Getting Metal Out of Processed Vegetables
By Paul Fears | 29 June 2020
Processed vegetables are a vital part of the food chain. Tens of thousands of bags of pre-cut carrots and freshly prepared kale are bought in supermarkets daily. Frozen vegetables have been very popular since Clarence Birdseye invented the quick freezing method in 1924. Also, often-unnoticed processed vegetables are present in many everyday food items such as tinned soup, baby food, sauces, and ready-made meals. Vegetable processing plants are vitally important to the food manufacturing industry.
However, processing vegetables takes a great deal of care and attention as the products are often delicate and can be easily damaged.
Metal Separator Locations
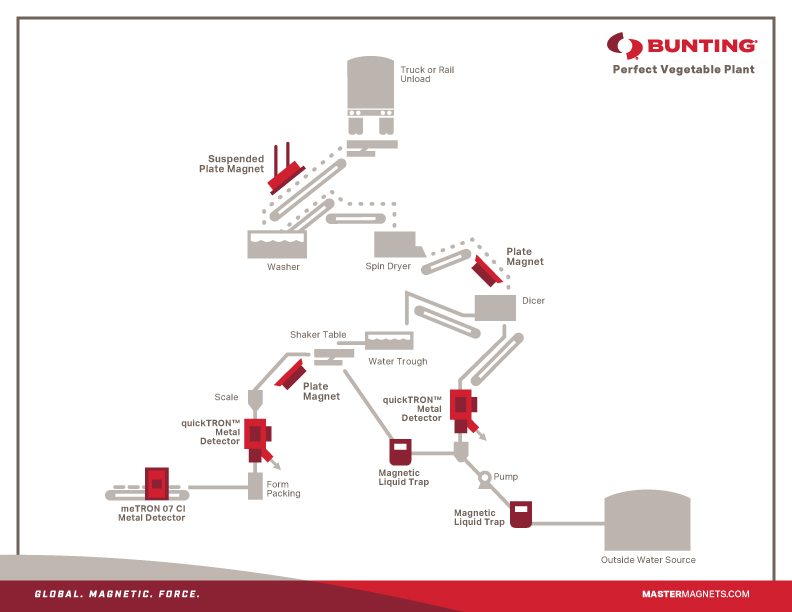
As with all processed foods, there is always the risk of metal contamination. Metal can be introduced at various stages in the process. The design and positioning of the Magnetic Separator or Metal Detector has to also respect the delicate nature of the product.
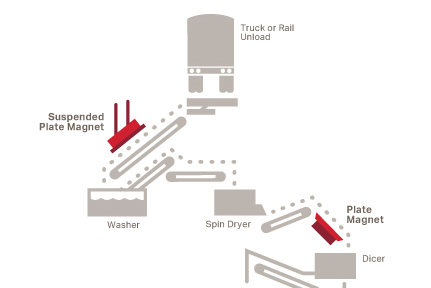
Stage 1 – Untreated Vegetables Feedstock: Magnetic Separator
During the collection and transportation of the raw vegetables, there is always a high risk of picking up metal contamination which would then be fed into the processing plant. Such tramp metal is removed using a magnetic separator such as a Suspended or In-Chute Plate Magnet. The Suspended Plate Magnet avoids any contact with the vegetables, reducing the chance of damaging the food product. The Plate Magnet is suspended above the conveyor feeding the washer. Metal is attracted up onto the face of the Magnet and held until cleaned. This is ideal to remove larger tramp metal items such as screws and nails.
- Technical information: Plate Magnet
Stage 2 – Prior to Dicing: Magnetic Separator
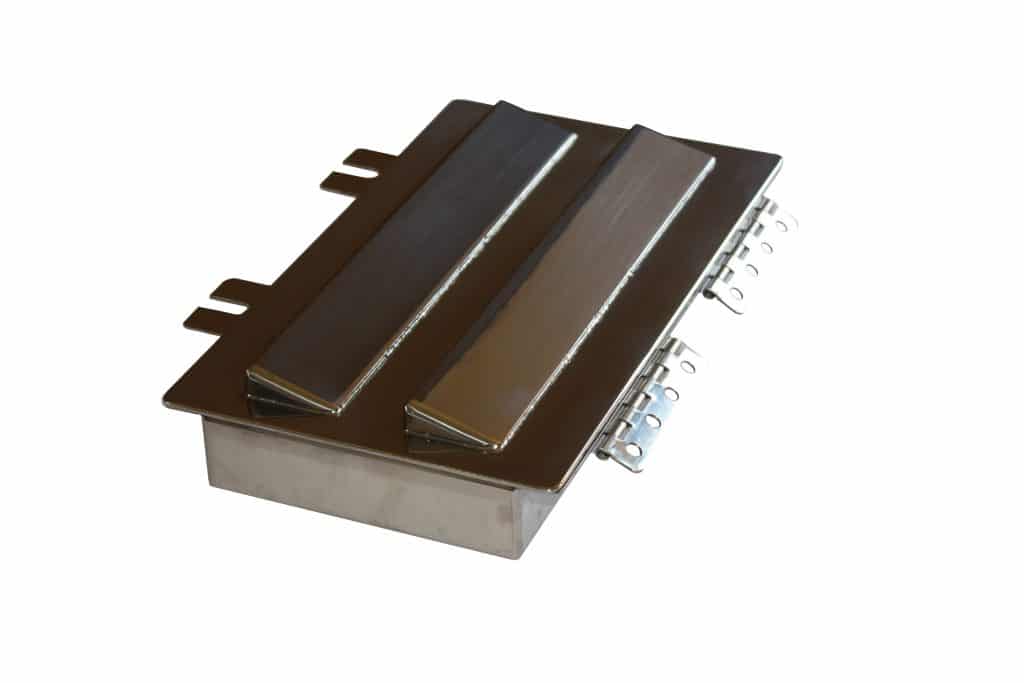
The blades on a dicing machine are delicate and expensive and metal contamination can cause significant damage. To ensure that no ferrous metal is present, the dried vegetables are fed over the surface of a Plate Magnet (featuring one or two tapered steps). Such an installation enables a higher level of ferrous metal separation than when the Plate Magnet is suspended above the material as the vegetables and metal contamination are passing closer to the area of maximum magnetic strength. In practice, the heavier metal contamination migrates to the bottom of the product flow and onto the face of the Plate Magnet. Any potential damage to the vegetables as they flow over the surface of the Plate Magnet is limited as there is no obstruction. The smooth tapered steps on the face of the Plate Magnet enables the removal and entrapment of trapped ferrous metal out of the product flow under the lip of a tapered step.
Stage 3 – Undersized Vegetables: Metal Detector
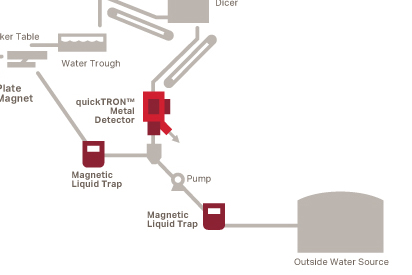
Smaller under-sized diced vegetables are commonly treated on a separate process route. Immediately after dicing, the smaller particles are fed through a quickTRON Metal Detector to remove any small ferrous and non-ferrous metals (including any broken blades from the dicer). They are then mixed with water from an external source for ease of transportation.
- Technical information: quickTRON Metal Detector
Water from the external source is passed through a Liquid Pipeline Magnetic Separator or Magnetic Liquid Trap to ensure that any rust or other ferrous metal contamination is not introduced into the process. The Undersized Vegetables are mixed with the water and then re-introduced into the process.
- Technical information: Liquid Pipeline Magnetic Separator
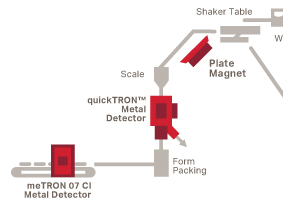
Step 4 – Prior to Packing: Magnetic Separator and Metal Detector
All the vegetables are remixed and fed through a shaker table for sizing into specific products. After the shaker tables, the individual sized fractions are passed over a Plate Magnet (with tapered steps) and through a final quickTRON Metal Detector. The Plate Magnet captures and holds any ferrous metal contamination (e.g. damaged processing equipment such as screens and broken dicer blades), whilst the Metal Detector identifies and removes any non-ferrous metal contamination (e.g. stainless-steel fragments). This combination ensures that all metal is removed prior to the final stage of packing.
Step 5 – Final Packed Product: Metal Detector
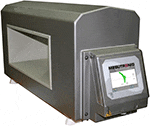
Finally, after packing, the finished packed batch of processed vegetables are passed through a tunnel-type meTRON C07 Cl Metal Detector as a final check for any unexpected metal contamination prior to shipment. This is often required as part of an internal and external (customer) quality control system.
- Technical information: meTRON C07 Cl Metal Detector
This is a typical example of a Vegetable Processing Plant. However, each plant is unique and often a site visit is required to assess and recommend the best ways to ensure a metal-free end product.
For further information on how to remove metal from a food manufacturing process, please contact us on:
Email: Gordon Kerr at GKerr@buntingmagnetics.com
Telephone: +44 (0) 1527 65858
Follow us on social media