High Intensity Magnetic Separator Optimises Copper Recycling
By Paul Fears | 14 April 2020
Around 50% of copper used in Europe is obtained from recycling rather than newly mined ore (International Copper Study Group – ICSG). Indeed, copper is widely regarded as one of most recycled engineering metals with much of the world’s globally mined copper, some 0.32 trillion kilogrammes, still in circulation.
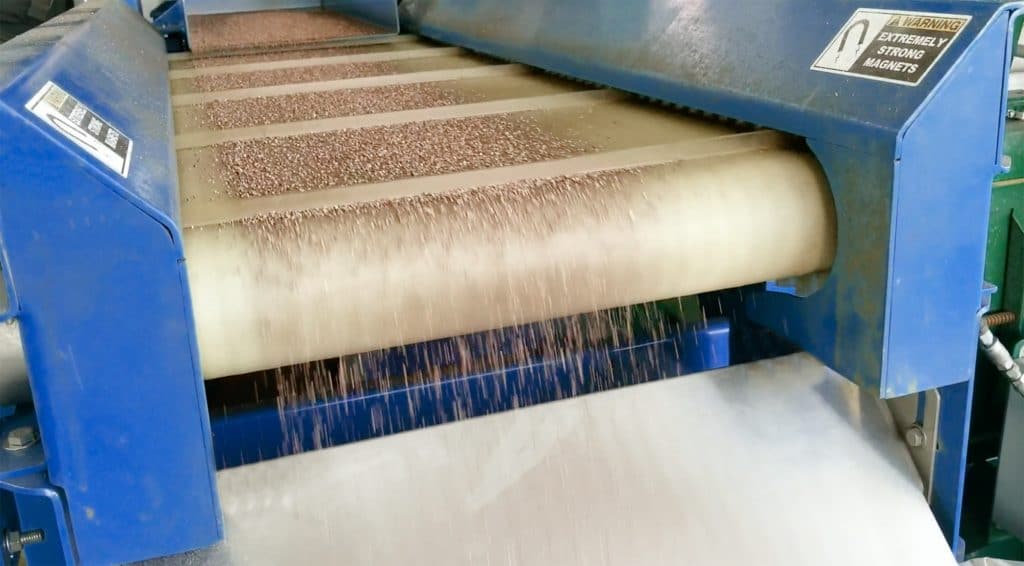
In a typical home there is around 100kg of copper, with 1.5 kg found in most computers. Commonly, a wind turbine uses 5 tonnes of copper. Such demands mean that recovering and recycling copper is vitally important for both environmental and financial reasons. Recycling copper requires up to 85% less energy than primary production and saves around 100 million MWh of electrical energy and 40 million tonnes of CO2 annually.
Copper is 100% recyclable and this valued characteristic is one of many features that makes it such a valuable material. In addition, copper is:
- Highly malleable;
- Resistant to rust and corrosion;
- An excellent conductor of heat and electricity;
- Know for antimicrobial properties;
Such properties make recycled copper a desirable metal with premium-grade scrap commonly commanding at least 95% of the value of the primary metal from newly mined ore.
Recovering and Recycling Copper
The value of recovered copper is proportional to the purity. In many metal and cable recycling operations, especially in the USA, recycling companies are using the High Intensity Separation Conveyor (HISC) to maximise the separation and removal of fragmented stainless steel and ferrous dirt.
- Technical information: High Intensity Separation Conveyor
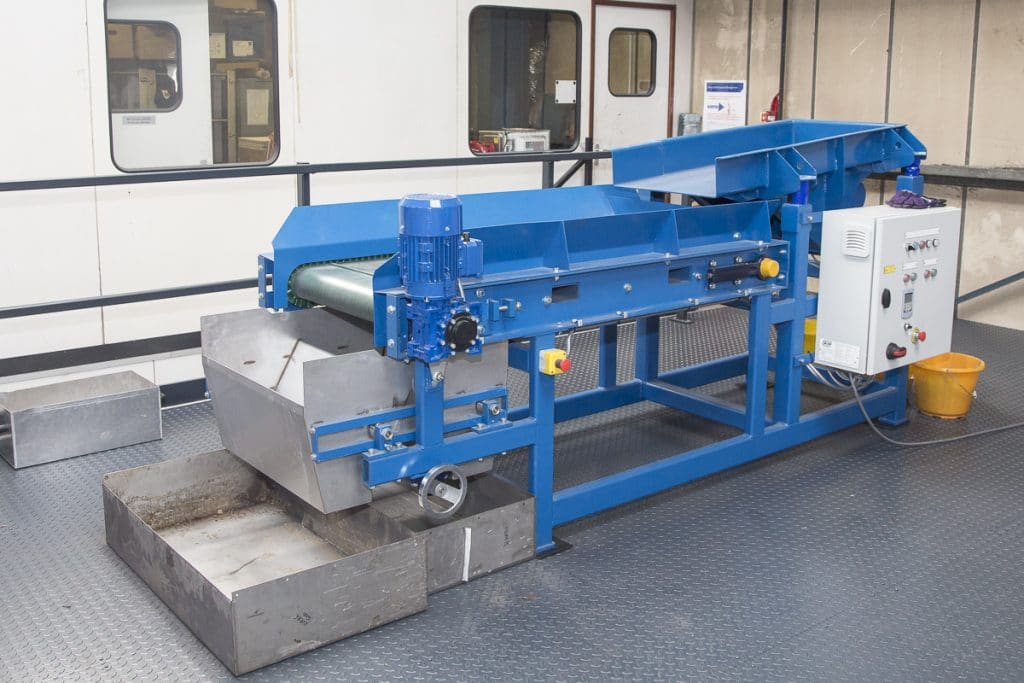
The HISC is a two-pulley conveyor featuring a high-intensity Neodymium Rare Earth magnet as the head pulley. The magnetic design of the head pulley was optimised using Finite Element Analysis software with the simple objective of maximising the magnetic field strength. Such an intense magnetic field would enable the attraction and separation of fine ferrous metal dust and, more critically, paramagnetic metals such as work-hardened stainless-steel.
In operation, the HISC is suitable for both wire pre-chopping purification as well as wire post-chopping purification in insulated copper wire separation applications.
In pre-chopping applications, the HISC removes stainless steel and ferrous dirt contamination to prevent damage to chopper knives. Removing the contamination significantly reduces wear and tear on the chopper knives. This results in improved productivity and profitability due to less knife maintenance and equipment downtime.
For post-chopping applications, the HISC is focused on removing stainless steel and fine ferrous contamination. Successful separation increases the end copper product purity, resulting in improved profitability.
In another project, a combination of an ElectroStatic Separator and a Metal Separation Module is enabling the recovery of fine copper and other metals from a waste product at a UK metal recycling company.
Metal Separation Solutions
The HISC is commonly used in conjunction with other metal separators including:
- Scrap Drum Magnets – for the recovery of large post-shredder ferrous scrap;
- Overband Magnets – for the removal of medium ferrous metals;
- Drum Magnets – for separating smaller ferrous metals;
- Eddy Current Separators – for recovering non-ferrous metals (e.g. aluminium, zinc, etc) from non-metallic materials;
- ElectroStatic Separators – for the separation of fine conducting metals;