Training Future Metal Recyclers from EMR
By Paul Fears | 14 September 2021
Students, on a year’s work placement with European Metal Recycling (EMR), attended a training day at Bunting’s Redditch plant assessing the latest magnetic, eddy current and electrostatic separators. The training illustrated the importance of optimising material separation in the drive towards increasing secondary material recycling rates.
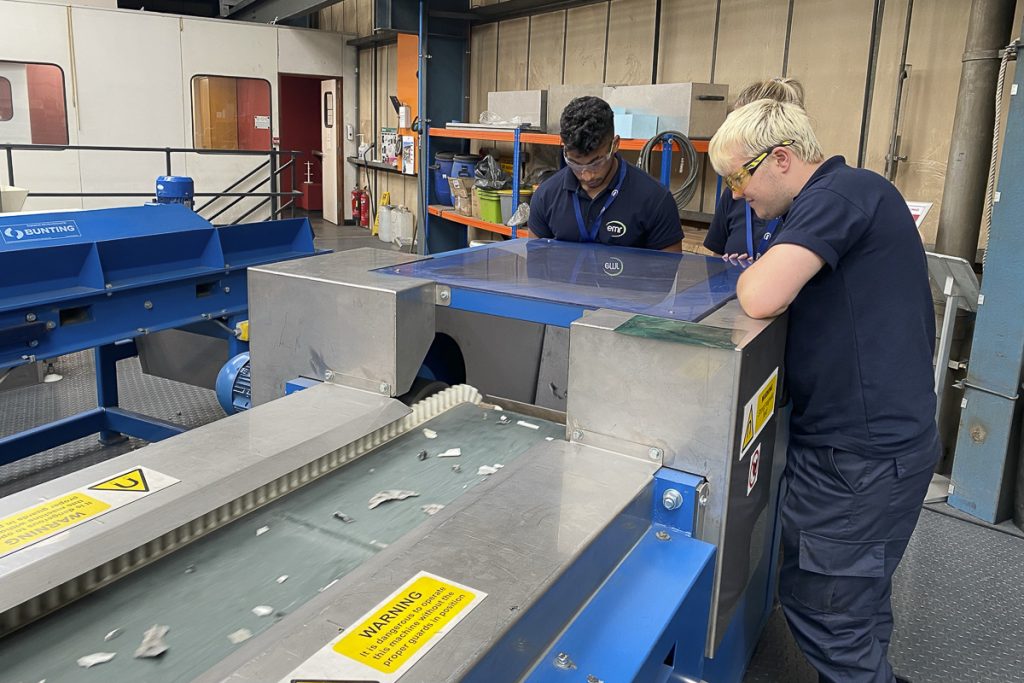
EMR is a global leader in sustainable materials, investing in cutting-edge technology, world-class research and a dedicated team of recycling experts. With facilities across the globe and a team of over 3,000 people, EMR’s operations put 10 million tonnes of material back into the supply chain annually.
The six (6) students were from Universities across the UK including Birmingham, Aston, Leeds and Harper Adams studying chemical and mechanical engineering. The students are in the 3rd year of a 4 year course, returning for their final year in September 2022.
Seeing Is Believing
Bunting’s Laboratory Manager, Neil Rowson and Sales Manager, Phil Tree demonstrated a wide range of separation technology used in the recycling and mineral processing sectors. Neil Rowson has over 35 years of experience in material separation, including a professorship of Chemical Engineering at the University of Birmingham. Over the past 40 years, Phil Tree has helped companies solve material separation problems with a wide range of magnetic technology.
The training session was held in the new state-of-the-art Customer Experience Centre at Bunting’s recently extended manufacturing facility in Redditch, UK.
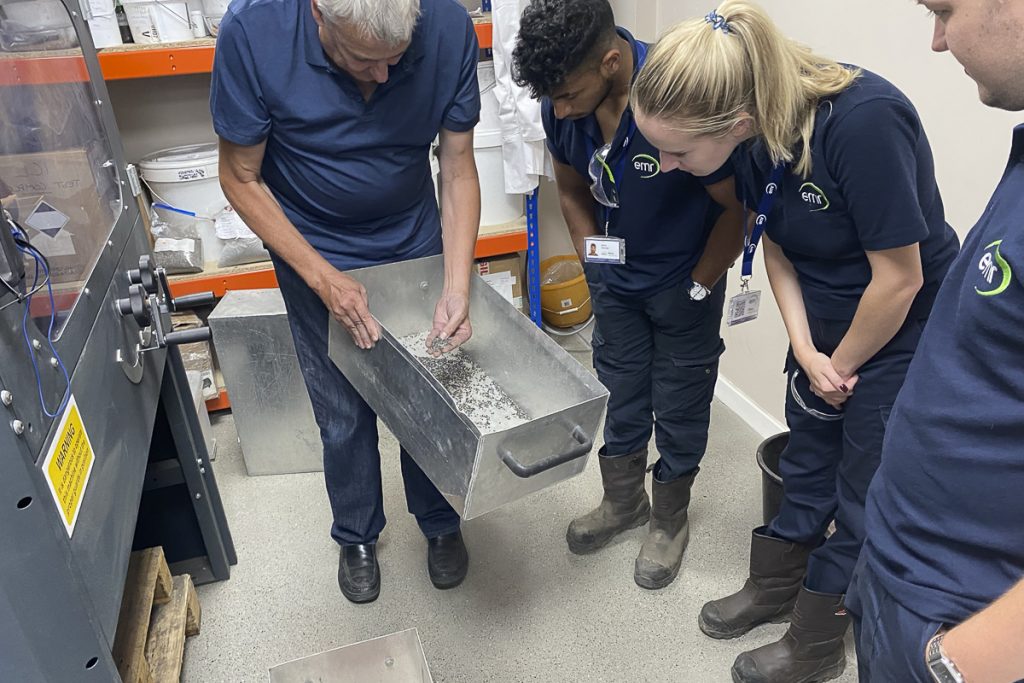
The training session started with a presentation on the physical separation of primary and secondary materials. This included an assessment of different types of physical separation technology presently available.
After a tour of the Redditch manufacturing facility, the training focused on practical demonstrations in the minerals and recycling testing facilities. This included:
- Illustrating techniques used to measure magnetic fields;
- Material sampling techniques and using a Hitachi Handheld XRF analyser to assess a materials composition both before and after separation;
- Using a high-intensity Magnetic Disc Separator to separate minerals of differing magnetic susceptibility. This technology is commonly used to process Coltan (used in the manufacture of technology such as mobile phones) and beach sands;
- Purification of crushed granite by removing biotite mica contamination on a high-intensity Rare Earth Roll Magnetic Separator;
- Coltan separation in a slurry state on a high-intensity wet magnetic separator (WHIMS);
- Separating fine shredded copper cable on Bunting’s ground-breaking ElectroStatic Separator;
- With ultra-high magnetic fields, separating fragmented stainless-steel on the patented SSSC Magnetic Separator;
- Recovering valuable non-ferrous metals using one of Bunting’s range of high-strength Eddy Current Separators;
The final discussion of the day focused on Electric Vehicles and the challenges of recycling both rare earth magnets and Li-ion batteries.
- Technical article: Metal Recovery from Electric Vehicles
“There has never been a greater focus on the recovery and reuse of secondary materials,” explained Neil Rowson. “Separation technology, both existing and new, play a vital role in our ability to reduce waste. EMR wanted the students to gain a greater understanding of material separation focusing on magnetic, eddy current and electrostatic technology.”
Related Recycling Articles
For further information on Magnetic Separators, Eddy Current Separators, and ElectroStatic Separators for metal recovery in recycling applications or to discuss a specific project including undertaking tests in our Customer Experience Centre, please contact our technical sales team on:
Email: Gordon Kerr at GKerr@buntingmagnetics.com
Telephone: +44 (0) 1527 65858
Follow us on social media