification or recovery.
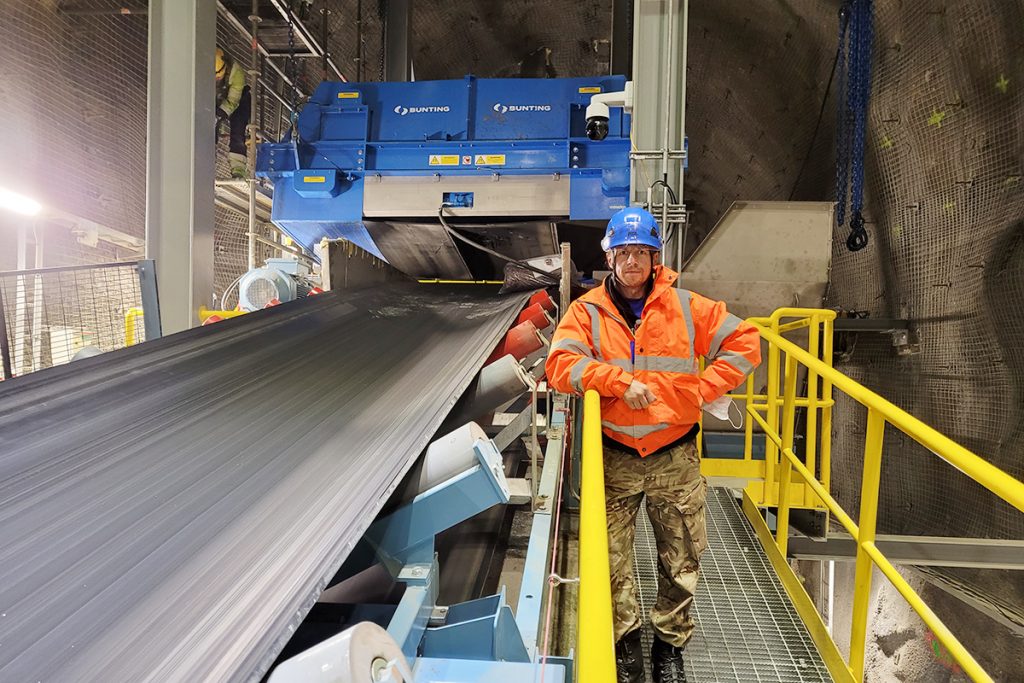
Magnetic Separators Removing Tramp Ferrous Metal
Tramp ferrous metal removal occurs at the mine or quarry and at the processing plant. The process of mining and quarrying rock and ore introduces metal contamination in many forms such as metal bars, digger teeth, nuts and bolts, and discarded metal waste. Magnetic separators separate the magnetically susceptible ferrous tramp metal and work alongside metal detectors that locate non-ferrous metal such as manganese steel. The magnetic separation equipment is located early in the process before the rock or ore is crushed and screened, reducing the risk of costly damage from tramp metal. On plants where there are several stages of crushing and screening, magnetic separators are located between the stages to remove metal liberated in the primary crusher.
The design of magnetic separator is dictated by the plant configuration and size. Permanent and electro Overband Magnets are suspended over conveyors, both across and inline with the belt, with electromagnetic models used for wider conveyors transporting higher tonnages or rock or ore. Magnetic Head Pulleys are an option when the installation of an Overband Magnet is difficult. These replace the head pulley of the conveyor. In ore processing applications such as iron ore and magnesite, where higher magnetic fields are required, large Drum Magnets with vibratory feeders are adopted.
High-Intensity Magnetic Separators for Mineral Processing
High-intensity magnetic separators purify or concentrate non-metallic minerals and magnetic ores. The magnetic separator design is dependent on the nature of the minerals (e.g. particle size, particle shape, composition) and the separation objective.
For dry processing applications, mineral processors use the Rare Earth Roll Magnetic Separator (RE Roll), the Magnetic Disc Separator (MDS), and the Induced Roll Magnetic Separator (IRS).
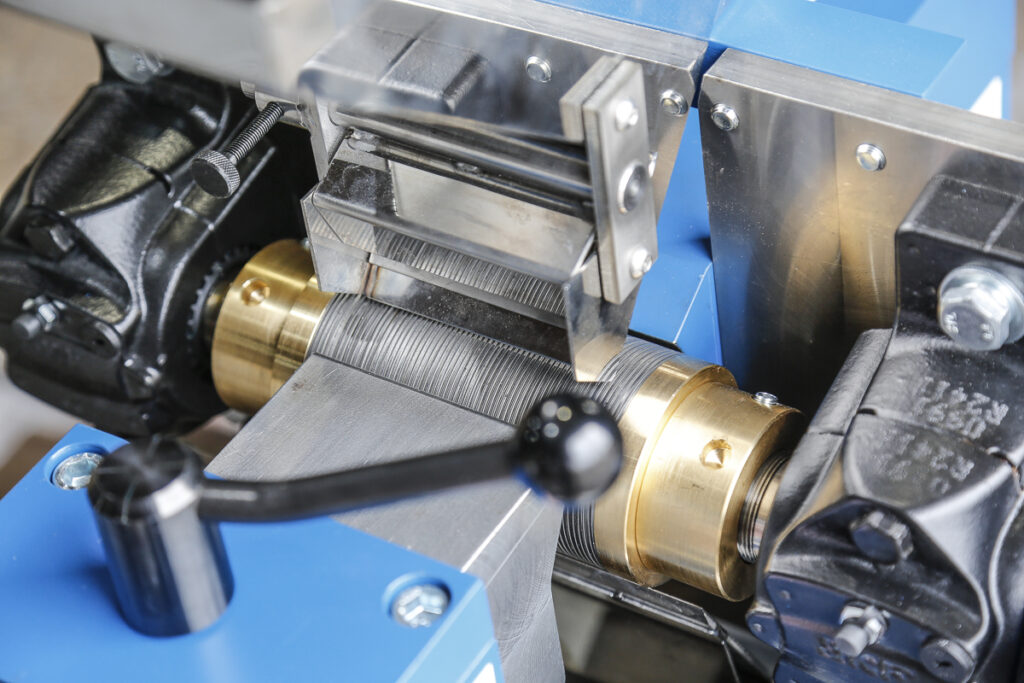
The Induced Roll Magnetic Separator (IRS) uses electromagnetic fields to generate high-intensity magnetic fields, whilst the Rare Earth Roll Magnetic Separator (RE Roll) uses permanent neodymium rare earth magnets. These intense magnetic fields enable the separation of weak and para-magnetic minerals (e.g. mica, iron-coated silica, etc) from non-metallic minerals (e.g. feldspar, silica sand, zircon, etc) in a dry state. Once cleansed, the non-metallic minerals are used in many industries, including ceramics and glass production.
Typically, the electromagnetic Magnetic Disc Separator will feature up to three high-intensity electromagnetic discs, each set at a different height from a feed conveyor. The first magnetic disc is set the furthest from the feed material, in order to extract only the most magnetically susceptible particles. The second and third discs are set at lower gaps, increasing the magnetic force at each disc and therefore separating different grades of magnetic material. Varying the current to each of the coils in the magnetic discs enables adjustment of the magnetic intensity to suit a specific separation objective.
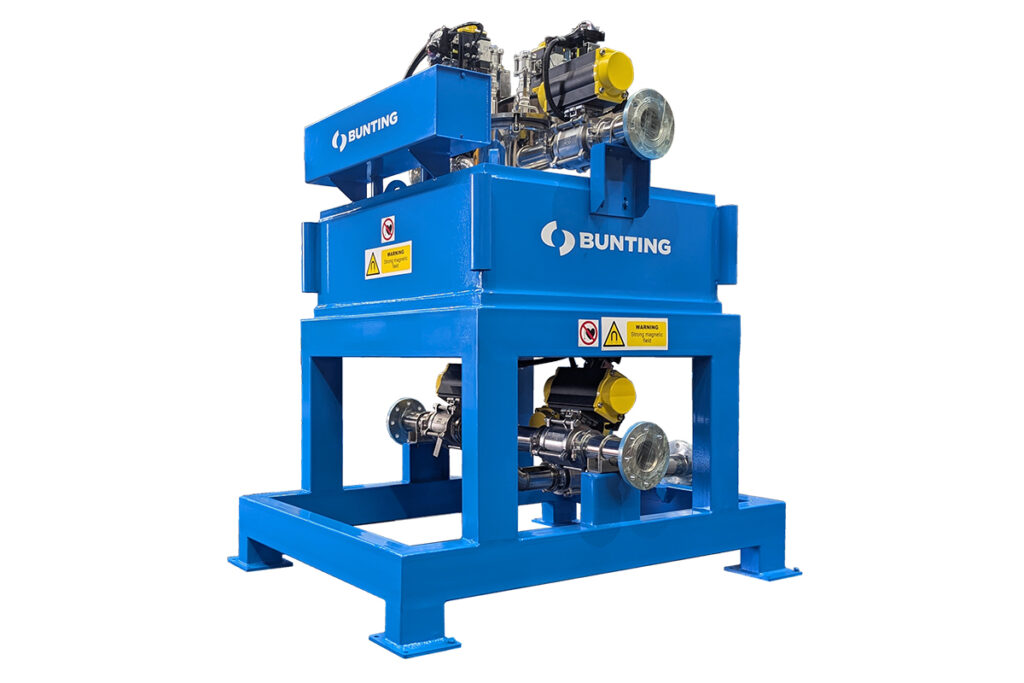
High-Intensity Electromagnetic Filter for Mineral Slurries
The Electromagnetic Filter is adopted for removing magnetically susceptible particles from mineral slurries. The high-intensity, background magnetic field (up to 10,000 Gauss) separates fine iron and paramagnetic minerals. Electromagnetic Filters consist of an electromagnetic coil positioned around a central hollow core containing a magnetic (400 series) stainless-steel matrix of various designs. The coil generates a high intensity magnetic field that becomes intensified on the points of the matrix creating the magnetic force needed to separate paramagnetic particles from the slurry. The process, including automated removal of the captured magnetics, is managed through a separate control panel.
Extending Mineral Reserves
As mineral resources become increasingly depleted, mining companies are turning to reserves that require more processing. This is driving an increase in demand for magnetic separators.