Ensuring In-House Plastic Recycling Purity
By Paul Fears | 18 January 2021
When re-processing in-house plastic rejects and waste, the purity of the final recycled plastic mix must be equal or at least very close to the original raw material. Whether the re-processed plastic is for in-house use or as regrind for resale, the removal of any metal contamination is critical.
Successful removal of metal contamination from waste plastic for recycling and reuse often requires more than a single stage of separation or detection. The optimum solution is a series of magnetic separators and metal detectors, with the best combination determined by the production process and nature of the waste plastic. Although there are many different configurations of in-house plastic recycling systems, this article focuses on one typical plant layout and suitable separation technology that eliminates metal contamination.
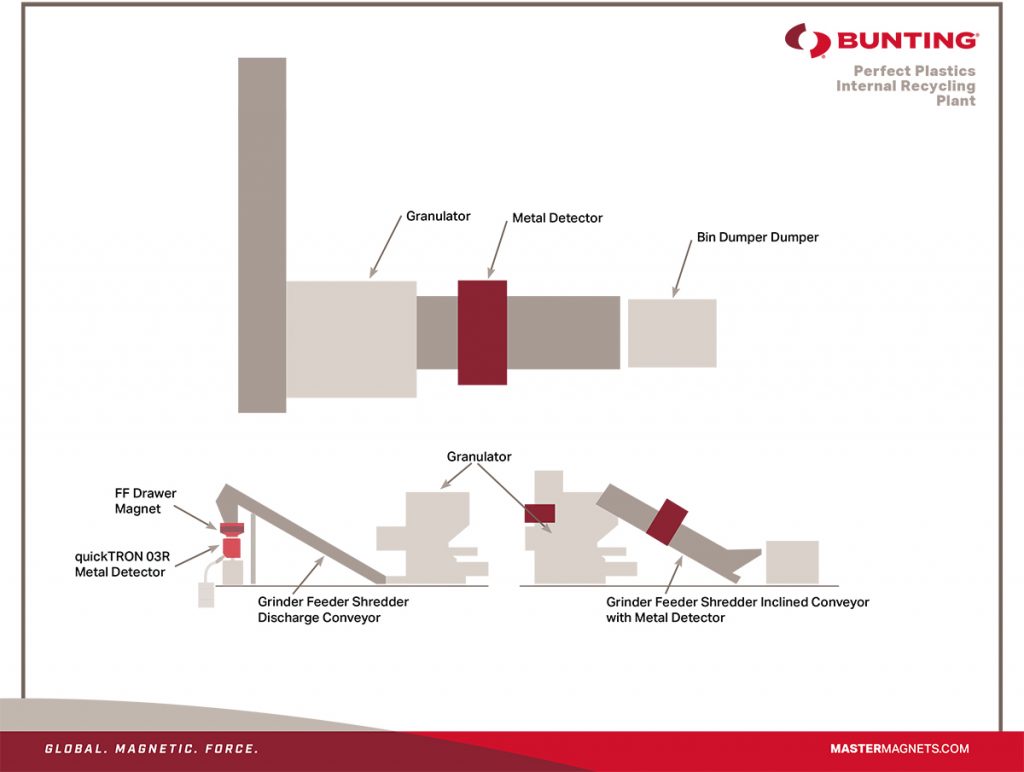
Prior to Granulation
All waste plastic, whether as rejected finished products or off-cuts and internal waste, requires resizing using a granulator and/or shredder prior to reintroduction into the manufacturing process or put aside for resale. Any plastic waste is at risk of being contaminated by metal. Such metal could have been the reason for the original reject, or accidentally added during collection and handling of the waste. A series of strategically located metal detectors and magnetic separators ensure that any metal is both identified and removed to produce a high-specification plastic raw material.
The first stage of metal contamination control is on the feed conveyor to the primary granulator or shredder. A tunnel-style or underbelt metal detector detects pieces of metal, preventing serious and costly damage to the granulator or shredder. In operation, once metal is detected, the conveyor belt stops, allowing operators to locate and remove the metal contamination.
- Technical product information: Metal Detectors
Metal detector sensitivity in tunnel-style models is generally based on the aperture opening size. On an infeed conveyor, the metal detector commonly features a large aperture to handle the high flow volume, and thus will have a lower sensitivity than smaller aperture detectors used in other parts of the plant. Nevertheless, when reviewing the application, the aim is to specify an infeed conveyor tunnel-style metal detector with the smallest aperture possible to maximize detection sensitivity, yet large enough to handle the flow-size and volume of the raw material input. Even large metal detector coils are very capable of sensing pieces of metal that may be hidden inside a purging or a bale.
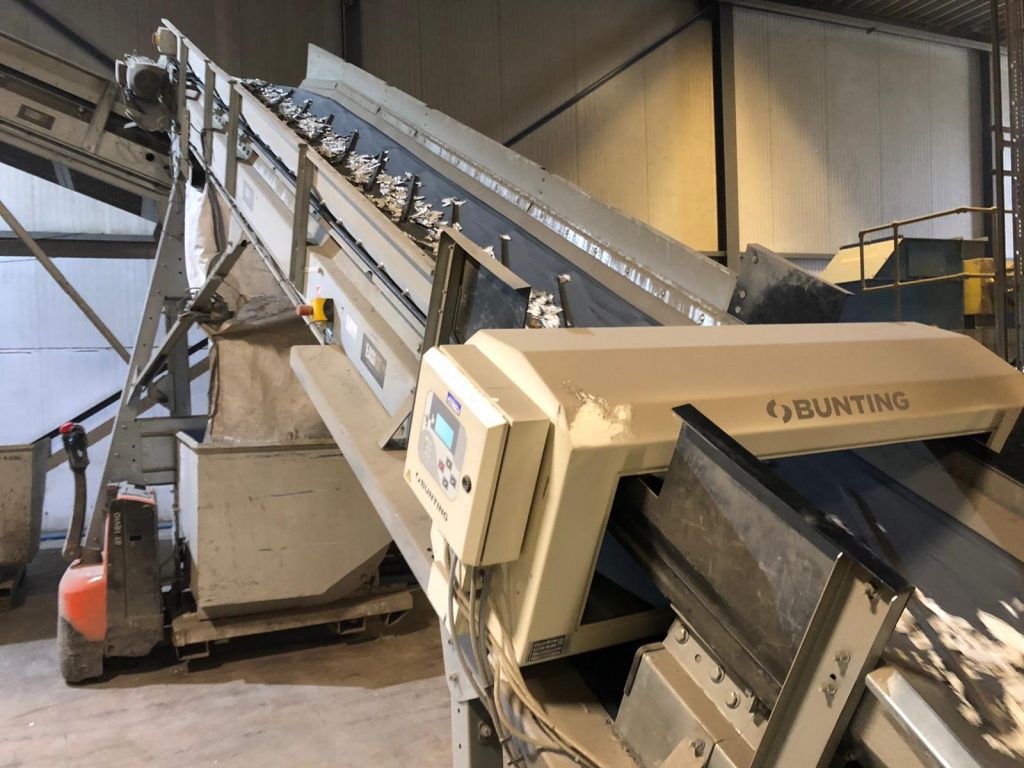
There is a wide range of tunnel-type Metal Detectors, including the meTRON 05C and meTRON 05D. Final selection depends on the required detection sensitivity, the application, and the installation.
Underbelt metal detectors are ideal for applications with smaller burden depths and more difficult installations where a tunnel-style model may cause product flow restrictions. Again, the sensitivity is lower than small aperture tunnel-style metal detectors, but suitable for identifying the type of metal that could damage the granulator or shredder.
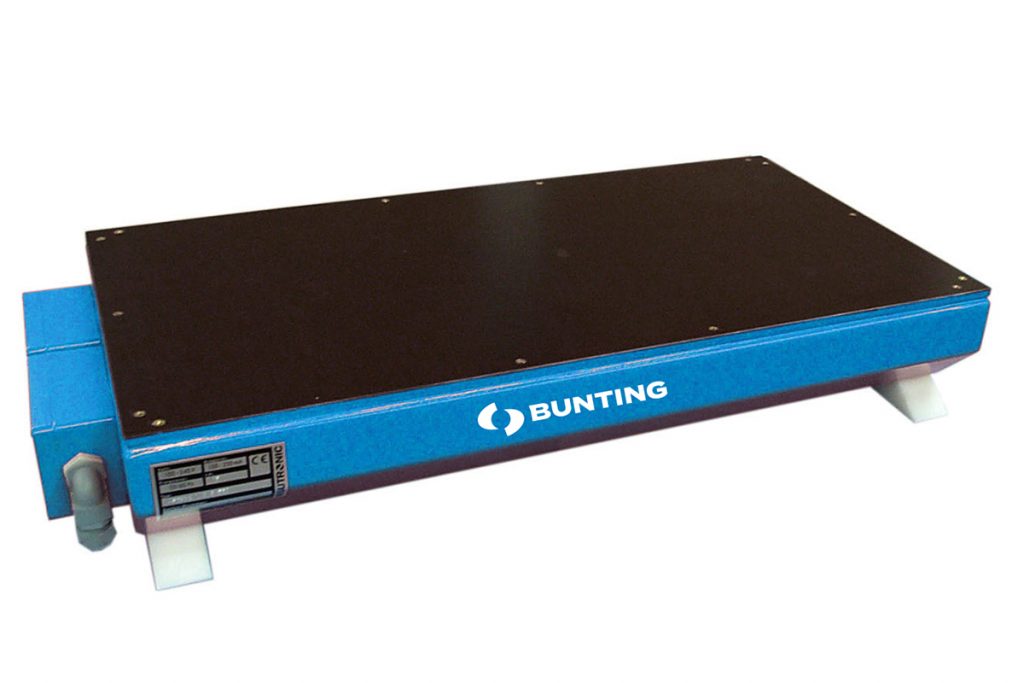
Both the meTRON 03SL and meTRON 05S underbelt Metal Detectors are suitable, with the ultimate selection determined by the required detection sensitivity and the installation.
Successfully removing tramp metal prior to granulation reduces production downtime, limits wear and damage to the granulator or shredder, and also prevents metal contaminants being broken into multiple smaller metal pieces.
Post Granulation
The granulation or shredding process produces a tightly-sized plastic, whilst also liberating any entrapped metal contamination. In a typical plant, the resized product travels up an inclined conveyor before cascading down, under gravity, into a collection area.
After leaving the inline conveyor, when the material is in free-fall, the combination of a FF Drawer Filter Magnet and quickTRON Metal Detector – acting as a Metal Cleaning System – captures ferrous metal and also automatically removes non-ferrous metals and stainless-steel. This ensures that the final re-processed waste plastic is metal-free prior to being reused or sold as regrind.
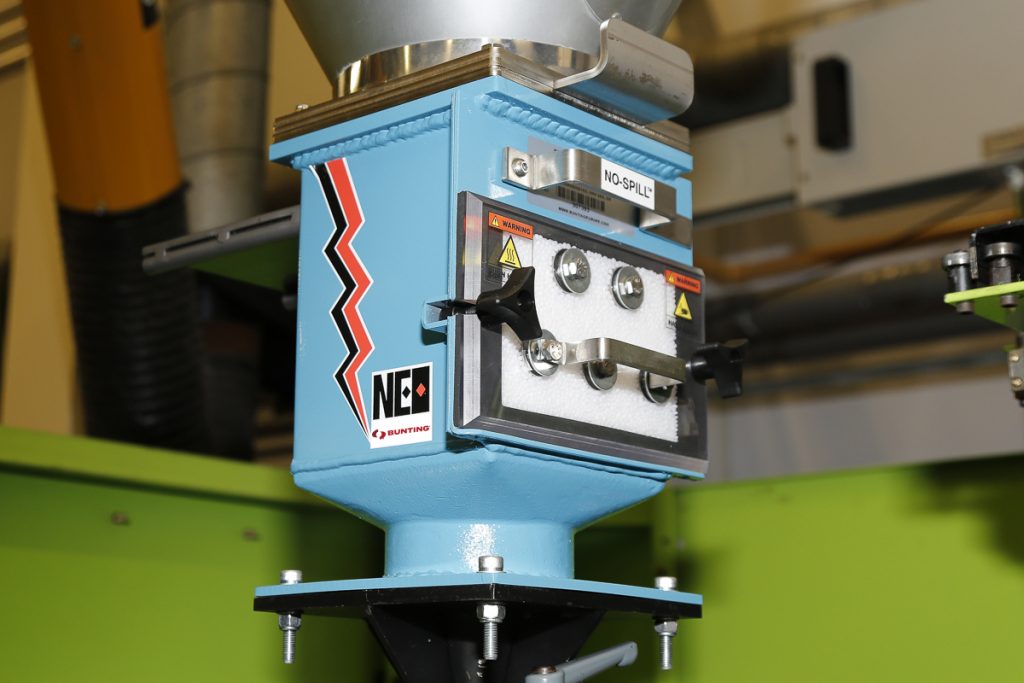
The FF Drawer Filter Magnet is equipped with powerful Neodymium Rare Earth Tube Magnets to extract and hold ferrous particles present in gravity flow or free-fall applications. This magnetic separator is designed specifically for the plastics industry and is the only available Drawer Filter Magnet featuring temperature-compensated rare earth magnets. This enables operation at high temperatures (up to 175°C), without compromising on the magnetic force, as found on some extruders as well as injection and blow moulding machines.
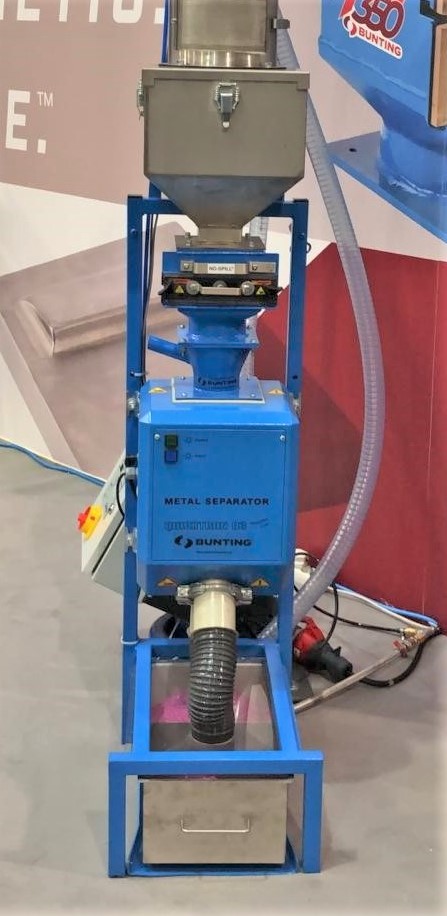
- Technical Product Information: FF Drawer Filter Magnets
The quickTRON 03R Metal Detector automatically and continuously detects both entrapped and liberated tramp ferrous, stainless-steel and non-ferrous metals. Designed specifically for gravity-fed applications, the quickTRON 03R is compact and easy to install in new and existing installations. The main aperture ranges from 30mm to 200mm (1¼” to 8”) to suit a wide range of applications and throughputs.
- Technical Product Information: quickTRON Metal Detector
Total Metal Separation Solution
The right combination of metal detectors and magnetic separators enables plastic producers to minimise waste without compromising on product quality or risking damage to processing plant. The cost benefits are significant in terms of reduced waste costs (from either reuse or income from the on-sale of regrind) and improved productivity with reduced equipment downtime due to plant damage and wear.
For further information on Bunting’s range of Magnetic Separators and Metal Detectors for the plastics industry or to discuss a specific application, please contact our technical sales team on:
Email: Gordon Kerr at GKerr@buntingmagnetics.com
Telephone: +44 (0) 1527 65858
Follow us on social media