Electrostatically Recovering Copper Wire
By Paul Fears | 26 October 2020
A combination of an ElectroStatic Separator and a Metal Separation Module is enabling the recovery of fine copper and other metals from a waste product at a UK metal recycling company.
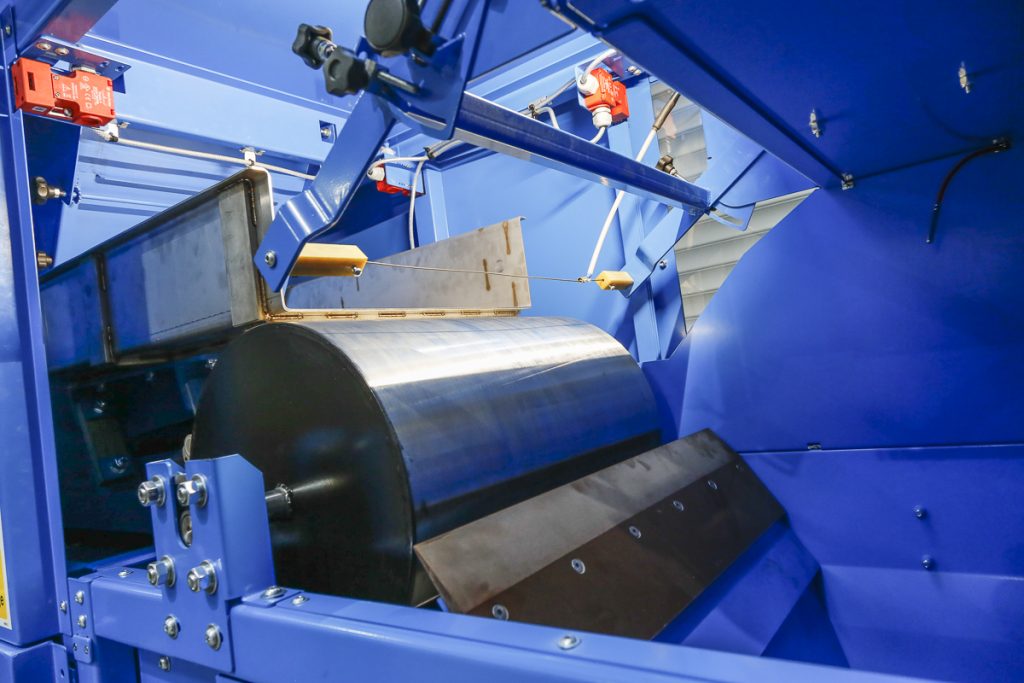
ElectroStatic Separation
The Bunting ElectroStatic Separator, launched in 2020, significantly enhances the ability of companies to recover fine metals such as copper wire. In this project, the feed material is fine material from air-extraction post-shredding; a mix normally classified as waste despite the valuable metal content. Previous attempts to recover the metal constituent, including fine copper wire, had been unsuccessful.
- Technical product information: ElectroStatic Separator
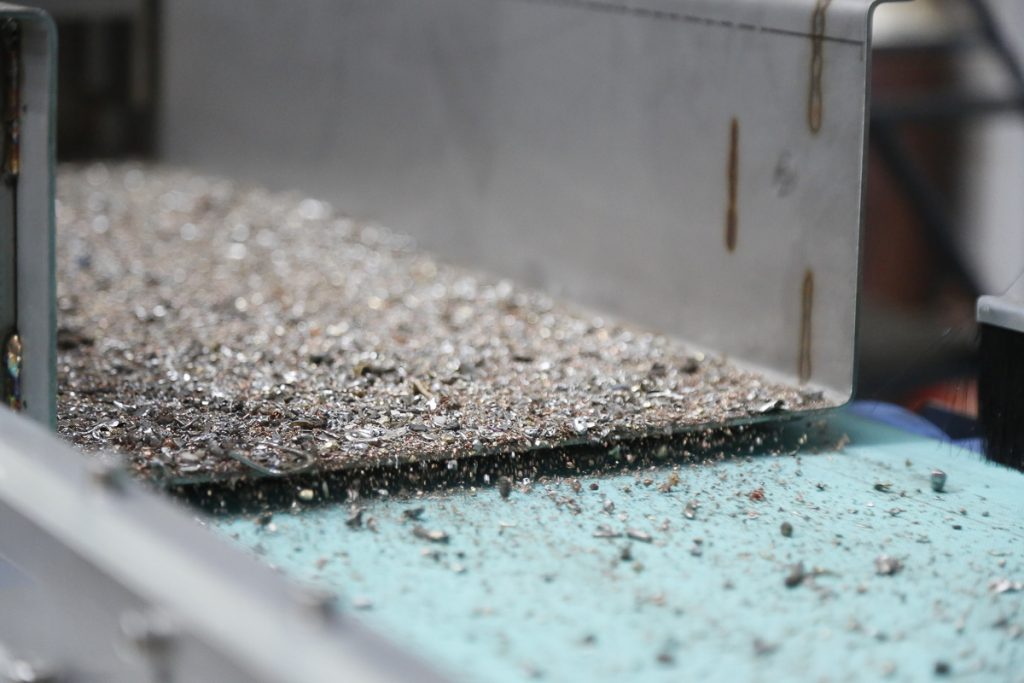
Prior to ordering the equipment, controlled tests conducted at Bunting’s Customer Experience Centre in Redditch determined that a three-stage separation process would enable high levels of metal recovery and purity.
On site, between one and two tonnes per hour of the metal mix initially passes through the Metal Separation Module before the final stage of ElectroStatic Separation. The Metal Separation Module consists of a Ferrite Drum Magnet, Vibratory Feeder and high-intensity Rare Earth Roll Separator. The Ferrite Drum Magnet removes strong magnetic metal with the remaining mix passing onto the Vibratory Feeder. This regulates and presents an even, monolayer of material onto the belt of the Rare Earth Roll Separator.
- Technical product information: Permanent Drum Magnet
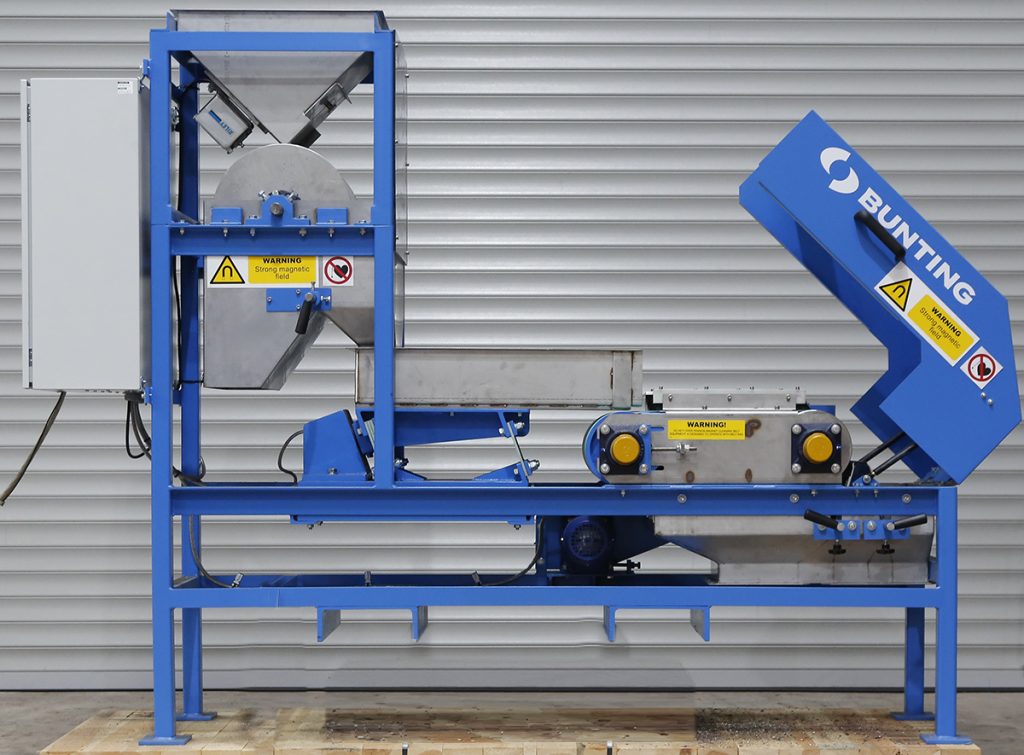
Rare Earth Roll Magnetic Separator
The Rare Earth Roll Separator has a thin belt feeding material onto a head pulley constructed from high-strength neodymium rare earth magnets. As material passes over the head roll, weakly magnetic metals are attracted to the radial high-intensity field and held on the belt and then deposited underneath. A strategically placed splitter enables the separation of the attracted metals (including fragmented stainless-steel) from other non-magnetic materials (e.g. fine copper wire and aluminium).
- Technical product information: Rare Earth Roll Magnetic Separator
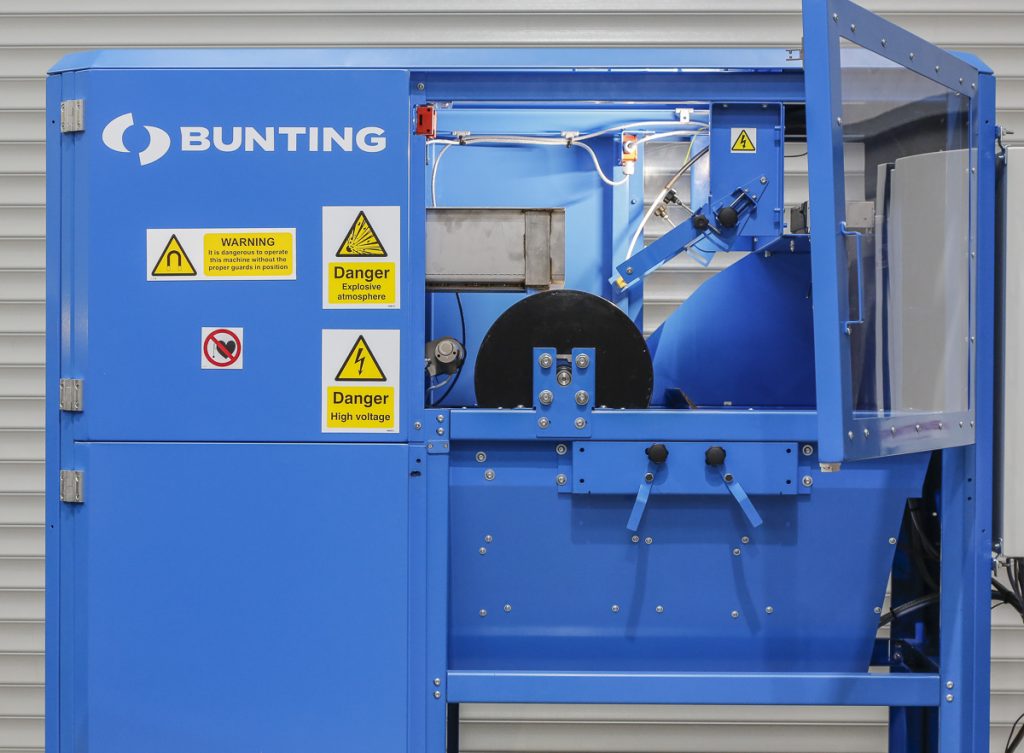
This non-magnetic metal mix passes onto the third separation stage to recover fine copper wire at a feed rate of approximately one tonne per hour. The ElectroStatic Separator is a recent additional to the range of Bunting metal separators. The technology produces a separation by exploiting the difference in electrical conductivity between various materials in a feed material. This enables the recovery of metals such as fine copper wire. In this project, the recovered copper wire has a purity of +95%.
Developing new metal separation processes, such as this three-stage Magnetic Separator and Electrostatic Separator system, is vitally important to reduce the amount of metal lost to waste and of unrecyclable material sent to landfill. There is also significant financial gain, with increased metal recovery and reduced disposal costs.
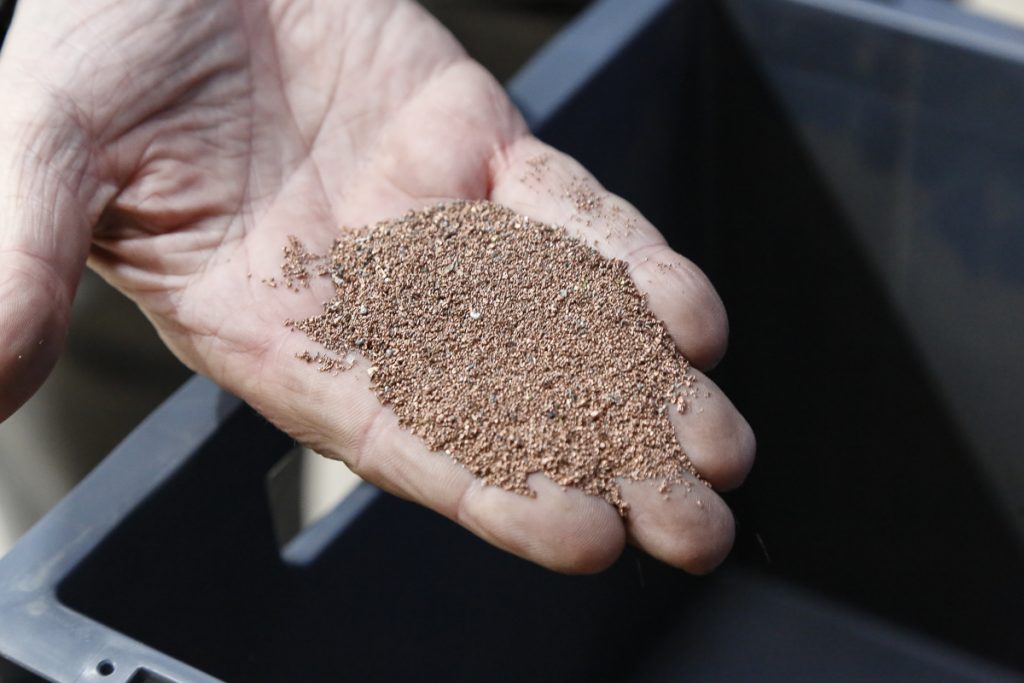
Investigating metal separation possibilities at Bunting’s Redditch Customer Experience Centre provides experienced process engineers with the technology needed to maximise both metal recovery and purity. Bunting invites companies to contact Bunting to arrange such test work.
Related Recycling Case Histories
For additional information on magnetic separators, eddy current separators, metal detectors, and electrostatic separators used to separate and recover metals, please contact us on:
Email: Gordon Kerr at GKerr@buntingmagnetics.com
Telephone: +44 (0) 1527 65858
All photographs taken by Paul Fears Photography
Follow us on social media