High-Intensity Magnetic Separators at Ceramitec
By Paul Fears | 20 June 2022
High-intensity magnetic separators play a key role in the manufacture of ceramics and the processing of ceramic raw materials, as highlighted at Ceramitec 2022 on Bunting’s stand (on stand C1:511).
Keeping Ceramics Iron-Free
Fine iron and magnetic minerals cause defects in any ceramic product, whether that is tableware, sanitaryware, tiles or technical ceramics. The iron causes spotting and blemishes on the surface if left unremoved from the liquid glaze. Such magnetic contamination also causes internal structural defects that lead to cracking and breaking.
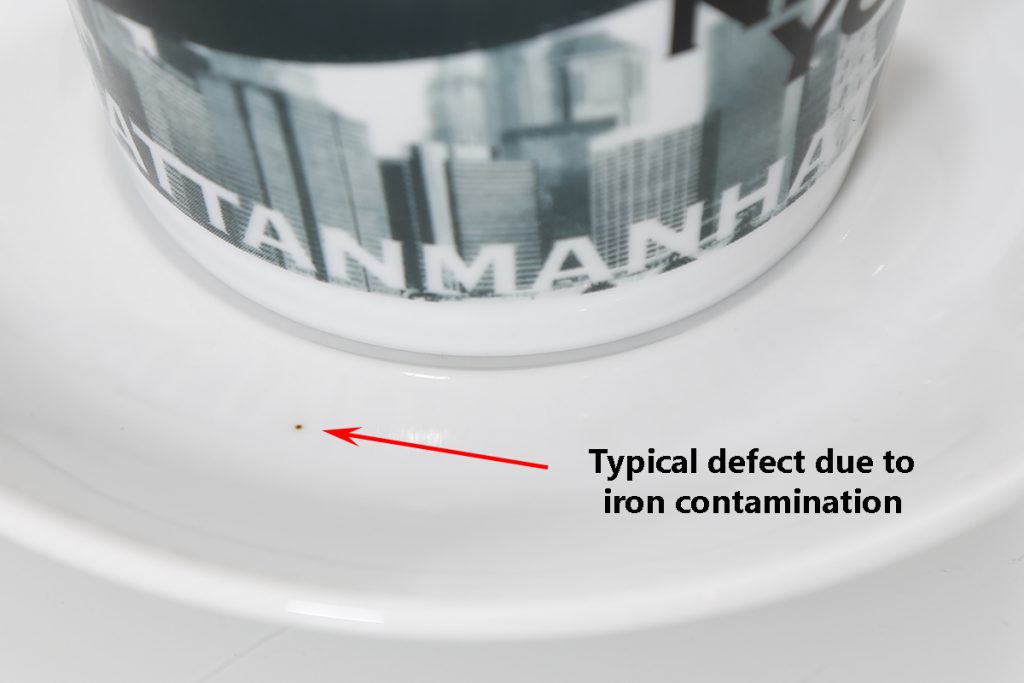
High-intensity magnetic separators capture the magnetic particles, removing them from the glaze, slip or body. Magnetic separators, in the form of Tube Magnets, Grate Magnets and Plate Magnets, utilise ultra-strong permanent neodymium rare earth magnets. Magnetic are held to the surface by strong magnetic forces.
The Electromagnetic Filter further extends the magnetic intensity, generating the high magnetic force through oil-cooled electromagnetic coils. In operation, ceramic glaze, slip or body is fed up through a matrix of magnetic stainless-steel in the centre of the Electromagnetic Filter. Fine and weakly magnetic particles are attracted to and held on the points in the matrix, removing them from the ceramic slurry.
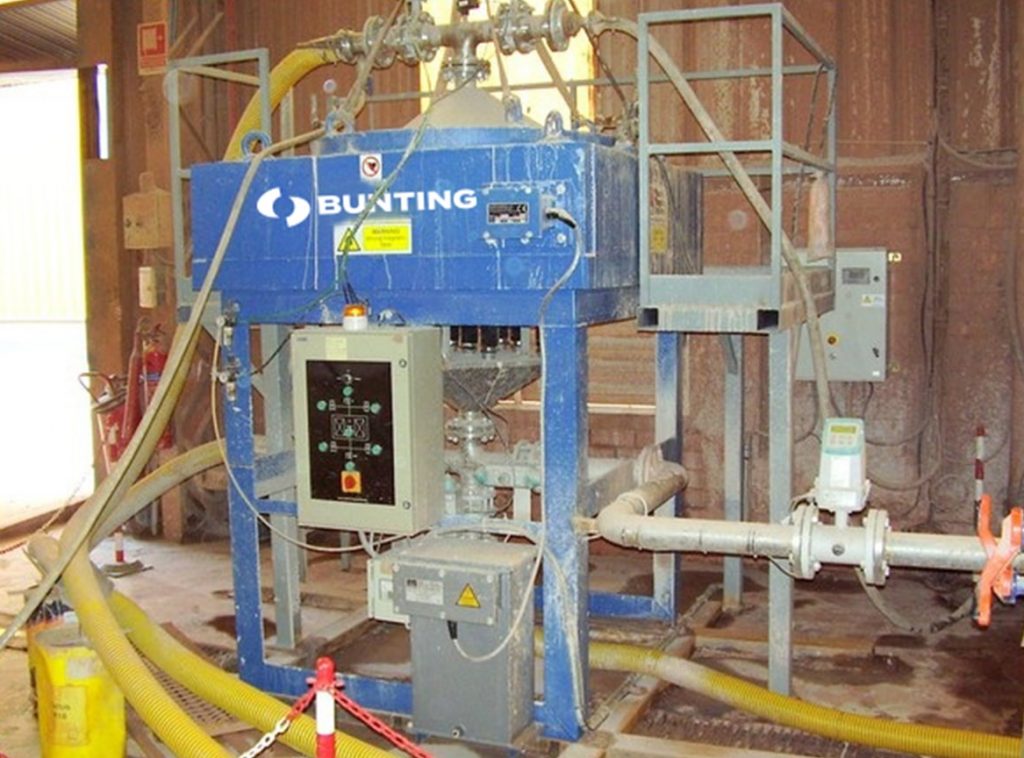
Ceramic Raw Material Purification
Non-metallic minerals used in the production of ceramics, such as feldspar and silica sand, commonly contain varying levels of strong and weak magnetic minerals. Once mined and quarried, the mineral processor will mill and purify the non-metallic mineral to meet a customer’s specification.
Europe has always been a global leader in the production of non-metallic minerals, although many of the higher quality reserves have already been mined. The extraction and processing of more complex deposits often requires additional levels of processing and purification, including the use of high-intensity magnetic separators including Rare Earth Roll Magnetic Separators, Induced Magnetic Rolls and Rare Earth Drum Magnets.
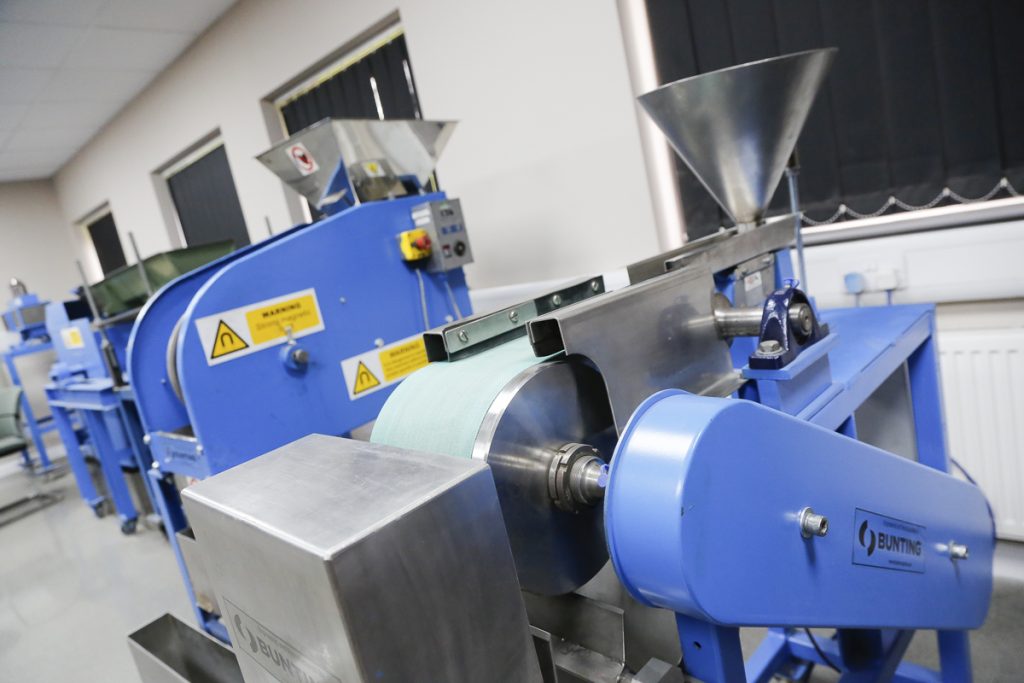
Bunting’ mineral processing engineers work with mining companies from the feasibility stage right through to production plant optimisation. Mineral processors have materials tested at Bunting’s Customer Experience Centre in the UK to prove what level of separation is possible with any particular magnetic separator.
Working within Ceramics for 50 years
“We have worked with ceramics manufacturers and ceramic raw material processors for over 50 years,” explained Adrian Coleman, the General Manager of Bunting-Redditch. “Although there have been advances in the manufacturing techniques and high-intensity magnetic separation, the basic need to remove free iron and magnetic minerals remains.
“By installing the right magnetic separator in the correct location, we have helped significantly reduce rejects in ceramic production. We have also worked with ceramics companies to help recycle the waste, recovering valuable raw materials whilst reducing the amount of material lost to waste.
“Ceramitec provides us with the ideal platform to meet both existing and new clients and help address issues relating to iron contamination and magnetic minerals.”
Related Technical Articles
- Keeping Ceramic Tableware Iron Blemish Free
- Keeping Ceramic Sanitaryware Iron Free
- Keeping Ceramic Tiles Iron Free
Optimum Magnetic Separation Reduces Rejects
Understanding the ceramic manufacturing process is important when making recommendations for the optimum magnetic separation equipment. However, each manufacturing process is unique and a visit by a local Bunting Sales Engineer will help understand a specific process and iron contamination issue and propose a specific solution.
For additional information on eradicating iron contamination in ceramic tableware, tiles, sanitaryware, or technical ceramics, please contact us on:
Email: Gordon Kerr at GKerr@buntingmagnetics.com
Telephone: +44 (0) 1527 65858
Follow us on social media