ElectroStatic Separation of Minerals
By Paul Fears | 01 June 2020
Article written by Neil Rowson, Professor of Minerals Engineering in the School of Chemical Engineering at the University of Birmingham
Electrostatic phenomenon dates back to 600 – 700 B.C. when people noticed static electric effects (attraction of hair) when amber was rubbed with fur. Indeed, the word ‘electrostatic’ comes from the ancient Greek word ‘electron’ meaning amber.
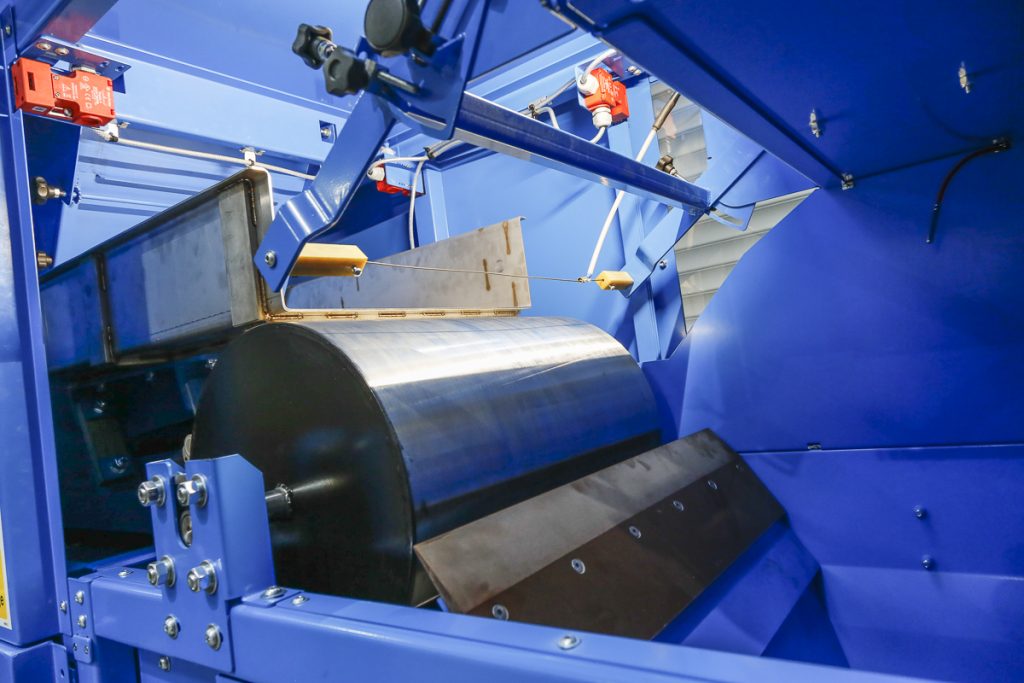
Electrostatic beneficiation
Electrostatic beneficiation of dry granular plant-based food (i.e, organic) materials have been investigated for over 140 years, with the first patent for electrostatic separation of wheat flour middlings filed as early as 1880. In the late 1890s, Thomas Edison designed a machine to separate non-magnetic iron ore from sand-like particles in the absence of water. His electrostatic separator accepted a thin film of dry particles to pass over an electrically charged drum. During the Gold Rush in the Ortiz Mountains southeast of Santa Fe in New Mexico, Edison learned that gold would stick to the drum while sand was repelled, resulting in the first patented a gold concentrator using electrostatic principles.
In the early 1900s, electrostatic separation became popular in mineral processing, until the advent of froth flotation. However, in more recent times, the move towards environmentally-friendly processing techniques (i.e. reducing the use of chemicals) and with many mineral processing plants facing water supply issues, there is an increased interest in the electrostatic separation of minerals in a dry state.
- Technical product information: ElectroStatic Separator
Principles of ElectroStatic Separation
Every mineral species has electrostatic properties that can potentially allow separation in an external electrostatic field. Mineral processing categorises minerals into conductors and non-conductors (dielectric) materials. When an electrostatic field is applied they behave differently, thus enabling a separation.
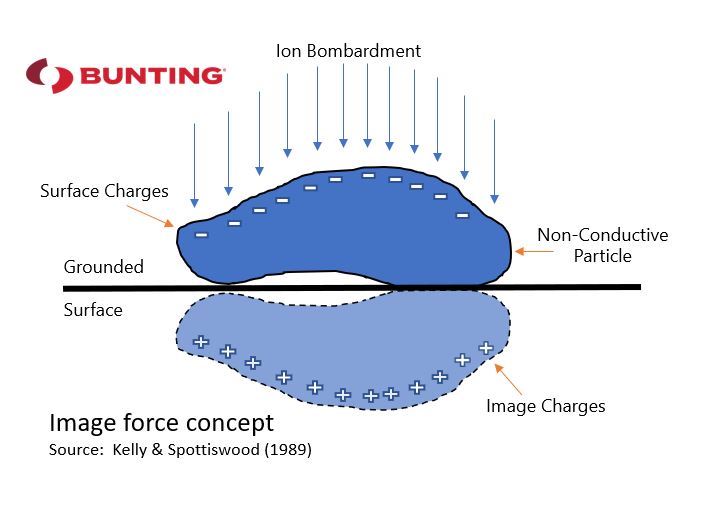
Conductor minerals (most sulphides) will lose the charge to an earthed surface, whilst non-conductors will retain the charge and be pinned to the earthed surface. This effect is known as ‘image charge’ and is the operating principle of the ElectroStatic Separator.
Applications
Electrostatic separation enables the separation of a wide range of minerals and this example, separating Pyrite from Silica Sand, provides a good example of the separation process.
A feed of conducting (Pyrite FeS2) and non-conducting (Silica Sand SiO2) powders is fed via a vibratory feeder onto an earthed, stainless-steel roll revolving at a pre-determined rate. A strategically positioned electrode assembly, at around 20° from the vertical, charges the feed at a high voltage (20 – 30 KeV). As the mineral particles leave the vibratory feeder and land on the roll, two behaviours are observed:
- Conductors (i.e. Pyrite) – lose their charge and are thrown by centrifugal force off the roll;
- Non-Conductors (i.e. Silica Sand) – have an image change and are pinned on the roll and discharged by a brush (see Figure 1);
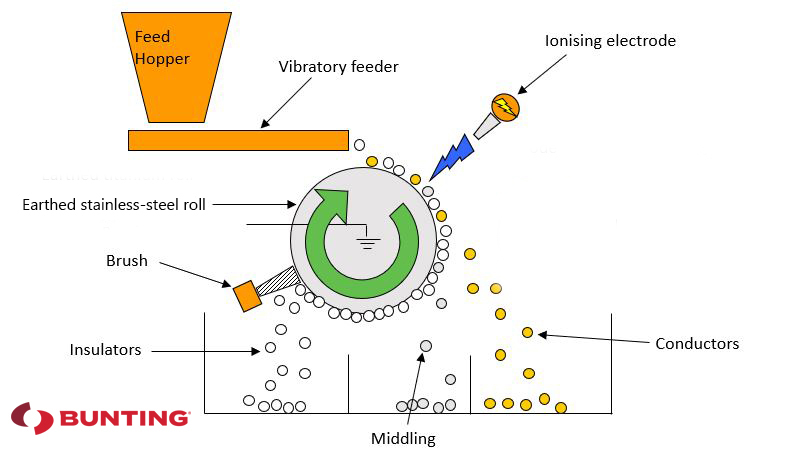
Separation Variables
The mineralogy of a sample dictates the ElectroStatic Separator settings. Controlled laboratory tests at Bunting’s Centre of Excellence (near Birmingham in the UK) identify the key parameters needed to optimise and then meet the separation objective. The key control variables for separation are:
- Material:
- Particle size range of material (> 4mm <100 microns);
- Low moisture content of the feed;
- ElectroStatic Separator
- Applied voltage;
- Roll speed;
- Splitter plate position;
- Low humidity atmospheric conditions (hence units have heaters);
- Electrode position;
Minerals Separated Using ElectroStatics
The list of minerals classed as conductive and non-conductive minerals is extensive. Such mineral mixes are ideally suited for separation using the ElectroStatic Separator. The following list is not comprehensive, but is provided as a guide.
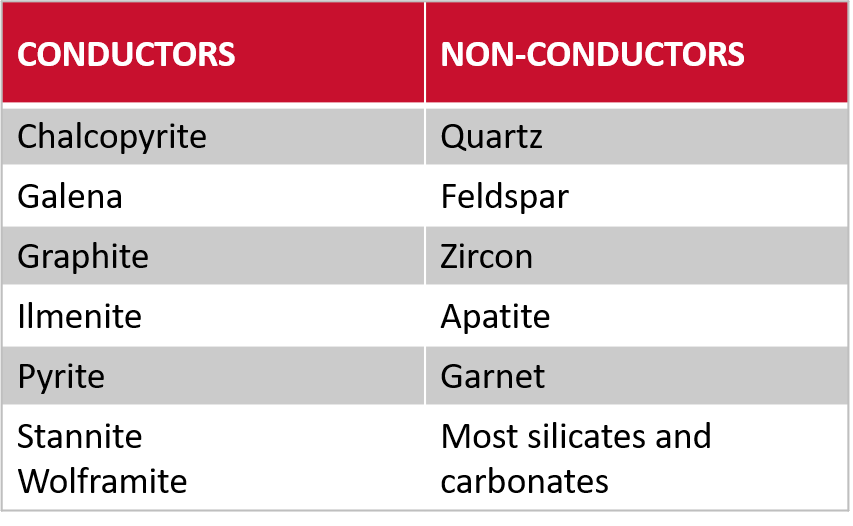
Combined Mineral Separation Solution
ElectroStatic Separators are commonly used in conjunction with high-intensity Magnetic Separators. A classic example is when processing complex beach sands.
For the primary separation, a Magnetic Separator (typically an Induced Magnetic Roll or Rare Earth Roll Separator) removes magnetically-susceptible para and ferro magnetic minerals (e.g. ilmenite, garnet, monazite). The secondary electrostatic separation focuses on separating the remaining minerals (e.g. zircon sand, silica and rutile).
When processing beach sands and similar minerals reserves, the electrostatic separator has the advantage of processing materials in a dry state (unlike froth flotation). In a beach sands processing plant, a 1.5m wide ElectroStatic Separator would typically process between 3-5 tonnes per hour.
A Changing Future
Mineral processors have never faced greater challenges. There is a focus on mining lower quality reserves or reprocessing waste materials, both requiring higher degrees of processing. Environmental considerations are paramount, whether that is availability of resource (i.e water) or the effect on the local natural habitat. These considerations often dictate the processing method.
Electrostatic separation, often in combination with magnetic separation, offers a solution.
Related Mineral Processing Technical Articles
For additional information on the ElectroStatic Separator, the magnetic separation of minerals, or to arrange a test in the Centre of Excellence please contact us on:
Email: Gordon Kerr at GKerr@buntingmagnetics.com
Telephone: +44 (0) 1527 65858
All photographs taken by Paul Fears Photography
To keep up to date with our news and technical reports, please follow us on social media