Five Magnetic Separator Myths
By Paul Fears | 19 July 2021
Often ascertaining the best Magnetic Separator for any given application is not straightforward. To complicate the decision-making process further, many companies supplying magnetic separators provide a wealth of information such as Gauss levels and the amount of metal that the Magnetic Separator can actually capture. Such details are often difficult to verify and may even be meaningless.
In this blog, we aim to help potential purchasers of magnetic separators by explaining the technology and dispelling some of those myths.
Myth 1 – Use the Strongest Magnetic Separator
Strongest is always best, or is it? Commonly, companies will call and request a quote for the strongest Magnetic Separator. However, is that actually what they need? Moreover, what does ‘strongest’ actually mean?
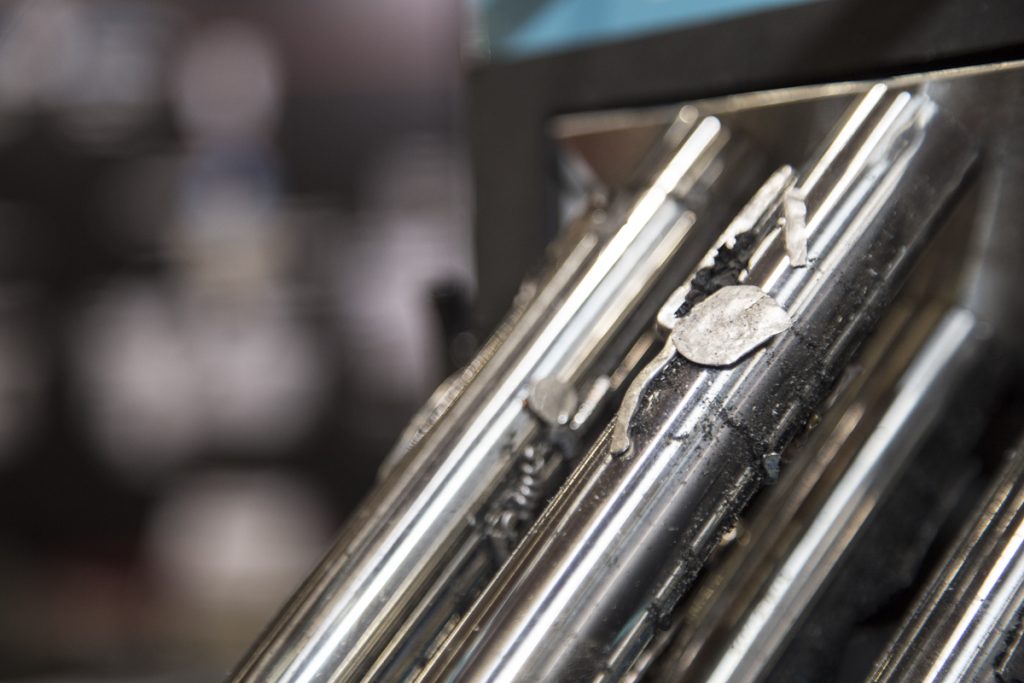
Before quoting for any magnetic separator, it is vitally important to understand the application fully. We commonly ask a range of questions such as:
- What is the metal that needs be magnetically separated? How big? How magnetic?
- From what is the metal to be magnetically separated?
- Why does the metal need to be removed? Is it to protect down-line processing equipment? Is it to recover the metal?
- How is the material being transported? Is it on a conveyor or as a slurry in a pipeline?
- What is the budget?
Armed with this information, the application can then be assessed by experienced engineers and a suitable design and strength of magnetic separation will be proposed.
However, do not be surprised if it is not the ‘strongest’ magnet.
Myth 2 – All Rare Earth Magnetic Separators Are The Same
A client has a metal contamination problem and needs to install the most suitable magnetic separation. The metal is small and so they believe that a Magnetic Separator with Rare Earth Magnets is perfect as it has the strongest magnetic field. The potential purchaser picks up the telephone and orders a Rare Earth Magnetic Separator and the problem is solved. Or is it?
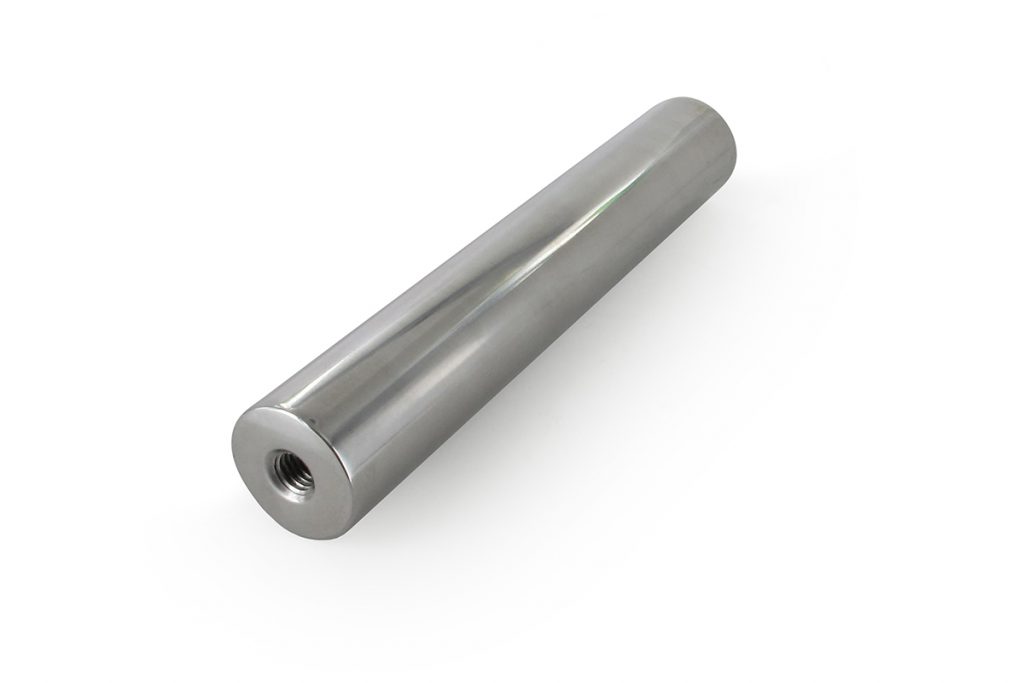
Unfortunately, the term ‘Rare Earth Magnet’ is unspecific. It is the same as ordering a car without specifying if it is a Mini or Aston Martin.
Rare Earth Magnets are strong permanent magnets made from alloys of rare earth elements such as Neodymium Iron Boron. Developed in the 1970s and ’80s, Rare Earth Magnets are the strongest type of permanent magnets presently available, producing significantly stronger magnetic fields than other types such as ferrite or alnico magnets. The magnetic field typically produced by rare earth magnets can be in excess of 1.4 Tesla, whereas ferrite or ceramic magnets typically exhibit fields of 0.5 to 1 tesla.
There are actually two types of Rare Earth Magnet:
The selection of Rare Earth Magnet depends on the application and we use the following as a general guide:
- Neodymium Iron Boron (Nd2Fe14B) – Unfortunately, life is never straightforward and there are two types of Neodymium Magnet:
- Sintered – These are produced using a high temperature process to produce a strong even and uniform bond of the material. This is the highest grade of Neodymium Iron Boron Rare Earth Magnet, producing surface fields of between 1 and 1.4 Tesla. Due to the higher specification, these are higher in cost;
- Bonded – These are weaker in terms of their magnetic properties. The materials are mixed and bonded using a synthetic resin or polymer. However, due to the manufacturing process the magnetic strength is lower (0.6 to 0.7 Tesla) and they are physically weaker. Bonded Neodymium Iron Boron is cheaper than sintered versions;
- Samarium Cobalt (SmCo5) – All Samarium Cobalt magnets are sintered and the magnetic fields produced range from 0.8 to 1.15 Tesla. However, these magnets are significantly more expensive than Neodymium Iron Boron, but they are ideal for very high temperature applications. Whereas standard Neodymium Iron Boron magnets are suitable for applications up to 80° C, Samarium Cobalt and high temperature Neodymium Iron Boron magnets maintain their magnetic integrity at higher temperatures;
In magnetic separation, the most common Rare Earth Magnets are Neodymium Iron Boron, but it is worth asking whether the magnets inside the Cartridge or Tube Magnet or Plate Magnet are sintered or bonded. High-quality magnetic separators use the sintered Rare Earth Material as it is physically better and produces a higher magnetic field. Asking the supplier to specify sintered or bonded helps the purchaser ultimately make the best decision based on price and, more importantly, the application.
Myth 3 – The Highest Gauss Magnetic Separator Is Always The Best
On a regular basis, we will receive an enquiry requesting a Magnetic Separator of a specific size. However, it is only when the enquiry also requests a specific Gauss figure that life becomes a little more complicated.
Frequently, the Gauss figure has been added to the enquiry with little understanding of the meaning of ‘Gauss’. It is a figure commonly quoted by companies supplying magnetic separators, but what is the relevance? Is 100,000 Gauss better than 10 Gauss?
‘Gauss’ is the cgs (centimetre-gram-second) unit of measurement of a magnetic field, which is also known as the ‘magnetic flux induction’ or the ‘magnetic induction’. One gauss is equal to one Maxwell per square centimetre.
However, does that really help or simply add to the confusion? In addition, does it help a purchaser understand if one Magnetic Separator is stronger than another?
There are several inherent problems with basing a magnetic separator purchasing decision on the ‘Gauss’ value alone.
- How do you know that the Magnetic Separator you are purchasing actually has the quoted level of Gauss?
- Even if you have a Gauss meter to measure the Gauss, have you had training?
- Where on the Magnetic Separator is that highest Gauss reading, as different levels of Gauss will be found at various points on the Magnetic Separator?
- The ability of the Magnetic Separator to capture metal particles is not only a function of Gauss alone and, in many cases, higher Gauss Magnetic Separators will not provide the best metal separation;
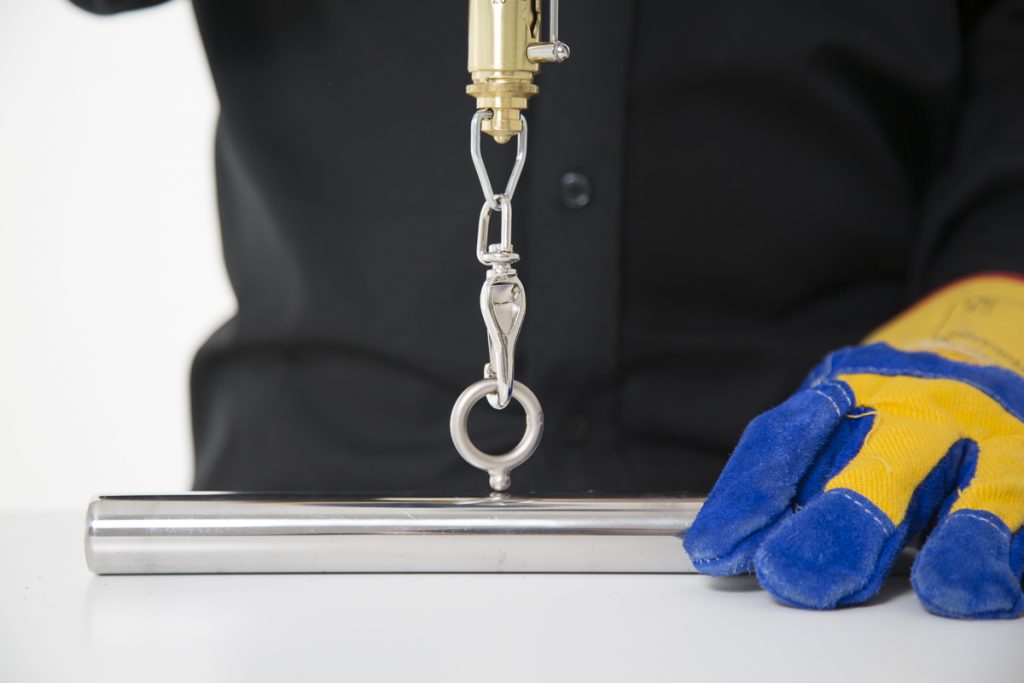
However, help is at hand! There is a simple way to assess and measure the magnetic attractive force on Magnetic Separators such as Tube Magnets, Grid Magnets and Plate Magnets. This physical test at least partly removes the ‘Gauss’ reading from the evaluation. The process is simple:
- Use a Spring Balance with a 3mm steel ball on the end;
- The Steel Ball is placed on the surface of the Magnetic Separator;
- The Steel Ball is then pulled away and off the Magnetic Separator;
- A reading is taken on the Spring Balance (in kilogrammes). This is the breakaway force;
- The test is repeated at several locations on the Magnetic Separator;
By conducting this test, you know have a real tangible figure than means something. You can conduct the same test on other Magnetic Separators and then you will be able to confirm which Magnetic Separator requires the highest kg force to extract the Steel Ball from the Magnetic Field.
As part of the internal auditing system, the Magnetic Separator test can be repeated at regular intervals to ensure that the Magnetic Separator is not losing strength. It is a simple and very effective method of assessing the magnetic strength of smaller Magnetic Separators and does not need extensive training using costly and high tech equipment.
So, if magnetic force is important when requesting a price for a Magnetic Separator, it is recommended that you do not only state the ‘Gauss’ level but also ask for the number of kilogrammes needed to pull the 3mm steel ball from the surface. Then, on receiving the magnetic separator, conduct the pull test to check that the purchased equipment meets the ordered specification.
- Technical article: Measuring Magnetic Separator Power
Myth 4 – Magnets Lose Strength Over Time
It is a question we frequently are asked: when will the Magnetic Separator start losing its magnetic strength? In normal operating conditions, a magnetic separator will not lose any magnetic strength. However, there are occasions when other factors do affect the magnetic strength.
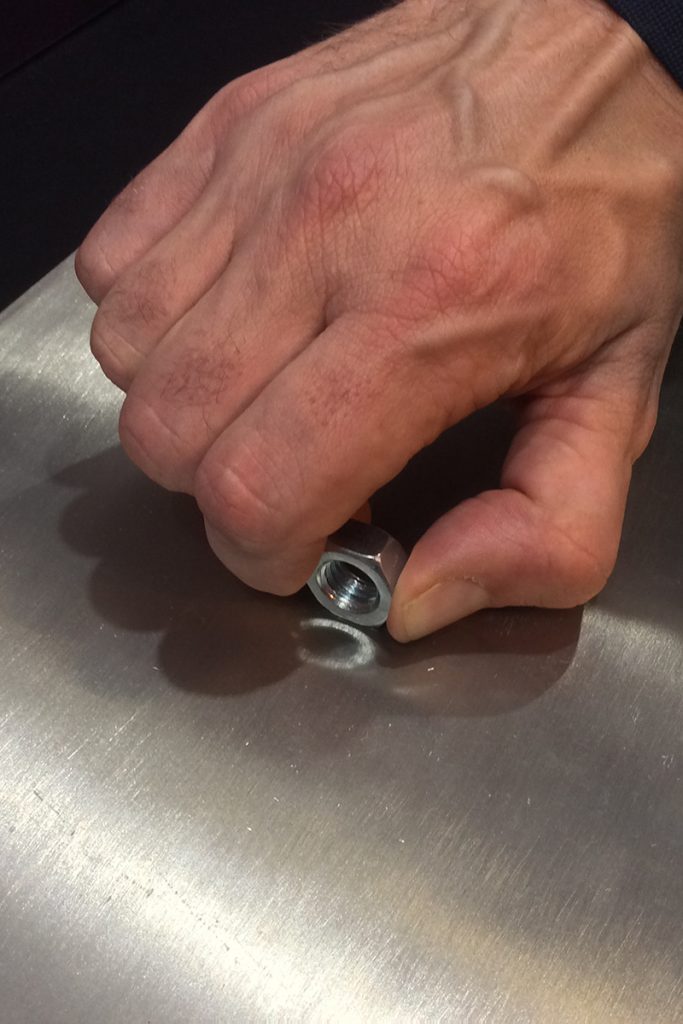
- The use of bonded Rare Earth Magnets. These are lower in cost to manufacture and therefore cheaper to purchase. Many companies, stating that the magnets are ‘Rare Earth’, supply them. However, as the magnet is only bonded (i.e. bonded together using a resin) it is not as strong or stable as being sintered. ‘Ceramic’ Rare Earth Magnets, that have been produced using heat, are more stable and are what Bunting and other reputable magnetic separator suppliers use in their magnetic separators. Of course, Bonded Magnets are ideal for many other applications;
- Physical damage. If a Magnetic Separator is dropped or hit, then this can result in the magnets inside breaking and this will affect the magnetic power. Such damage often occurs when a Magnetic Separator is being cleaned. Unknowingly, the Magnetic Separator is returned to the process line with the operator totally unaware that the magnetic separation capabilities have been seriously compromised. Regular checks on the magnetic strength of the Magnetic Separators is recommended as part of an annual review and audit;
- Exposure to heat. When Rare Earth Magnets are exposed to heat over 80°C, there is a reduction in the magnetic strength. When the temperature reduces, the magnetic field can recover. However, if the temperature is very high then the magnetic strength will never recover back to the original state. Typically, Magnetic Separators are exposed to high temperatures if a process line is being cleaned using steam. There are special Rare Earth Magnetic materials that are specially produced for high temperature applications, with Samarium-Cobalt being used in extreme circumstances;
Understanding the ability of a Magnetic Separator to retain magnetic strength will help during the purchasing and maintenance processes.
Myth 5 – We Guarantee 100% Metal Separation
In the perfect world, installing a Magnetic Separator will enable 100% metal separation with 0% product loss. However, is this even remotely possible?
Often as part of a project specification, there will be a question asking about the level and percentage of metal separation. In some projects, the expected metal separation target is even stated.
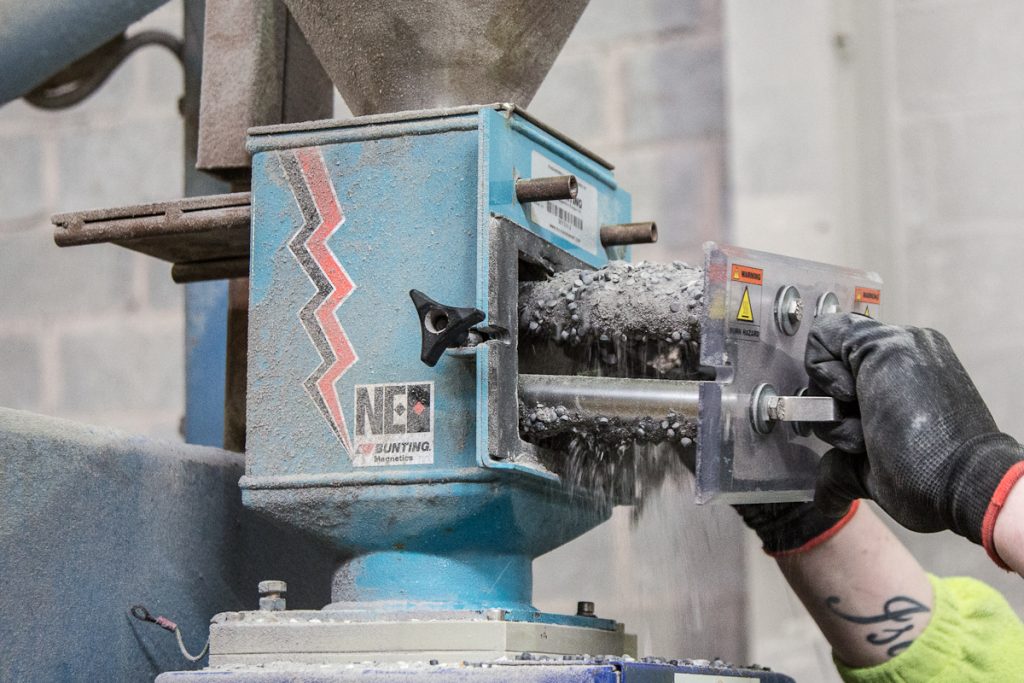
The response from Magnetic Separator suppliers will include a statement regarding the level and percentage of Metal Separation, often without any qualification. So what should the answer be?
There are a number of questions that need asking before the level of Metal Separation can be estimated:
- What is the Metal Separation objective? Is it to remove problematic metal and protect processing equipment as when processing food, pharmaceuticals, or plastics? On the other hand, is the aim to recover as much metal as possible, which may be the objective in a recycling operation?
- How much product or non-metallic material can be lost? The non-metallic material might be the product or it could be the waste. It is commonly found that higher metal separation rates are often accompanied by a higher loss of the non-metallic materials;
- What purity of end product is required? In recycling, the aim is to achieve recovery of metal, but at what point does the value of the recovered metal become affected by the level of contamination? In the food and plastics industry, the final product quality is paramount;
- How is the stated Metal Separation figure in terms of separation and/or purity monitored once the equipment is installed? Commonly, very high separation percentages are quoted by suppliers as it is well recognised that once the equipment has been installed the actual separation rate will never be checked;
Just asking these four questions enables a good initial assessment of the application. Then it is possible to make a recommendation in terms of the design of Magnetic Separator, as well as the mode of installation and operation.
Importantly, if a Metal Separation target is a key part of the contract, ensure that there is an agreed process to check the level of separation once the Magnetic Separator is installed.
Concerning the original statement, ‘We Guarantee 100% Metal Separation’, this is a claim made by only the ill advised. Processing any material can be carefully controlled, but is always subject to variations that can affect any part of the process including the level of metal separation. Even by installing an infinite number of magnetic separators of different designs, achieving a 100% Metal Separation is simply a myth.
Related Technical Article
For further information on Magnetic Separators, ElectroStatic Separators and Metal Detectors or to discuss a specific project including undertaking tests in our Customer Experience Centre, please contact our technical sales team on:
Email: Gordon Kerr at GKerr@buntingmagnetics.com
Telephone: +44 (0) 1527 65858
All photography by Paul Fears Photography
Follow us on social media