Cleaning Recycled Plastic with Bunting Inline Magnets
By Paul Fears | 29 July 2024
A manufacturer of window frame bodies is using Bunting’s Pneumatic Inline Magnets (PIMs) to cleanse recycled plastic flake of ferrous metal contamination. In production, each window frame uses up to 40% recycled plastic.
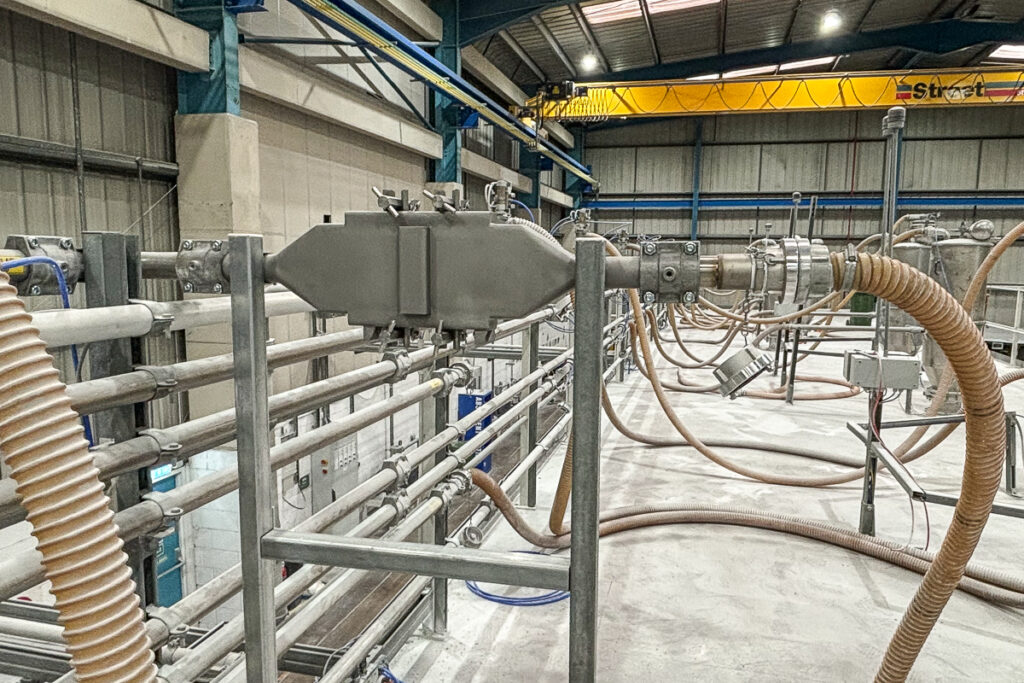
Inline Magnets are versatile and cost-effective magnetic separators that connect into both gravity-fed and pneumatic pipelines. With a plate magnet fitted on one or both sides of the body, the Inline Magnets are ideal for removing occasional tramp ferrous metal from materials transported in pipelines.
Pneumatic Inline Magnets
There are four (4) Pneumatic Inline Magnets installed at various locations in the plant. Two are in fixed positions and two are mounted on mobile stands for easy repositioning at key positions in the process.
In operation, plastic flake is pneumatically fed horizontally through the centre of the housing and close to the surface of a high-strength neodymium plate magnet. Tramp ferrous metal and any other magnetically-susceptible particles, including fine iron, are attracted to the surface of the plate magnets and securely held. A scheduled maintenance programme includes the regular manual cleaning of the plate magnets, removing any captured magnetics.
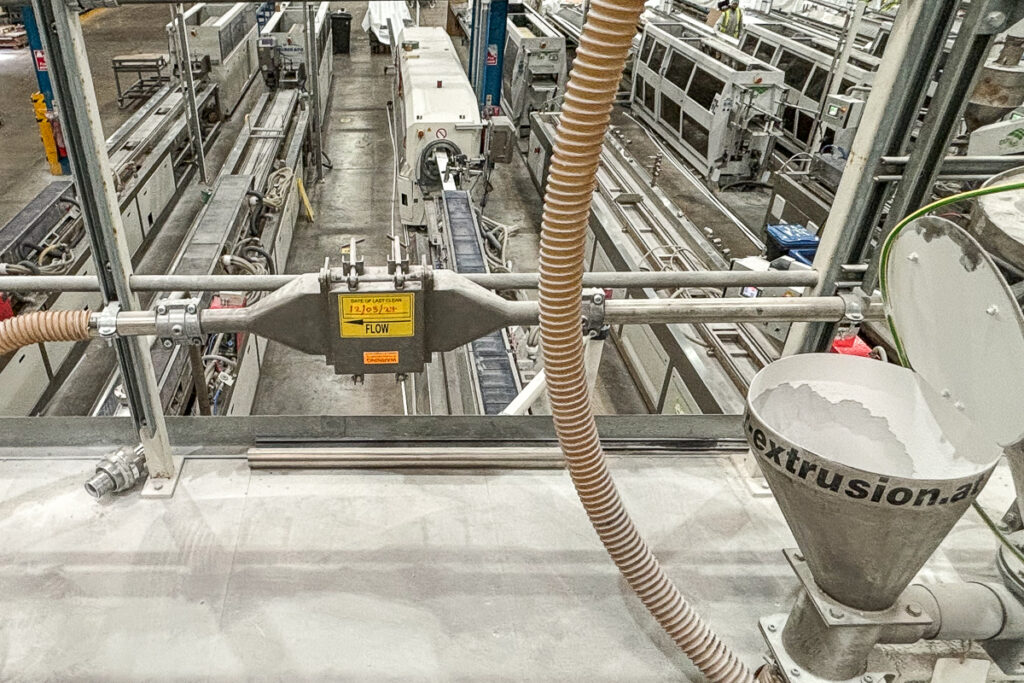
Using Recycled Plastic
In 2023, the Epwin Group, a UK based extruder and window fabricator, completed the first commercial installation of PVC-U windows manufactured from 98% recycled. This marked the beginning of a new era in PVC-U building product sustainability (British Plastics Federation).
The successful use of recycled plastic is reliant on the quality, with the removal of contaminants including metal. In this manufacturing plant, the Pneumatic Inline Magnets (PIMs) capture strong and weakly magnetic particles which may damage extruders and screens and reduce the quality of the recycled plastic feed.
The window frame manufacturer uses up to 40% recycled plastic in the feed for the frame substrate, with virgin plastic used for the outer coating to control the quality of finish and colour.
Mobile Pneumatic Inline Magnets
The two mobile Pneumatic Inline Magnets provide production flexibility. Mounted on a frame, the easily attachable and quick-release end connections enable the PIMs to be manoeuvred into critical positions, focusing on different batches of material which could be contaminated with ferrous metal.
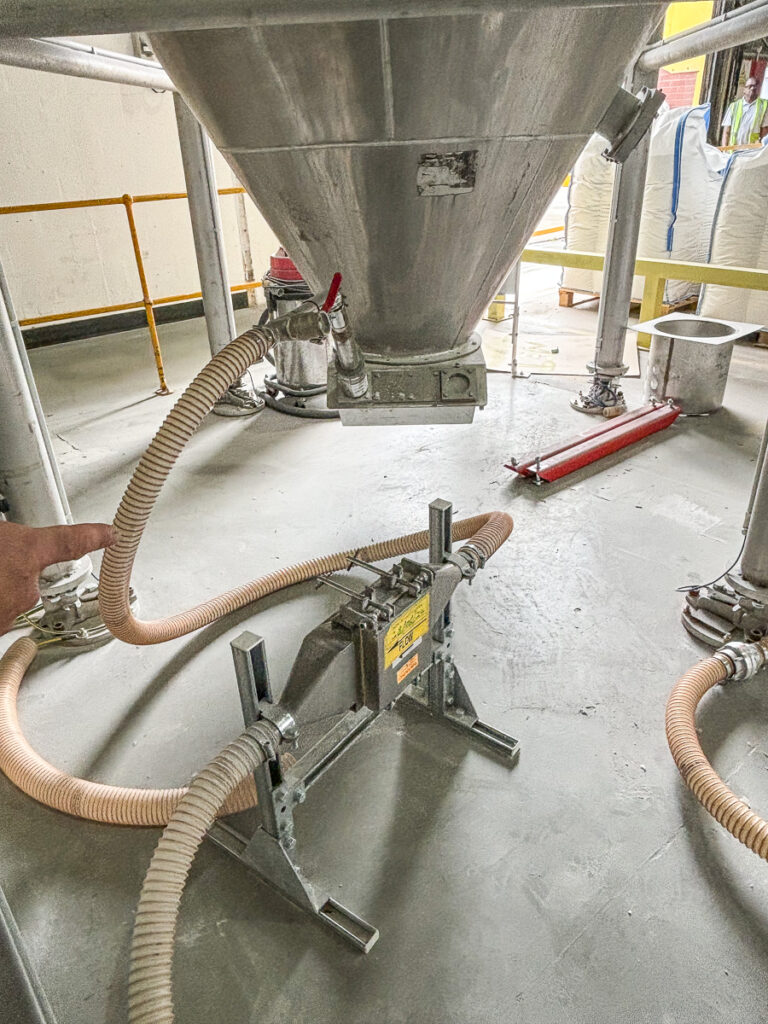
“The plastics industry is continually introducing new processes to increase the use of recycled plastic,” explained Peter Buckley, Bunting’s Technical Sales Engineer. “However, the successful use of recycled plastic relies on the material being free of contaminants such as metal. The Pneumatic Inline Magnets are a simple but effective way to capture ferrous metal and ensure that the recycled plastic flake is metal-free.”