Detecting and Removing Tramp Metal from Conveyors
By Paul Fears | 29 April 2019
The process of quarrying aggregate and mining ore often results in the introduction of tramp metal. The effective detection and removal of this tramp metal is critical to prevent damage to crushers, screens and conveyors, and is achieved using metal detectors and magnetic separators.
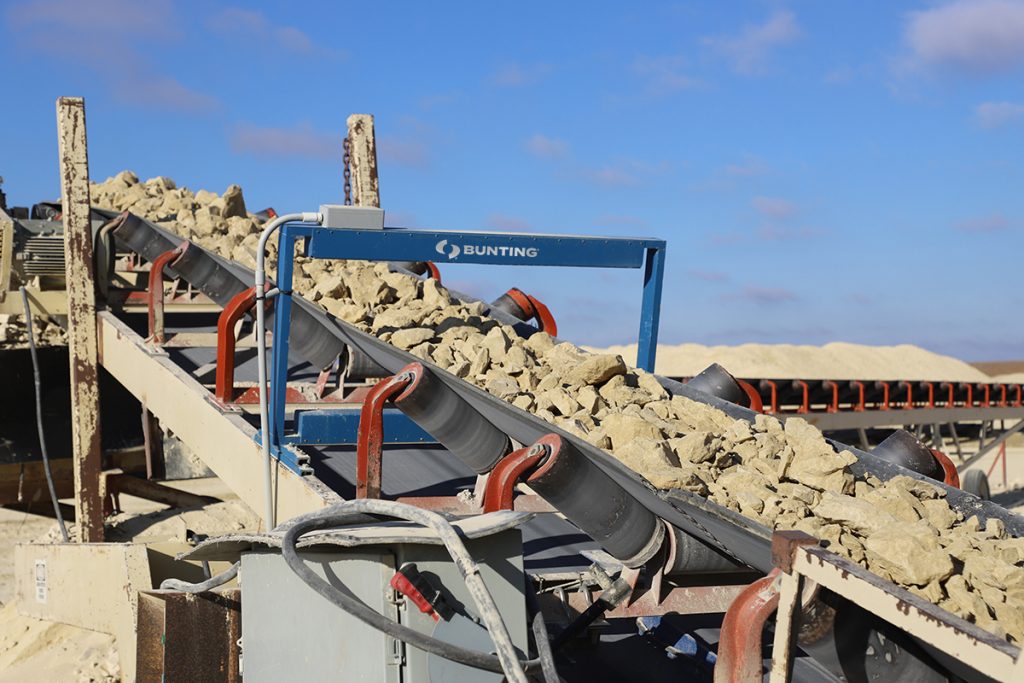
The design of metal detector or magnetic separator is dependent upon the application. Understanding the nature (e.g. size, shape, composition, origin) of the tramp metal is important. Typical tramp metal will include digger teeth, drill rods, crusher plates, bars, chains, nuts and bolts. A review of the plant layout, identifying critical machinery at risk from tramp metal, highlights potential locations. Once the application details are known, it is possible to recommend an optimum solution to detect and or remove the tramp metal.
Metal Detection
Metal Detectors are available in a wide variety of designs. However, they all operate using the same principle. Inside a Metal Detector is a coil which, when electricity is passed through, produces a magnetic field. This magnetic field is stable until the introduction of a metal particle. The subsequent change in the magnetic field is recognised by a control.
In a quarry or mine, Metal Detectors are commonly located underneath or around a conveyor belt. When tramp metal enters the magnetic field of the metal detector, the control either stops the conveyor or can divert the contaminated product flow.
Bunting-Redditch manufacture three designs of metal for the quarrying and mining industry. All the metal detectors provide an automatic and continuous inspection of all conveyed materials, which are non-metallic or non-conductive. The design means that all three types can be fitted without cutting the conveyor belt. The wall mounted control panels are all rated to IP65.
TN77 Conveyor Belt Metal Detector
The TN77 metal detector is a tunnel-type design and detects tramp iron and low grade manganese steel. This design ignores non-magnetic copper alloy conveyor belt fasteners. The control panel also indicates if 1 of 2 pieces of tramp metal have been detected.
Magnetic Separators
Whereas Metal Detectors identify all tramp metal objects, magnetic separators only attract and remove magnetically susceptible ferrous metal. Magnetic separators and metal detectors are commonly used together. Tramp ferrous metal is removed by the magnetic separator and then non-ferrous metal (e.g. manganese steel) is identified by the metal detector.
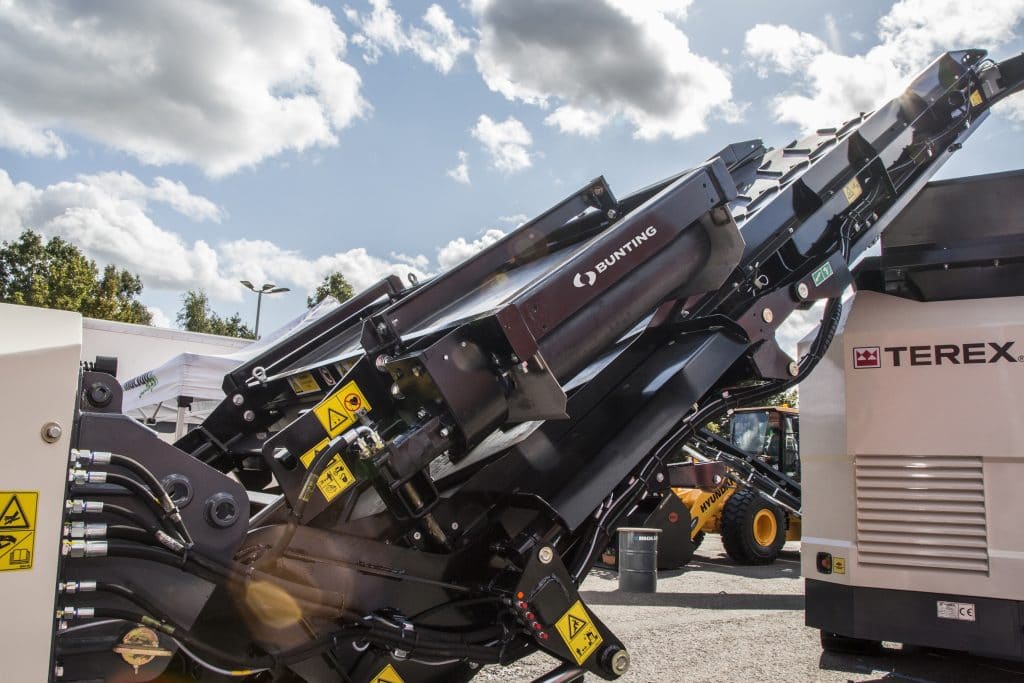
The most commonly used designs of magnetic separators include the Overband Magnet and Pulley Magnet.
Overband Magnet
The Overband Magnet has a magnetic field produced by permanent magnets or an electromagnetic coil. When the Overband Magnet is suspended above a conveyor, the magnetic field is projected down into the conveyed material. Tramp iron passing into the magnetic field is attracted up off the conveyor and away from the burden of material.
Permanent Overband Magnets are an industry standard, featuring in quarries and on mobile screens and crushers. Electro Overband Magnets are heavier duty and are used when conveyors are transporting high tonnages of material. The Electro designs produce deeper and stronger magnetic fields. Both the permanent and electro designs are supplied with and without self-cleaning gear.
Pulley Magnet
A permanent Pulley Magnet replaces the head pulley of a conveyor. A magnetic field is projected up through the conveyor, continuously attracting any tramp metal in the conveyed material. The tramp metal is held to the conveyor belt by the magnetic field, before bring automatically removed when the conveyor belt leaves the surface of the pulley.
Good Protection Means Less Downtime
Installing the optimum metal detectors and magnetic separators ensures the protection of process equipment. Damage to crushers, screens and conveyors is not only inconvenient and time-consuming, but costly in downtime and missed production.
Related Articles
For additional information on detecting and removing metal from conveyed materials, please contact us on:
Email: Gordon Kerr GKerr@BuntingMagnetics.com
Telephone: +44 (0) 1527 65858
Follow us on social media