Eddy Current Separator Magnetic Poles
By Paul Fears | 10 December 2018
2nd of 5 Technical Articles:
Reviewing Eddy Current Separator Performance
More is always better. Or is it? In the second of our technical articles reviewing the design of Eddy Current Separators, we look at the importance of the number of magnetic poles. Does a magnetic rotor with 42 magnetic poles enable a better separation than 22 poles?
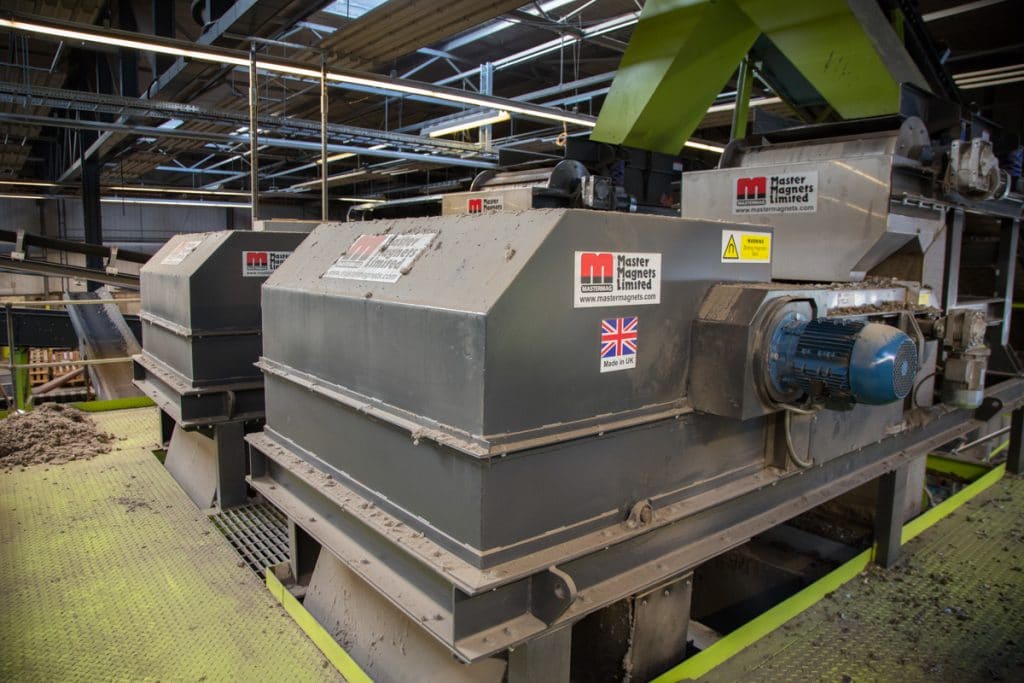
Eddy Current Separators operating at Recycling Lives
The Theory
The magnetic rotor of any Eddy Current Separator comprises of rows of magnets. These magnets, usually Neodymium Rare Earth, are fixed in such a way to produce a projected magnetic field of differing polarity. The actual separation of non-ferrous metals on an Eddy Current Separator is based on Fleming’s Left Hand Rule. When a non-ferrous metal is placed in the rotating and changing magnetic polarity of a magnetic rotor, a current is generated inside the particle. This current produces it’s own magnetic field, which then reacts against the magnetic field of the rotating rotor. This causes the non-ferrous metal particle to repel. This repulsion enables a separation. In operation, the repulsive action causes the non-ferrous metal particle to spin and lift.
This theory would suggest that the greater number of different magnetic poles passing through a non-ferrous metal particle would produce a better separation effect. This is a result of the rotor speed (discussed in our first technical article – Eddy Current Separator Rotor Speed) and the number of magnets (and therefore magnetic poles) on the rotor.
The Eddy Current Separator
The Magnetic Rotor of an Eddy Current Separator is positioned inside a non-metallic shell at the head of a two-pulley belt conveyor. Material is conveyed on the belt into the magnetic field. As the non-ferrous metal enters the rotating magnetic field, it reacts and is propelled away from the belt. A strategically placed splitter enables the segregation and collection of the non-ferrous metals away from the non-metallic materials.
Magnetic Poles on a Magnetic Rotor
As with any engineered design, there are several factors to consider other than just theory. As shown in diagram 1, the magnets on the rotor interact to project a magnetic field. Within reason, any number of magnets can be used to build an Eddy Current Separator rotor. The number of resultant magnetic poles is a function of the quantity of magnets. More magnetic poles can be created by using smaller magnets.
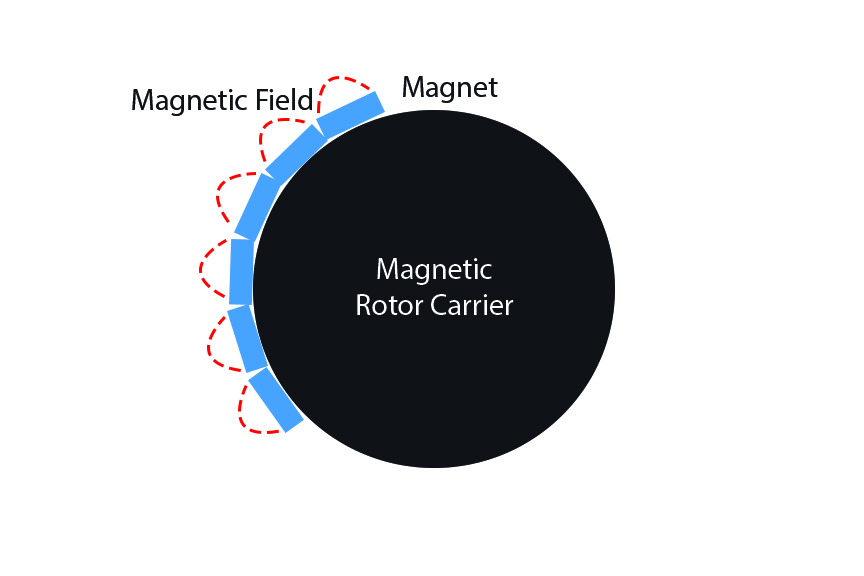
Diagram 1 – Magnets and Magnetic Field of an Eddy Current Separator Rotor
However, the size of the magnet also dictates the throw or projection of the magnetic field. Smaller magnets produce a shallower magnetic field, which could prove problematic. The magnetic rotor is mounted and rotates independently inside a slower moving non-metallic shell. Also, a conveyor belt sits on top of the shell. Therefore, the magnetic field has to project quite a distance before it reaches a non-ferrous metal on the surface of the belt (Diagram 2).
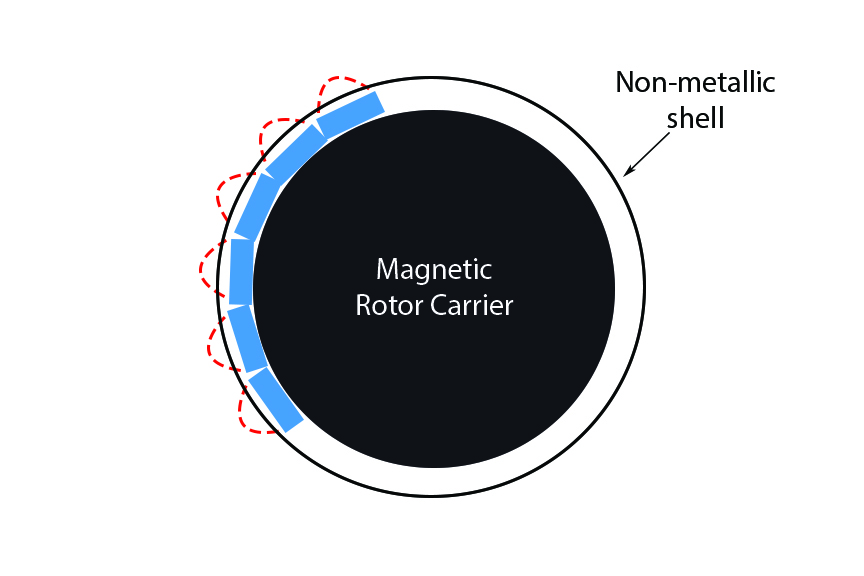
Diagram 2 – Effect of the Non-Metallic Shell
If the magnetic field is too shallow, possibly because there are a high number of smaller magnets, it may not project enough repulsive energy to cause a repulsion and separation. Thicker magnets may help, but the length of the magnet has a greater influence.
Optimum Number of Magnetic Poles
The optimum number of magnetic poles is commonly determined by the separation objective:
- Separation of Larger Non-Ferrous Metals – Ideally, the magnetic field should project into the centre of the non-ferrous metal particle. If this is an aluminium can or fragmented aluminium ball, a deeper field is needed. Commonly, this means that the magnets on the magnetic rotor are larger in size produced a deeper magnetic field with less magnetic poles;
- Separation of Smaller Non-Ferrous Metals – Smaller magnets and shallower magnetic fields are appropriate when separating smaller non-ferrous metals (eg aluminium flakes from plastic) with single particle burden depths;
Eddy Current Separator Blogs
In this series of technical blogs, we will examine a wide range of operational parameters of the Eddy Current Separator. This information has been obtained through extensive testwork at our manufacturing and test facility in the UK and on site.
For further information on Eddy Current Separators or metal recovery please contact us on:
Email: sales.redditch@buntingmagnetics.com
Telephone: +44 (0) 1527 65858
All photographs and illustrations are by Paul Fears Photography
Other Recycling related articles include:
- Eddy Current Separator Rotor Speed
- 3 UK Waste Recycling Facts;
- Could Aluminium Can Recycling Hit 85% By 2020?
- Ferrite or Rare Earth Overband Magnet?
- Recycling Lives Recovering Aluminium with Eddy Current Separators;
- Mastermag Help Finnish Waste Sorting;
- Mastermag Supplies ECS To Spanish Metal Recycler