Metal Removed from Plastic Regrind
By Paul Fears | 03 March 2025
The combination of a magnetic separator and metal detector is removing rogue metal contamination from recycled plastic regrind before the material is mixed into other raw materials used for the manufacture of plastic products including handles and hinges.
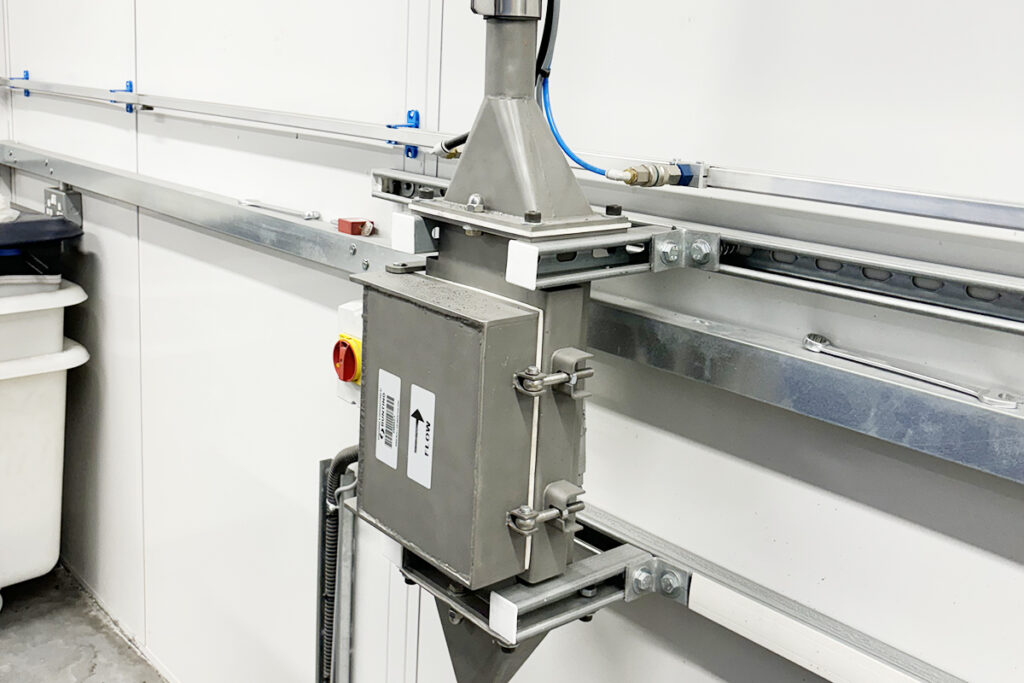
At the plant, waste generated from plastics injection moulders and in the manufacturing process is reground for reintroduction into the raw material feed. This significantly reduces waste and the demand for virgin raw materials.
The nature of plastic regrind means that there is always a possibility of contamination from metal. This could result in at least one production outage per month due to metal contamination damaging and causing blockages to processing equipment and proved costly both in production downtime and plant maintenance.
Following a site review by Bunting’s technical sales team, the manufacturer installed a magnetic separator followed by a metal detector on a 2” (50mm) diameter vacuum line from the injection moulding machines.
The plastic regrind first passes through a Pneumatic Inline Magnet (PIM). As the material flows through the body, the strong magnetic field of a ferrite plate magnet attracts and securely holds any tramp ferrous metal. This is a continuous process, with the captured ferrous metal being removed during scheduled maintenance on a frequency in accordance with the level of ferrous metal contamination. The PIM is designed for installation in pneumatic conveying systems with a top pressure rating of 15psi.
The regrind is then vacuum fed through a p-TRON 03 FM metal detector. Pipeline Style Metal Separators detect and then reject any metal, loose or encapsulated, from an enclosed pipe system. The metal detector has transmitter and receiver coils which generate an electromagnetic field, and when a metal particle enters the field the measured signal is deflected in one direction. When the metal particle leaves the magnetic field the signal is deflected in the opposite direction. If the detection thresholds are exceeded in both directions a metal signal is created, triggering the opening of a reject flap and redirecting the metal contamination into a separate waste collection bin.
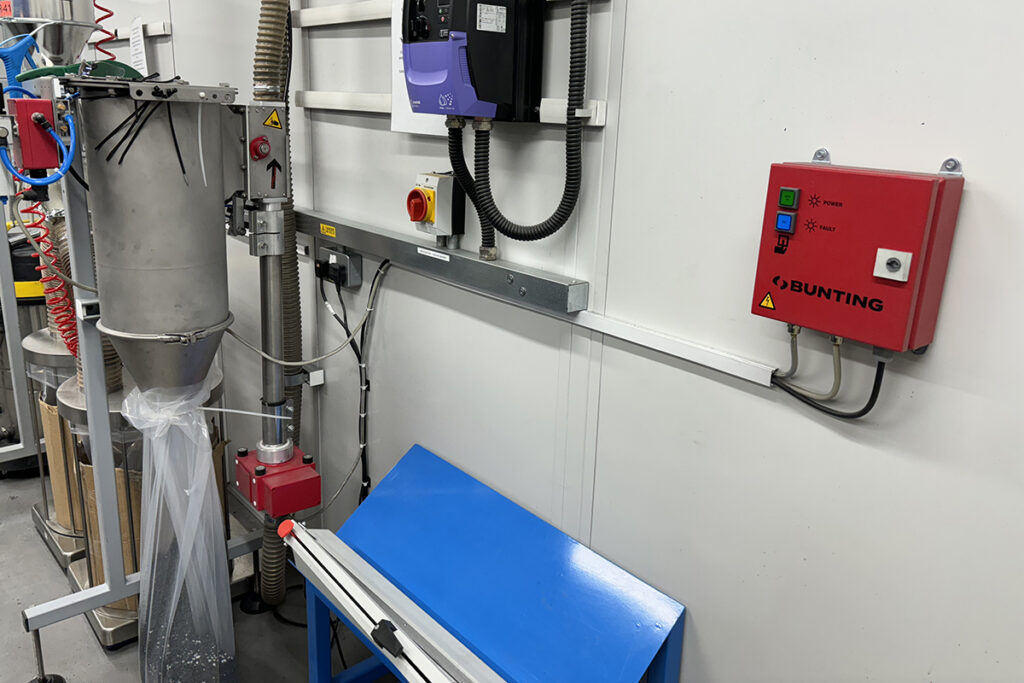
The combination of the magnetic separator and metal detector provides the optimum level of protection. Removing ferrous metal with the magnetic separator reduces the loading on the metal detector, lowering the numbers of reject operations and potential loss of product.
Since installing the magnetic separator and metal detector the manufacturer has eliminated issues related to metal contamination.
“Working with the customer and understanding the metal contamination problem provided the platform to determine the best solution,” explained Peter Buckley, Bunting’s Technical Sales Engineer. “And the combination of the magnetic separator and metal detector ensures that the plastic regrind is metal-free.”