BMRA’s Young British Metal Recyclers Visit Bunting
By Paul Fears | 28 February 2022
The British Metals Recycling Association (BMRA) arranged for their Young British Metal Recyclers group to visit Bunting’s Customer Experience Centre in Redditch, UK and see the latest in metal separation technology. The British Metals Recycling Association represents the £7 billion UK Metal Recycling sector.
Located at the material testing facility in Redditch is a range of laboratory-scale high-intensity magnetic separators, eddy current separators and electrostatic separators. Recycling companies from around the world send samples to Redditch for testing and Bunting’s laboratory team conduct tests to determine the separation performance in terms of recovery and purity.
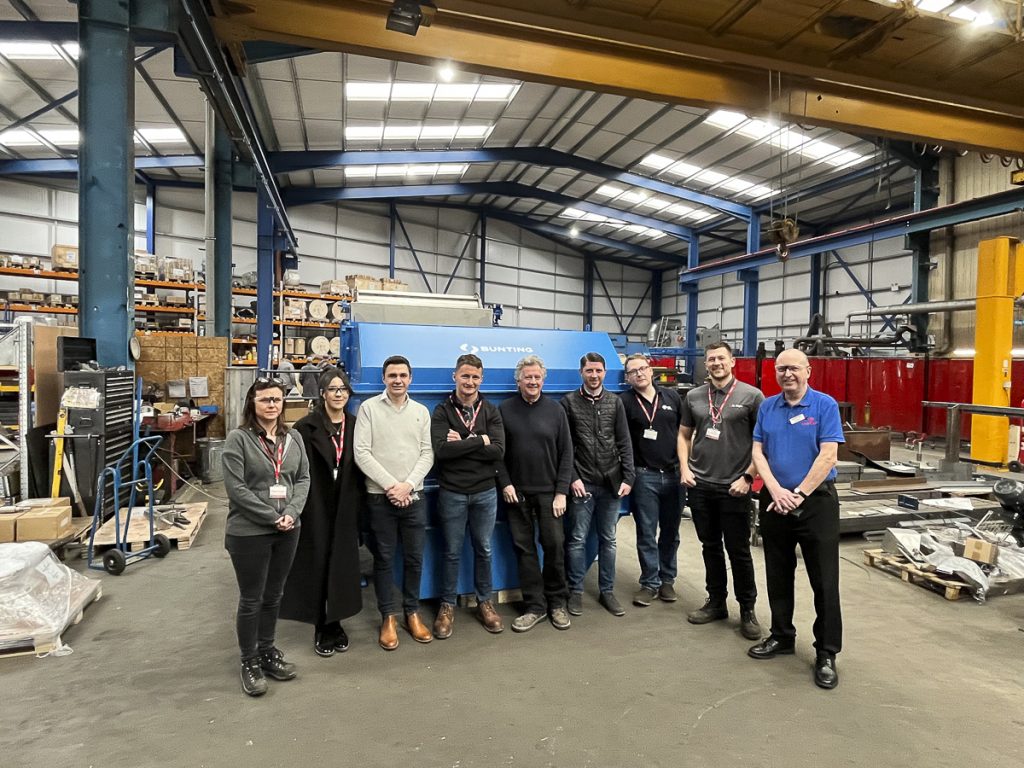
Demonstrating Separation Possibilities
Bunting’s Customer Experience Centre is split into two areas. The Recycling Test Facility focuses on coarser material separation with equipment including the Eddy Current Separator, Stainless Steel Magnetic Separators (HISC and SSSC). More delicate material tests, including mineral separation, take place in the Test Laboratory.
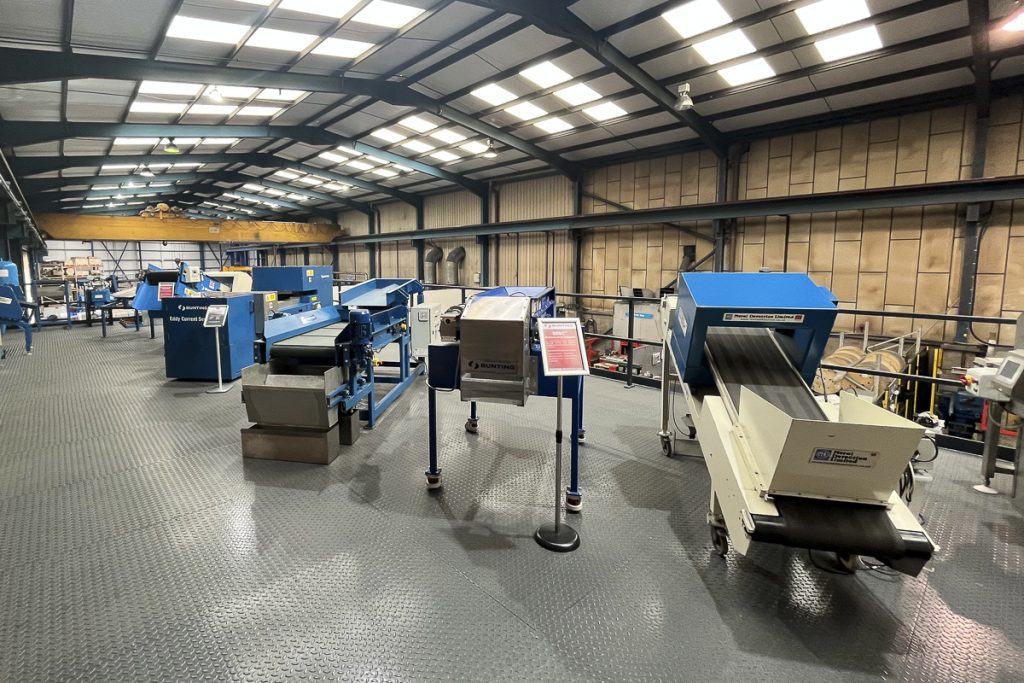
Bunting’s team providing the group with training and demonstrating the equipment included Neil Rowson, Phil Tree, Joe Cetti, Tom Higginbottom and Alison Flower.
There were a wide range of demonstrations and discussions on different types of metal separators. The demonstrations included:
- Non-ferrous metal separation on the Eddy Current Separator;
- The separation of weakly magnetic, fragmented stainless-steel on the HISC;
- Beach sands separation on the high-intensity Magnetic Disc Separator;
- Separating ferrous and weakly magnetic stainless-steel from a metal mix including copper and brass using a Rare Earth Roll Magnetic Separator;
- Using a Drum Magnet to separate batteries;
- ElectroStatic separation of fine metals such as copper when processing granulated cables;
- The increasing use of Metal Detectors in recycling;
Manufacturing in Action
Whilst at Redditch, the Young British Metal Recyclers took the opportunity to see manufacturing in action. The Redditch manufacturing was recently expanded by 50% in response to the growing demand for metal separation equipment.
Bunting manufactures hundreds of Permanent Overband every year and the group was shown the charging of magnet blocks and the assembly of complete separators. In 2021, Bunting manufactured a record number of Eddy Current Separators, with the high demand continuing into 2022. During the visit, the group saw highly skilled and experienced fabricators building eddy current separator rotors.

It was also fortuitous that a large, 2-metre-wide Metal Separation Module (including Drum Magnet and Eddy Current Separator) was in the final stages of construction on the shop floor. This enabled the group to see the evolution of a project that started with testing and resulted in the manufacture of a production-sized separator.
Seeing Is Believing
“You can read about technology and even watch videos on YouTube, but there is nothing better than being present to see a separation demonstration,” explained Phil Tree, Sales Manager of Bunting-Redditch. “At our Customer Experience Centre, we work alongside customers to achieve a specific separation objective. With the BMRA’s Young British Metal Recyclers group, we would demonstrate the capabilities of a metal separator and then discuss specific applications. This is another example of the importance of equipment manufacturers working hand-in-hand with recyclers.”
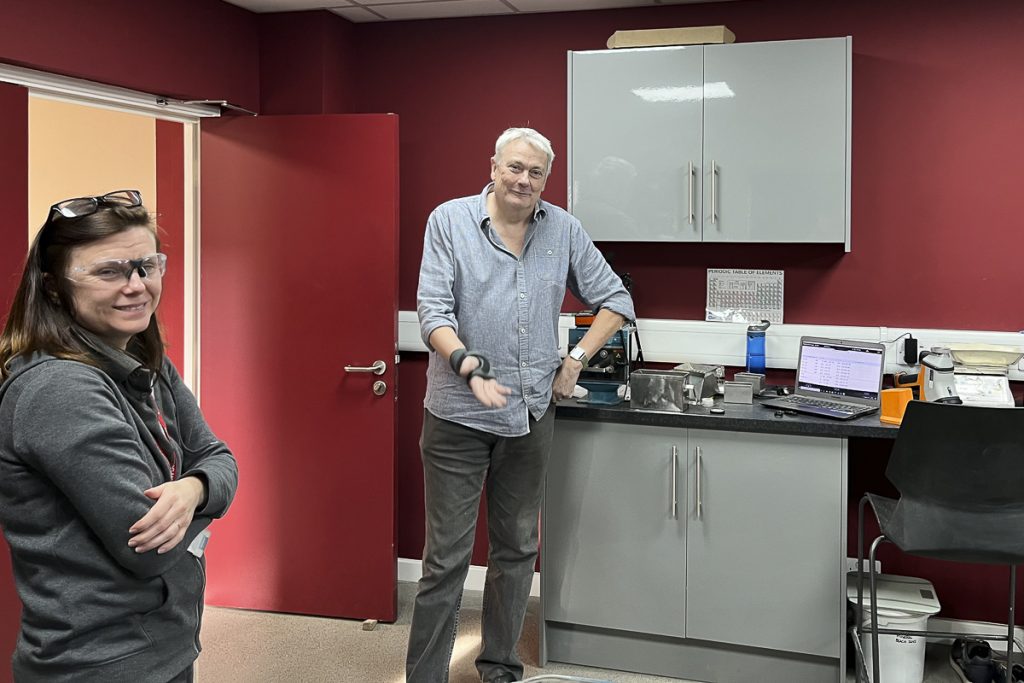
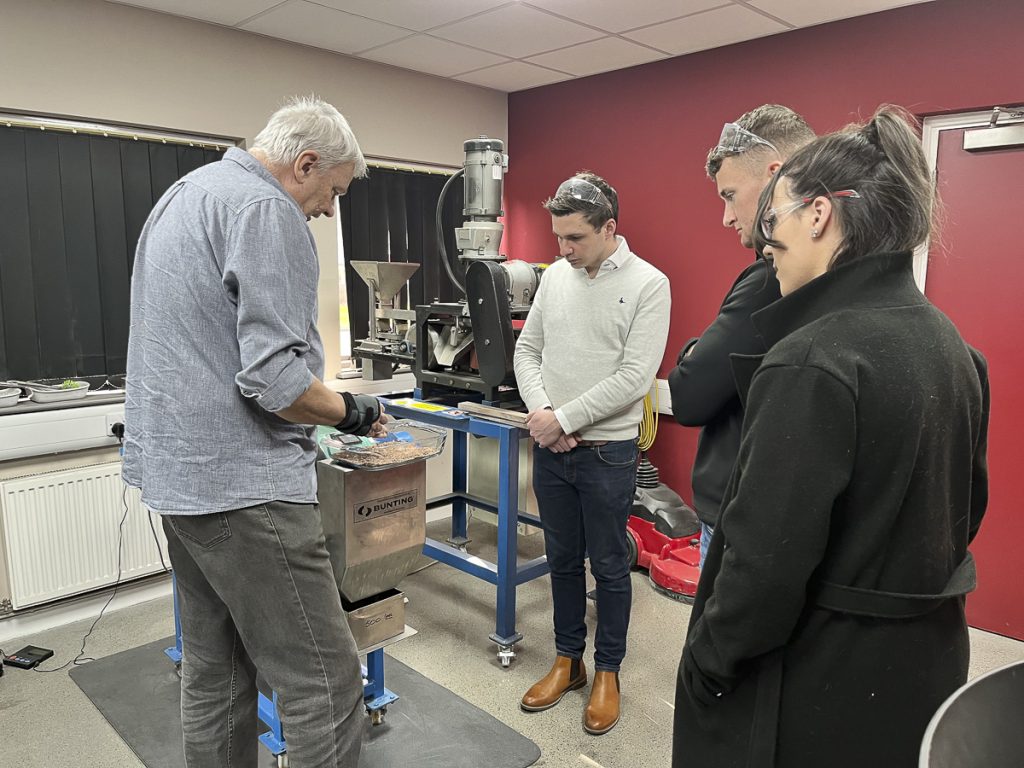
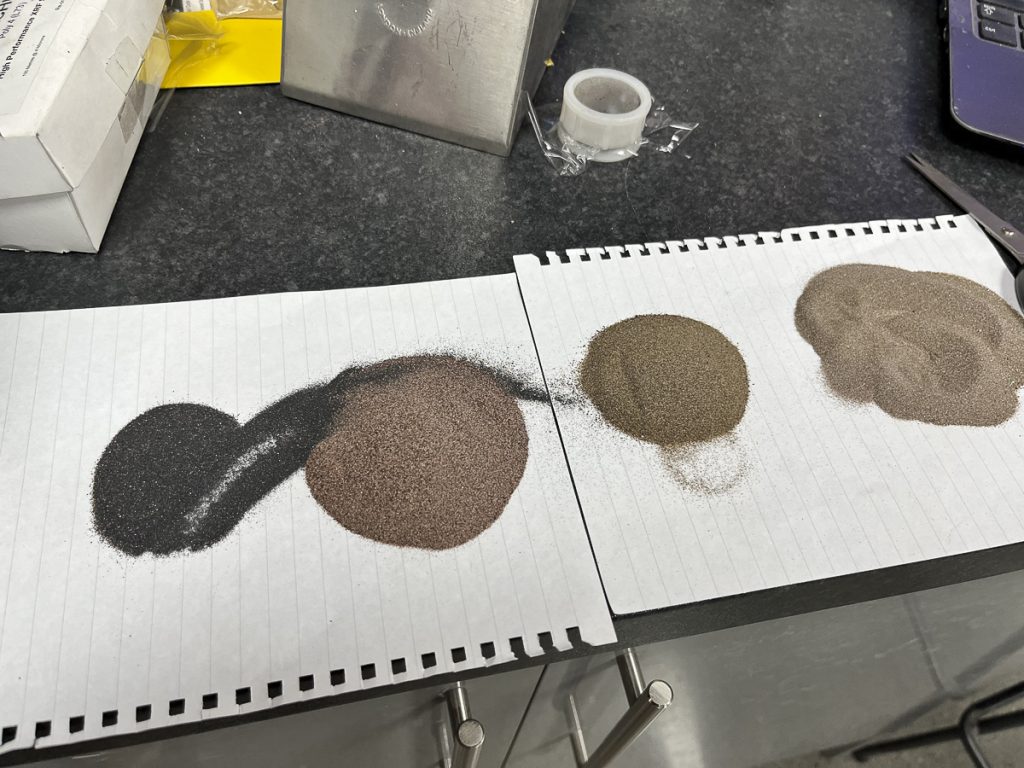
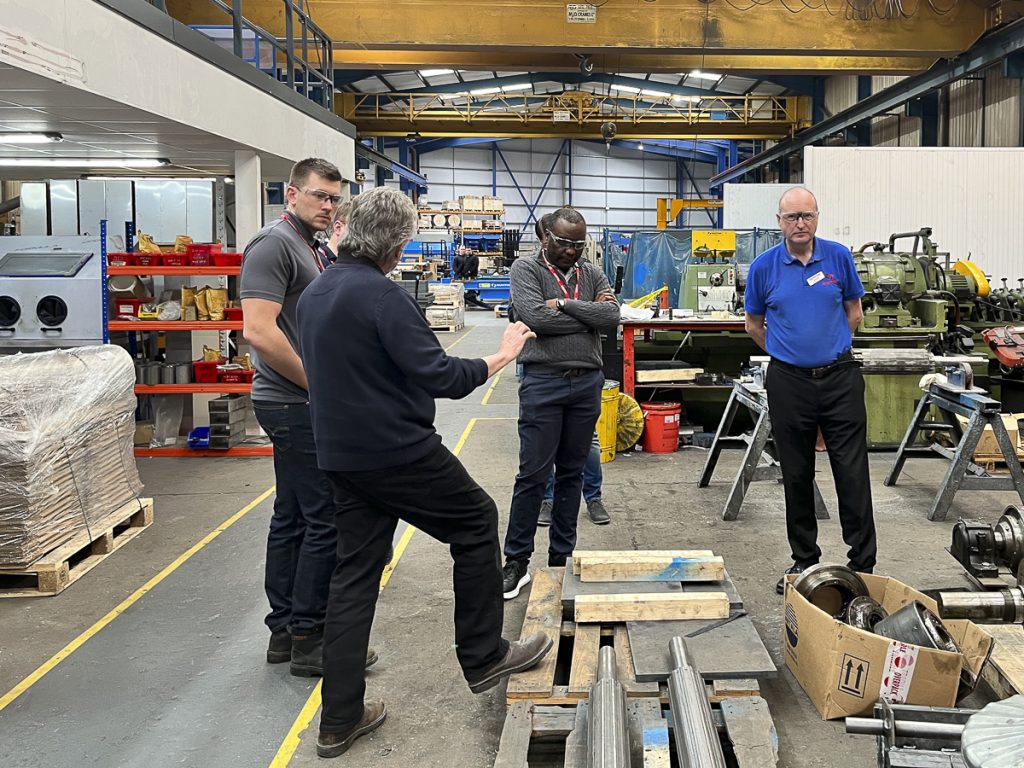
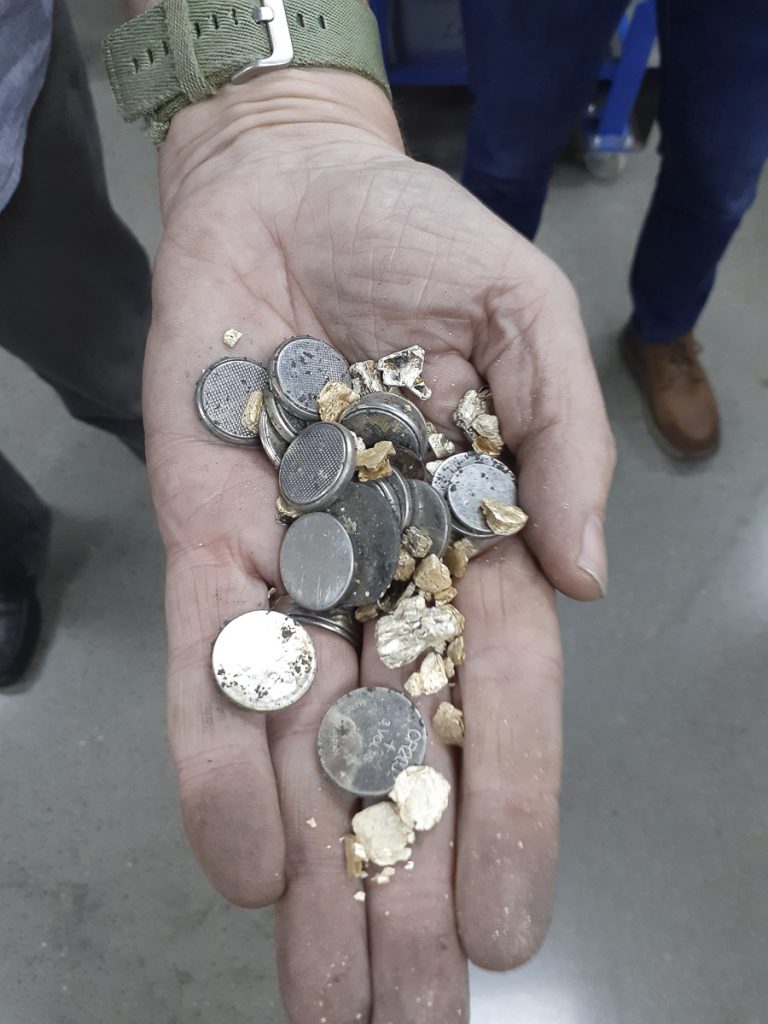
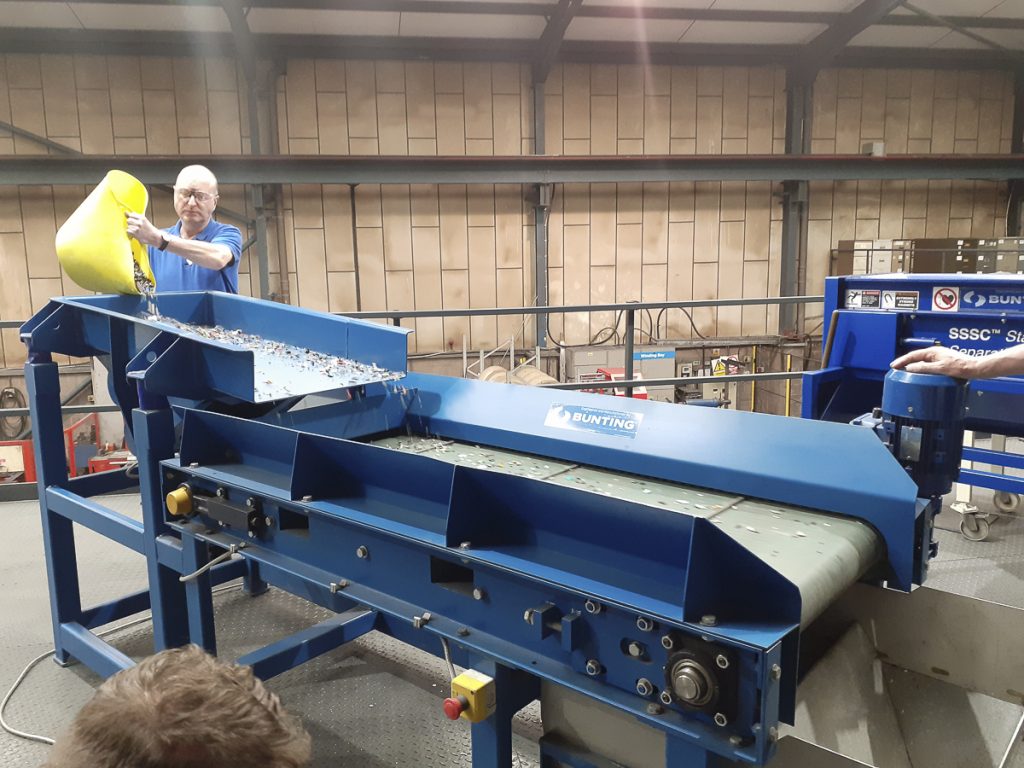
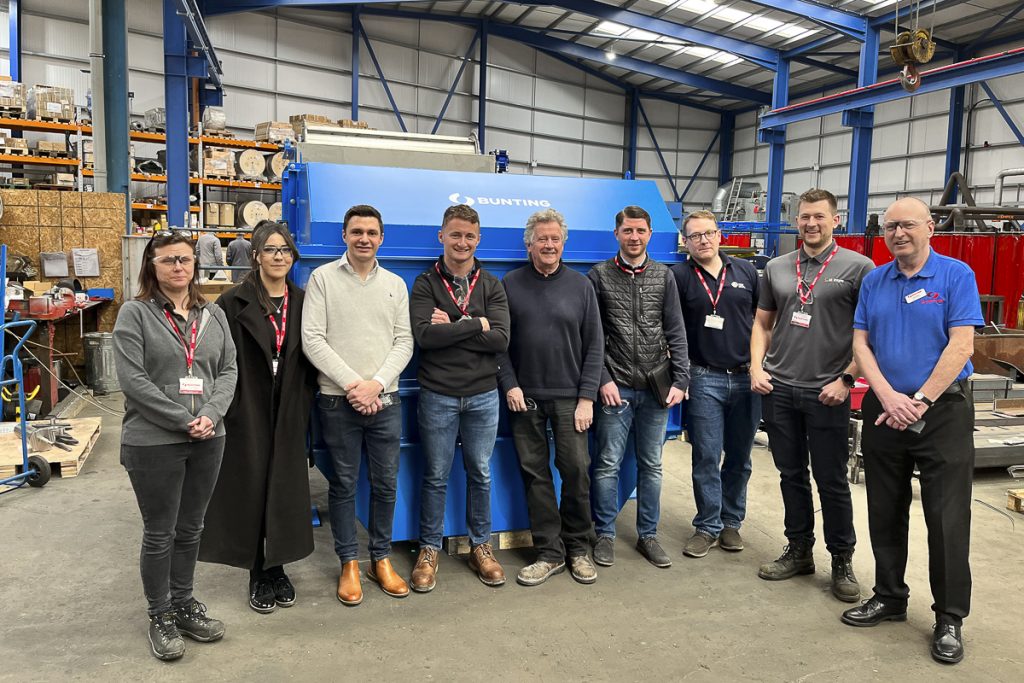
Related Recycling Articles
For further information on Magnetic Separators, Eddy Current Separators, and ElectroStatic Separators for metal recovery in recycling applications or to discuss a specific project including undertaking tests in our Customer Experience Centre, please contact our technical sales team on:
Email: Gordon Kerr at GKerr@buntingmagnetics.com
Telephone: +44 (0) 1527 65858
Follow us on social media