Getting Metal Out of Grain and Cereals
By Paul Fears | 11 October 2021
By the time grain and cereals have been collected and delivered to a Milling Plant, it is highly likely that there is metal contamination present. Removing that metal to prevent damage to processing equipment and produce the highest quality end-product is essential and achieved with a series of different designs of Magnetic Separators and Metal Detectors.
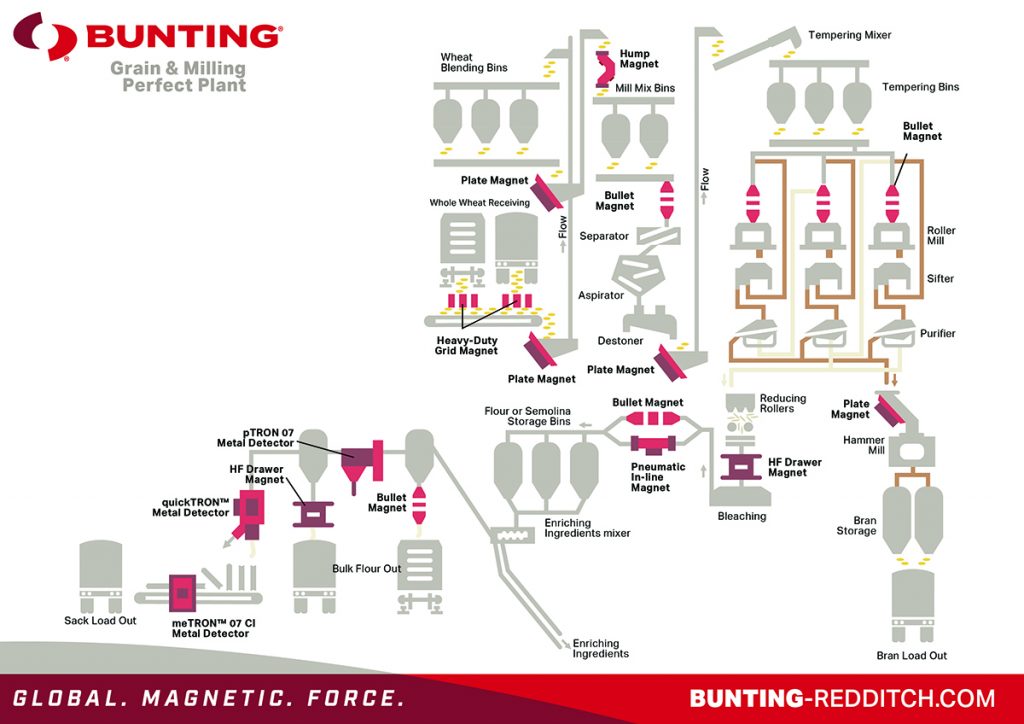
Metal contamination occurs in a wide variety of shapes and sizes such as nails, belts, screws and rust. Unfortunately, such contamination enters the process at multiple stages within the plant., meaning that several stages of magnetic separation and metal detection are required. The following summary acts as a guide as every milling plant is unique. The recommended equipment and locations follow decades of experience working with grain and cereal suppliers.
Metal Separation Steps
Steps 1 – 5 From Raw Material Delivery to Purification
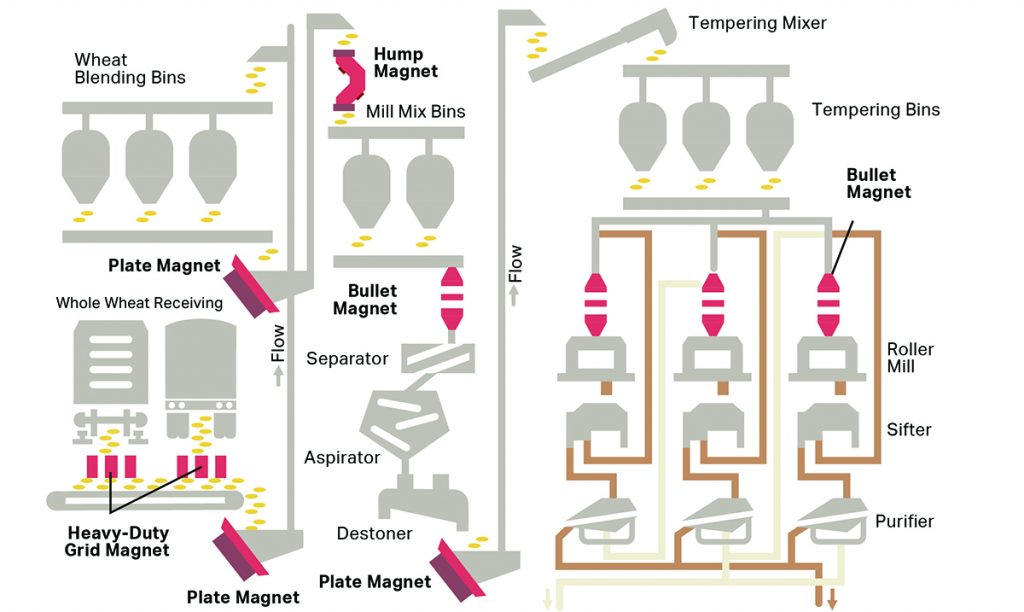
Step 1 – Whole Wheat Receipt
The biggest risk for metal contamination is at the point where raw materials are delivered to the mill. Metal contamination may be in the original farmed materials or in the transport. Subsequently, material being discharged from the back of the transportation is fed through a heavy duty Grid or Grate Magnet, to capture larger tramp ferrous metal. The grain is then conveyed over the surface of a Plate Magnet (to capture smaller tramp metal) and into an elevator before being discharged into Wheat Blending Bins.
- Technical product information: Heavy-duty Grid or Grate Magnet
- Technical product information: Plate Magnet
Step 2 – After Wheat Blending
Material discharging from the wheat blending bins passes over a second Plate Magnet or through a vertical gravity-fed Hump Magnet before being transported to the Mill Mix Bins. A Hump or Cascade Magnet has two Plate Magnets offset inside a doglegged housing, with material falling directly onto the zone of magnetic magnetic field. The material tumbles as it falls from one Plate Magnet to the next, freeing trapped metal contamination which is then captured.
- Technical product information: Hump or Cascade Plate Magnet
Step 3 – After Mill Mix Silos
The wheat mix discharged from the bins through a series of separators including:
- Vertical gravity-fed Bullet Magnet
- Screens for particle size control
- Aspirator to remove fines and heavies
- Destoner to remove field debris
Often a Plate Magnet is also installed after the destoner as a safety net for any breakages of the separation equipment (e.g. a screen mesh). After the multiple stages of separation, the mix is fed into a Tempering Mixer.
- Technical product information: Bullet Magnet
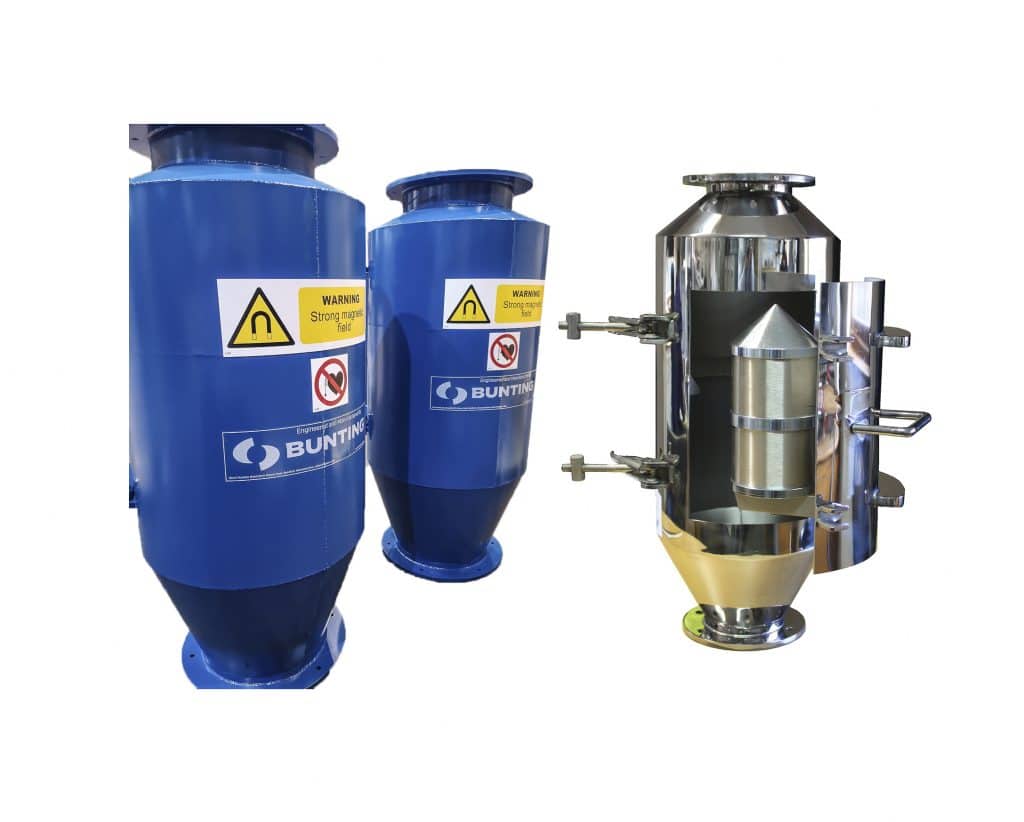
Step 4 – After the Tempering Silos
After the tempering bins, there is a stage of more delicate processing with expensive processing equipment such as roller mills, sifters and purifiers followed by reducing rollers. Metal contamination entering this stage would cause serious and costly damage, as well as disrupting production. On each line, prior to the Roller Mill, the material passes through a Bullet Magnet with an ultra-strong Rare Earth Neodymium Cone. This captures and holds any magnetic metal contamination.
Step 5 – After the Purifier
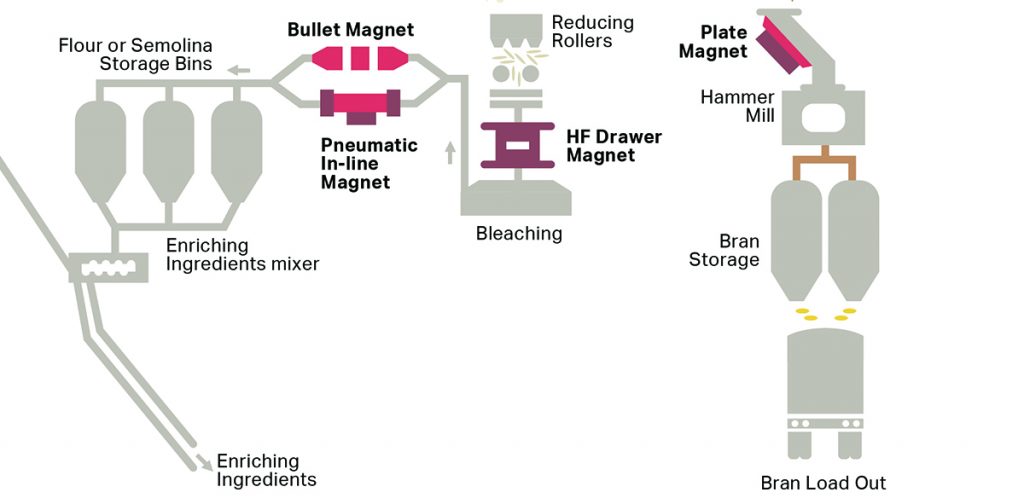
At this stage, the material splits into two different fractions:
- Flour or Semolina
- Bran
As the Bran fraction by-passed the Bullet Magnets and Roller Mill, the material feeds over a strong Rare Earth Neodymium Plate Magnet for magnetic metal contaminant removal prior to the hammer mill. This protects the hammer mill from damage or excessive wear. The Bran is then stored before shipment.
The finer flour or semolina fraction passes through reduction rollers and a HF Drawer Magnet prior to bleaching. Another option is to position magnetic separators after bleaching with either a Bullet Magnet (for vertical gravity-fed lines) or a Pneumatic Inline Magnet (for pneumatically fed lines) prior to storage.
- Technical product details: HF Drawer Magnet
- Technical product details: Pneumatic Inline Magnet (PIM)
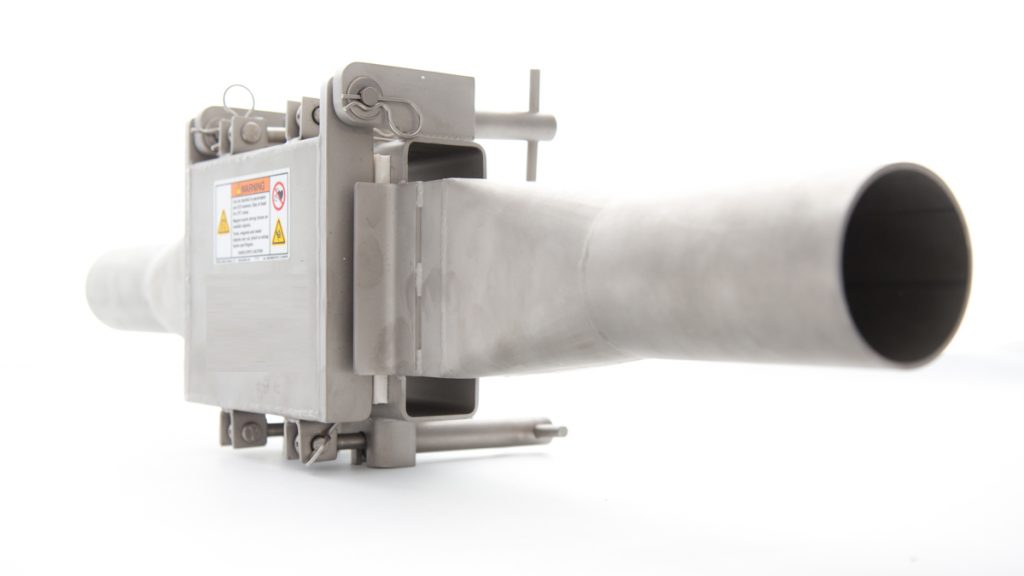
Step 6 – Flour and Semolina prior to Packing and Despatch
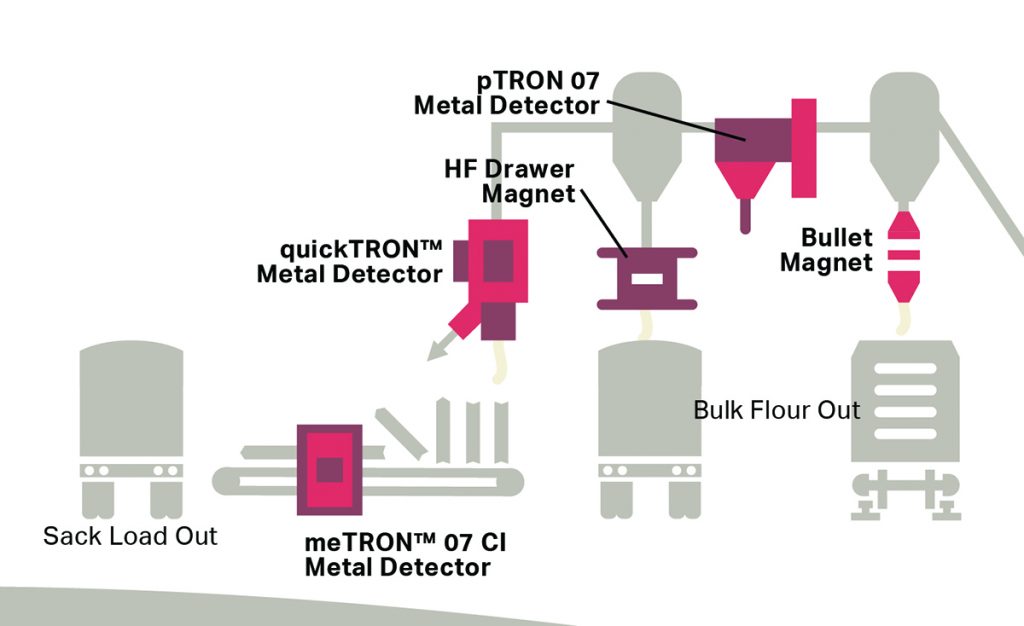
After enrichment, the material is either loaded into transportation vessels or diverted to packing. Immediately prior to loading, the flour or semolina flows through either a Bullet Magnet, HF Drawer Filter or pneumatic pTRON Metal Detector. This is the final check prior to leaving the mill and provides a metal-free guarantee.
On the packing line are two metal detectors:
- quickTRON Metal Detector: the flour or semolina flows under gravity through the metal detector with any metal contaminants being rejected prior to packing. This reduces the risk of packed product rejection;
- meTRON Metal Detector: all packed product passes through a tunnel-type metal detector. This is often requested by the end-customer and provides the final check for metal contamination prior to shipment;
Complete Protection
The multiple stages of metal separation with both magnetic separators and metal detectors may appear excessive, but is necessary due to the nature of the process. Metal contamination, in a wide variety of forms, gets introduced at any stage in the process, especially after milling and during storage. Installing specific designs of Magnetic Separators and Metal Detectors at different locations within the process ensures that the end product is metal-free and eliminates costly metal damage to processing equipment.
Related Metal-in-Food Technical Articles
For further information on Magnetic Separators and Metal Detectors used in removing metal contamination from grains and cereals or for any food processing application, please visit our website or contact us on:
Email: Gordon Kerr at GKerr@buntingmagnetics.com
Telephone: +44 (0) 1527 65858