High-Intensity Magnetic Separation at Ceramitec 2024
By Paul Fears | 28 March 2024
High-intensity magnetic separators reduce rejects, rework, and increase ceramic whiteness. On Bunting’s stand A6 323D at Ceramitec 2024 (9-12 April, Munich, Germany), ceramic engineers and ceramic mineral processors can find out about the latest high-intensity magnetic separation technology for both wet and dry processes.
Keeping Ceramic Glazes, Slips and Bodies Free of Magnetics
Fine iron and magnetic and para-magnetic minerals cause defects in ceramic products such as tableware, sanitaryware, tiles, and technical ceramics. The magnetic particles cause spotting and blemishes on the surface of the ceramic. Such magnetic contamination also causes internal structural defects that lead to cracking and breaking, and reduces the whiteness and brightness of white ceramic products such as sanitaryware and tableware.
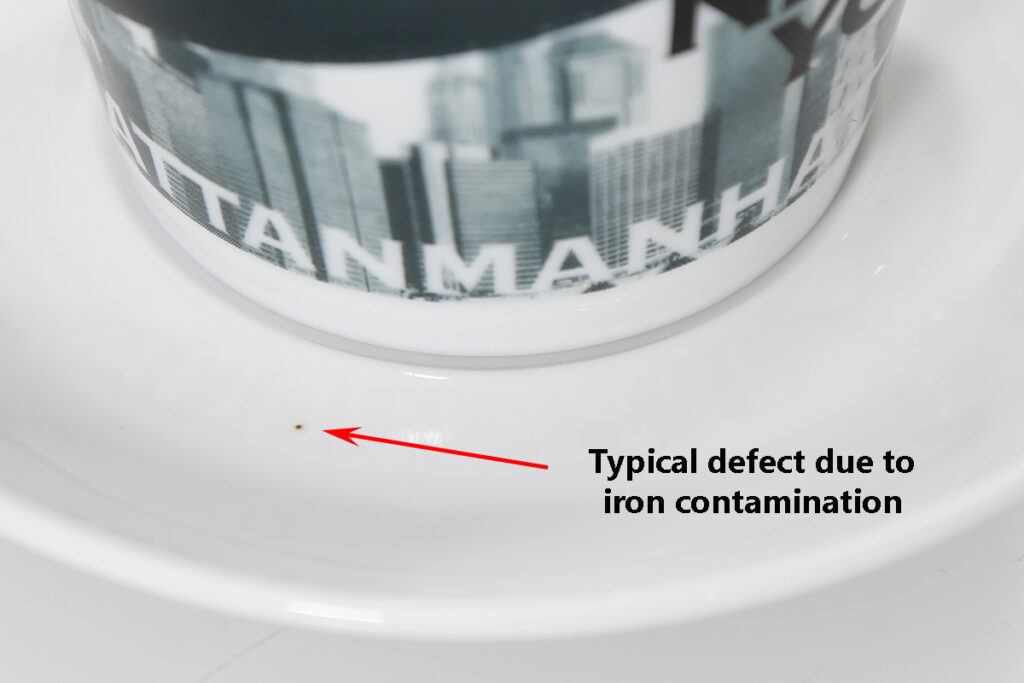
High-intensity magnetic separators capture the magnetic particles, removing them from the glaze, slip or body. Magnetic separators, in the form of Tube Magnets, Grate Magnets and Plate Magnets, utilise ultra-strong permanent neodymium rare earth magnets. Magnetic are held to the surface by strong magnetic forces.
However, the Electro Magnetic Filter further extends the magnetic intensity, generating a high magnetic force through oil-cooled electromagnetic coils. In operation, ceramic glaze, slip or body is fed up through a matrix of magnetic stainless-steel in the centre of the Electromagnetic Filter. The magnetic field is enhanced (up to 3 times) on the points of the matrix, enabling the capture of ultra-fine iron and paramagnetic minerals.
Ceramic Raw Material Purification
Non-metallic minerals used in the production of ceramics, such as feldspar and silica sand, contain varying levels of strong and weak magnetic minerals. Once mined and quarried, the mineral processor will mill and purify the non-metallic mineral to meet a customer’s specification.
The extraction and then dry processing of these complex non-metallic mineral deposits requires additional levels of processing and purification, including the use of high-intensity magnetic separators including Rare Earth Roll Magnetic Separators, Induced Magnetic Rolls and Rare Earth Drum Magnets.
High intensity magnetic separators in Bunting’s Customer Experience Centre
Bunting’s mineral processing engineers work with minerals companies from the feasibility stage right through to production plant optimisation. Minerals tested at Bunting’s Customer Experience Centre in the UK confirm what level of separation is possible with any particular magnetic separator.
- Find out more about conducting tests at Bunting’s Customer Experience Centre
Working within Ceramics for 50 years
“Our experienced applications engineers have been visiting European ceramic plants for over 50 years,” explained Bradley Greenwood, Bunting’s European Sales Manager. “Ceramitec provides us with the ideal platform to meet both existing and new clients and help address issues relating to iron contamination and magnetic minerals.”
On Bunting’s stand A6 323D will be Stefano Maiaroli, Bunting’s Sales Area Manager covering Southern Europe, and Marcel Graef from 3SMI, Bunting’s representative in Germany.
Related Technical Articles
- Keeping Ceramic Tableware Iron Blemish Free
- Keeping Ceramic Sanitaryware Iron Free
- Keeping Ceramic Tiles Iron Free
Optimum Magnetic Separation Reduces Rejects
Understanding the ceramic manufacturing process is important when making recommendations for the optimum magnetic separation equipment. However, each manufacturing process is unique and a visit by a local Bunting Sales Engineer will help understand a specific process and iron contamination issue and propose a specific solution.
For additional information on eradicating iron contamination in ceramic tableware, tiles, sanitaryware, or technical ceramics, please contact us by completing the form below.