Metal Removal when Recycling Rubber Tyres
By Paul Fears | 27 March 2020
Successfully removing metal from rubber (originating from the metal wire in a tyre) when recycling tyres is critical, especially as rogue metal can cause injury to horses and children who run and play on the recovered rubber crumb. Although each tyre recycling plant is different, here is a guide to the common types and location of Magnetic Separators to remove the steel.
The biggest challenge with removing all the steel wire from shredded tyres is to maximise separation whilst minimising product (rubber) loss. This means that multi-stage Magnetic Separation is required.
As shown in the typical plant layout, the primary objective is to liberate the rubber from the metal and this is commonly achieved with a 2-stage shredding set-up. This achieves optimum size reduction whilst also producing a rubber crumb material that is well liberated. After the 2nd stage of shredding, it is then possible to focus on the separation of the steel.
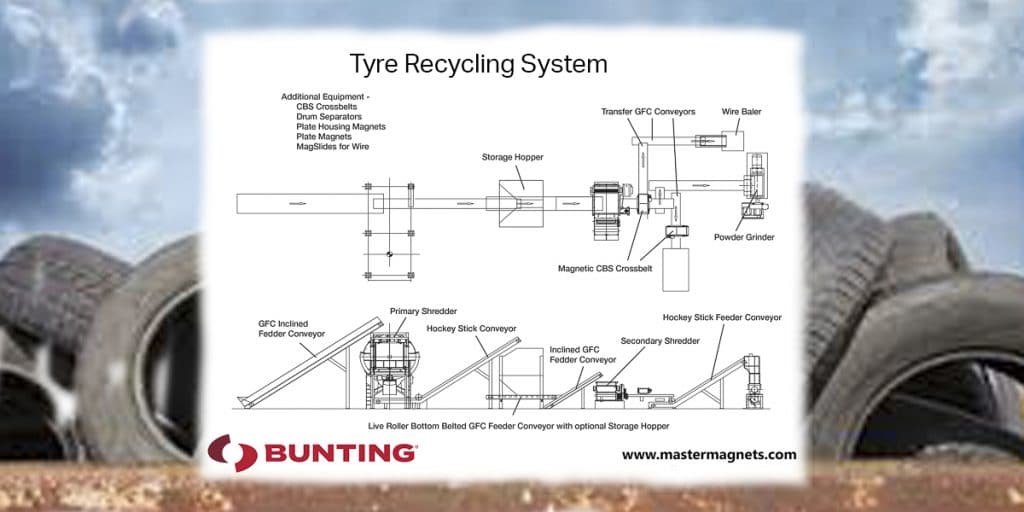
Step 1 – Primary Magnetic Separation after the 2nd Shredder
At this stage, the objective is to separate the bulk of metal and this is achieved using a high strength Overband Magnet. The Overband Magnet is suspended across the conveyor and attracts, lifts and removes metal from the conveyed rubber. There are various designs of Overband Magnet, both electro and permanent, and the optimum design for this application is a design with multiple poles.
Step 2 – Magnetic Separator Treatment of the Separated Metal Fraction
As there will be clean rubber product carried over into the separated metal fraction, the material can be passed over a rotary design of high-strength Magnetic Separator. These include:
All using high strength Rare Earth Magnets. It is important that the design of the Magnetic Separator features an Axial magnetic field (one that runs along across the width of the Magnetic Separator) as this causes the material to tumble and release entrapped rubber.
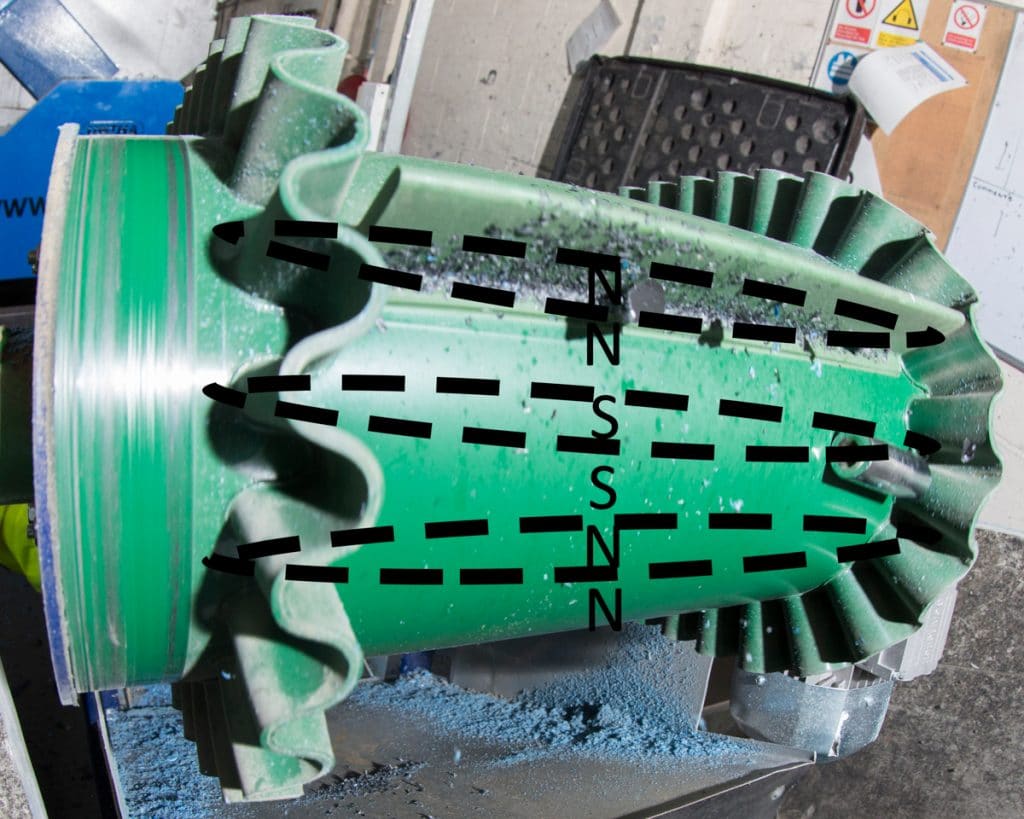
If a Drum Magnet is used, then consideration is needed for either a manganese steel shell or wear cover as the strong magnetic characteristics of the steel wear can result in heavy wear.
A recent development is the use of a Stainless Steel Separator. The conveyor design feeds rubber crumb into the high magnetic field of the head roll, where separation occurs.
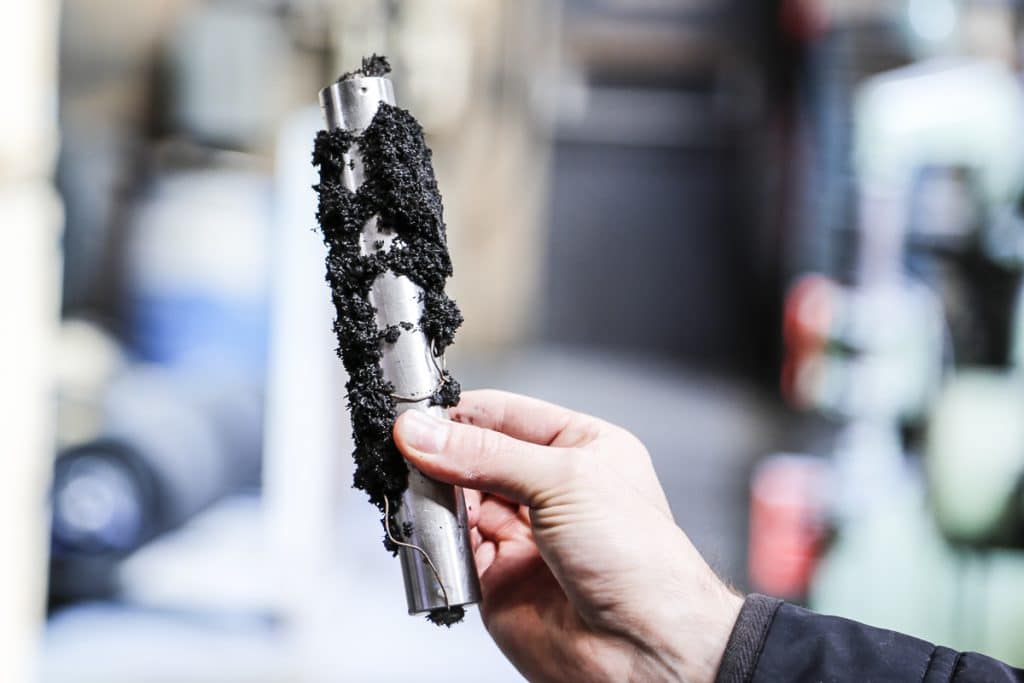
Step 3 – Secondary Magnetic Separation
As a clean metal-free rubber product is vital, a second-stage Magnetic Separation is recommended. This removes any stubborn metal left after the first stage separation. The most commonly-used Magnetic Separators include:
Step 4 – Magnetic Treatment of the Rubber Powder
For fine rubber material, that is fed onto a powder grinder, a final stage Magnetic Separator is needed to remove smaller fragments of wire. As the volume of metal is low, a manual-clean Plate Magnet suspended close to the product over the conveyor will lift and remove the fine wires;
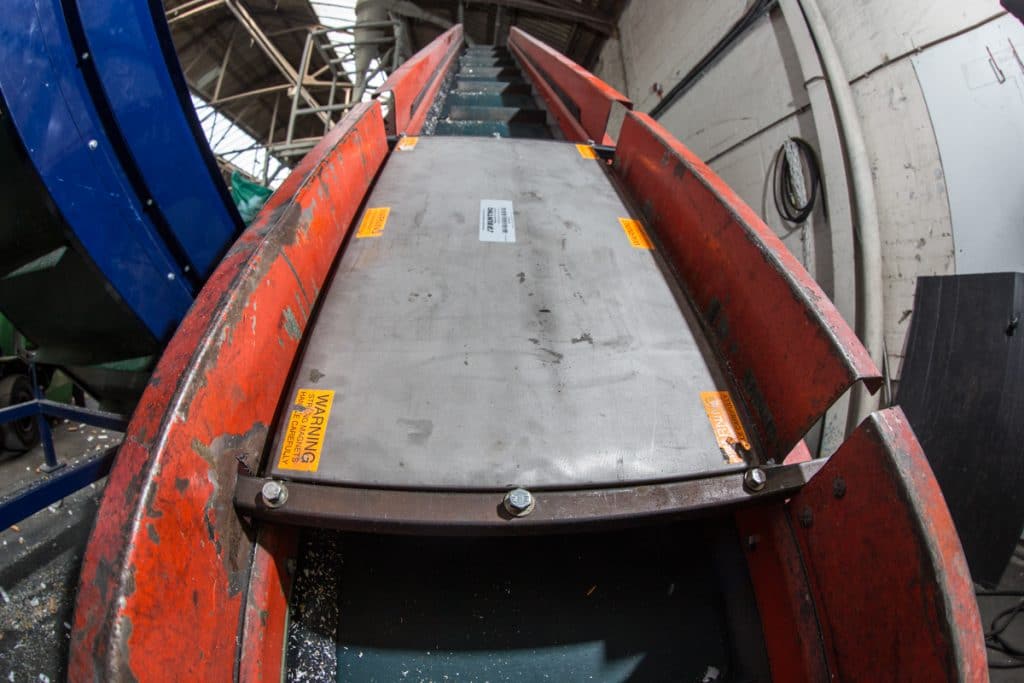
Maximising Metal Separation
The four-steps outlined are based upon work Bunting has conducted with tyre recyclers around the world, but each plant is often unique. When considering metal separation, either from the start or to improve on the level of metal separation presently being achieved, a review of the plant by one of the Bunting Application Engineers will enable the recommendation of the optimum design and location of a Magnetic Separator.
For additional information on equipment used to separate and recover metals, please contact us on:
Email: Gordon Kerr: GKerr@buntingmagnetics.com
Telephone: +44 (0) 1527 65858
Follow us on social media