Technical Explanation of the Magnetic Disc Separator
By Paul Fears | 07 November 2018
The origins of the Magnetic Disc Separator date back to the early 1900s. Although manufacturing techniques have significantly changed and more advanced machines have now been incorporated, the basic function design remains virtually the same. The Magnetic Disc Separator is widely used to ensure an accurate separation of dry minerals that have varied magnetic susceptibilities.
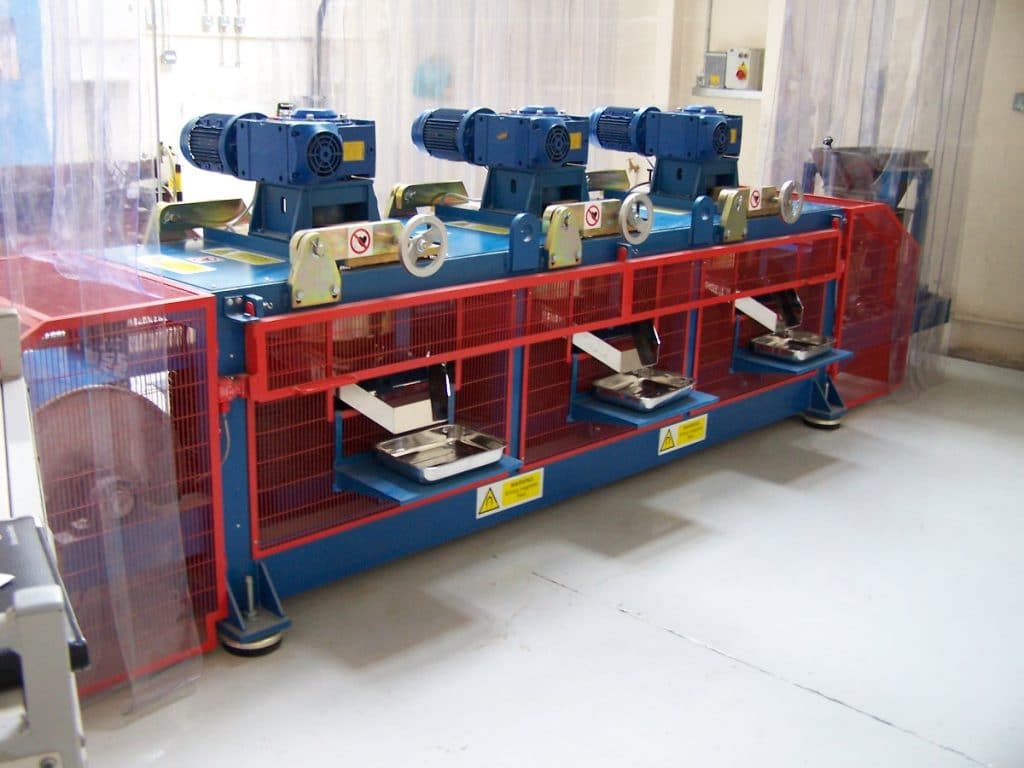
Magnetic Disc Separator Design
Typically, a Magnetic Disc Separator features up to three high-intensity electromagnetic discs, each set at a different height from a feed conveyor.
- Disc 1 – This will be set the furthest from the feed material. The objective is to extract only the most magnetically susceptible particles;
- Discs 2 and 3 – The second and third discs are set at lower gaps. This increases the magnetic force at each disc and enables the separation of different grades of magnetic material.
The magnetic intensity can be further adjusted by varying the current of each coil. This allows each Magnetic Disc Separator to be designed and set-up for an individual mineral ore.
The Methodology
In this video, Dr Neil Rowson, a respected mineral processing engineer from the University of Birmingham, explains the operation of a Magnetic Disc Separator.
On camera, Dr Rowson explains how feed material is discharged from a hopper onto a vibratory feeder tray. The vibratory feeder presents an even and thin layer of material onto a moving conveyor. As the material is conveyed under the rotating electromagnetic discs, magnetic particles are attracted up to the high gradient magnetic zones on the discs. The rotating discs then carry these captured particles to the discharge chutes where they are move into a non-magnetic area and are released. Scrapers mounted on chutes ensure the total discharge of magnetic particles.
Non-magnetic material continues to the second magnetic separation zone where secondary separation occurs, and is finally discharged at the end of the machine as a clean non-magnetic product. A third stage of separation can be added if required.
The physical action of the Magnetic Disc Separator lifting the magnetic minerals off the conveyor belt produces a very clean magnetic fraction.
Typical Applications
The Magnetic Disc Separator is used in many applications including:
- Beach Sands – Separating ilmenite, garnet, monazite, and zircon sand;
- Tin processing
- Wolframite recovery
- Abrasive minerals separation
- Tantalite and Columbite separation
Technical Video Presentations
Several technical video presentations by Professor Neil Rowson on the use of high-intensity magnetic separators in the minerals industry are available to view on the Bunting-Redditch website:
- Technical Video Explanation of the Induced Magnetic Roll Separator;
- Technical Explanation of Rare Earth Roll Separator
Related Mineral Processing Technical Articles
Magnetic Separators – Mineral Processing Laboratory
Bunting-Redditch has one of the most comprehensive magnetic separation mineral processing testing laboratories in the world. Their Laboratory Technicians have decades of experience in mineral processing. Controlled tests ensure that the most suitable and cost-effective machinery is recommended for each application. The laboratory is equipment with a wide range of equipment including:
- Smaller scaled versions of industrial Magnetic Separators. This equipment is used to accurately scale up to industrial capacities and calculate performance guarantees;
- X-Ray Fluorescence and X-Ray Diffraction analysis are available for chemical assay and mineralogical identification to aid the development of a viable process route for each application;
For further information on our range of magnetic separation equipment designed for purifying ceramics and non-metallic minerals, or to arrange sample tests in our laboratory, please contact us on:
Email: Gordon Kerr at GKerr@buntingmagnetics.com
Telephone: +44 (0) 1527 65858
To keep up to date with our news and technical reports, please follow us on social media